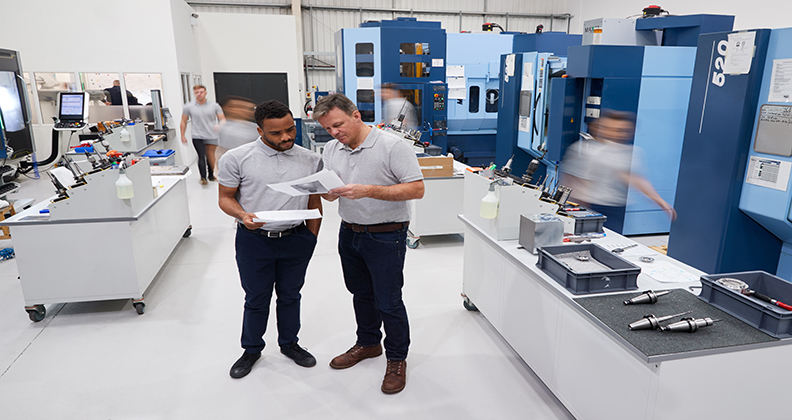
There’s a lot that goes into turning expertly engineered designs into finely crafted orthopedic devices. Successful operations managers strike a balance between reducing costs and reacting to fluctuations in demand while looking for ways to improve the manufacturing process.
Edward Jaeck, President and Founder of the consulting firm SINE18, helps orthopedic manufacturers build continuous improvement processes into their manufacturing methods. The technology operations and quality assurance expert said efforts to level up manufacturing processes should begin with determining current capabilities. He suggests mapping out every aspect of current operations.
“How do you compare a new process against standard methods?” Jaeck asked. “You need to analyze data to figure that out, and that data analysis often involves multivariate optimization.”
Optimization Fuels Efficiencies
The goal for any orthopedic factory manager is to maximize profit, which sometimes involves slowing down a process to increase yield and profit, according to Jaeck. Other times it requires taking a minor yield hit by speeding up the process. Each product is different, and each product impacts the factory system differently.
Once you have an accurate assessment of volume capabilities, dig into the data to determine the highest-volume, longest-running parts — these are the parts in the factory that take the longest time to produce, Jaeck said.
“Streamlining the production lines of these parts provides the biggest opportunity to achieve better throughput and improve quality and maximize profit,” he added.
Streamline cycle times for long-running parts by determining which elements of the manufacturing process are critical and which non-critical steps can be combined or automated without sacrificing quality, Jaeck advised.
He explained that a key element of optimized manufacturing operations involves building continuous improvement into workflows, which requires allocating time and resources accordingly. He added that continuous improvements in an operational strategy are achieved by identifying potential growth areas and capitalizing on them through experimentation and innovation. No customer wants to come to a contract manufacturer and be told, “We don’t have that capability, but we can develop it on your dime.”
For example, Jaeck highlighted the benefits of learning a CNC machine’s top performance threshold through experimentation. Running CNC machines as fast as they can safely operate determines their true capacities — and limitations.
Doing so also shows machinists how aggressive they can be in cutting pieces efficiently and effectively. Machinists should understand the impact their work has on the bottom line, so they are more aware of the relationships between throughput, cost and quality. It demands striking a balance.
“After an analysis, you can see where inefficiencies exist and then test the performance of new tooling, speeds and feeds to optimize the process,” Jaeck said. “Continuous improvement is asking every year or even every month, ‘How do we build on what we’re already doing?’”
Maximizing Capacity
Brett Gopal, Senior Vice President of Operations at SpiTrex Orthopedics, always looks for ways to build efficiencies into his company’s manufacturing processes.
“There’s plenty of opportunity for optimization in terms of bridging the gaps between processes and creating one-piece flow wherever possible,” Gopal explained. “When one-piece flow is not possible, work to fill a smaller run batch that primarily becomes a pacemaker of the workcell.”
Gopal noted that some manufacturing processes can be combined based primarily on value streams, regardless of the type of part being manufactured. “All parts have different processes, whether it’s forging or testing or machining,” Gopal said. “Bringing those processes closer together is a great opportunity for optimization.”
Gopal said unlocking the full capacity of machining equipment leads to higher productivity and savings, and he recommended automating as many processes as possible within an operational strategy.
“You can take manufacturing to the next level by integrating inspection into the automated process to generate a rapid feedback loop with software applications and machine learning,” Gopal said. “This enables a lights-out operation that’s able to run from Friday night through Monday morning.”
SpiTrex recently partnered with the robotic automation company Flexxbotics to add robot-driven manufacturing capabilities with autonomous process control to its FOBA laser marking machine workcells. The technology enables robots to communicate directly with the FOBA laser marking system and change jobs in real-time and within sequence, reducing job changeovers to just 10 minutes instead of the hour or so it takes an engineer to set up a new workcell.
“The autonomous changeover process coupled with the closed feedback loop functionality enables us to produce extremely high tolerance parts through continuous flow, which reduces the overall lead time by more than 20%,” Gopal said. “That directly improves our throughput, which in turn increases profitability.”
Adding the Flexxbotics platform to each of SpiTrex’s FOBA laser marking workcells resulted in a 10:1 machine-to-man ratio, which enables continuous operation and allows the company to ship more high-quality parts, even in the face of labor shortage challenges. The platform also horizontally integrates one FOBA machine to another and vertically integrates to the company’s pre-machining process, post-process and IT systems.
“We’re impressed with the platform’s autonomous process control and its ability to close the loop by alerting upstream and downstream workcells of quality problems based on automated inspection results,” Gopal said.
He recommends automating and integrating quality and safety inspection at the point of manufacturing, explaining that it’s a strategy that saves time and money.
“Traditionally, products were manufactured and then moved into the quality control lab, waiting for inspection and to go through verification to determine if issues needed to be addressed,” Gopal said. “It was a manual sorting process that determined which devices could go through the next sequence of finishing processes.”
Integrating inspection into the point of manufacturing provides a faster feedback loop, Gopal noted. He added that if machine operators need to make an offset, they’re able to guarantee the adjustments made to the machine’s coordinates will be on-spec.
Embracing Challenges
Gopal mentioned that “servant leadership” is important in his role. He explained that instead of telling his team members what needs to be done, his focus as a project manager is to ask the right questions to find optimal solutions.
“We try to encourage our people on the floor that problems are treasures,” Gopal said. “The more we embrace the issues that arise, the more we’re going to have a positive outlook for working through them instead of trying to hide them.”
When that type of language is used more consistently, and the next level of management hears it, it is easier to start looking at problems. “And when they start speaking with middle-level management or operators on the floor or with production supervisors,” he said, “the optics of looking at the problem completely changes.”
PM
Patrick McGuire is a BONEZONE Contributor.