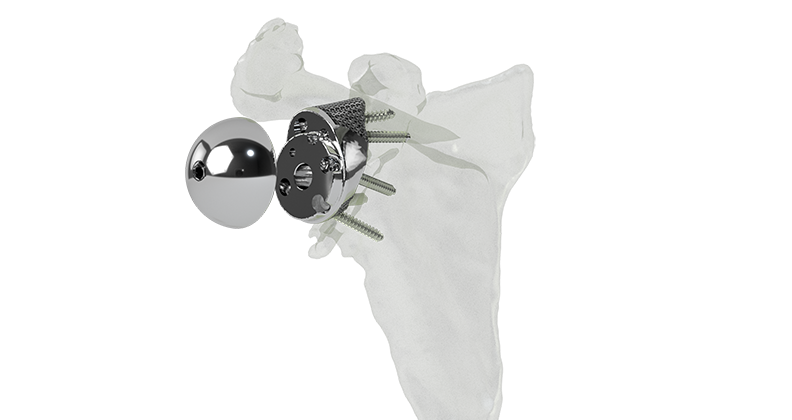
The potential application of additive manufacturing in orthopedics was more pipedream than possibility until 2007, when Dr. Guido Grappiolo became the first surgeon to successfully implant a 3D-printed titanium hip implant in a patient.
Since that landmark case, additive manufacturing has emerged as a truly game-changing technology. The ability to produce personalized implants made of intricate structures that perfectly match a patient’s anatomy and promote bone growth is reimagining how complex surgeries are performed. Additively manufactured patient-specific instruments and implants are being produced in parallel to the industry-wide movement toward more personalized care.
Cambre Kelly, Ph.D., Chief Technology Officer at restor3d, said additive manufacturing creates complex geometries that are not achievable with traditional machining. The potential to enhance osseointegration, improve implant stability and reduce the risk of implant loosening has inspired a wave of additively manufactured orthopedic devices.
Today, additive manufacturing is used to enhance a host of surgical procedures, from trauma and fracture fixation to sports medicine and joint replacements. And it’s not just the implants that are getting the 3D printing treatment. Surgical guides and instruments are also being manufactured with additive techniques in the ever-growing search to create the perfect procedure for every patient.
Still, additive manufacturing in orthopedics remains in the early adoption phase and the industry is just starting to realize its true potential. As more companies continue to conduct research and develop innovative products, many 3D-printed devices could have comparable or superior outcomes to those made with traditional manufacturing methods, according to Dr. Kelly.
“Additively manufactured products have been on the market for a relatively short time and the evolution has been truly incredible,” she said.
Orthopedic manufacturers have taken notice of a growing trend that will inevitably evolve into standard practice. “Every device we sell — for hips, knees, ankles and shoulders — has some components made with additive manufacturing,” said Chris Roche, Senior Vice President of Extremities at Exactech.
That’s quite the endorsement for a technology that’s only begun to scratch the surface of what’s possible in the advancement of patient care.
Personalized Solutions
The advantages of digital implant designs and rapidly evolving enabling technology have enabled the transformation of patient-specific orthopedic solutions.
Dr. Kelly said this movement has resulted in “scalable personalization,” which involves surgeons seeking solutions tailored to the unique anatomy of their patients.
For example, complex joint reconstructions often involve significant bone deformity, rendering inadequate a few-sizes-fit-all approach to implant selection. “That concept doesn’t make a lot of sense,” Dr. Kelly said. “Patients want the best possible care, and that involves instruments and implants customized to fit their anatomy and match the goals and objectives of their surgery.”
Additive manufacturing’s unique properties make the creation of patient-specific implants possible. Traditional manufacturing methods like molding and machining are cost-prohibitive for such personalization, according to Dr. Kelly.
Exactech has collaborated with Materialise, which specializes in software solutions and 3D printing services for the medical industry, to increase access to personalized shoulder implants in Europe and Australia. The companies produce 3D-printed glenoid implants for cases involving significant bone deformities that require a more effective solution than what’s possible with off-the-shelf products.
Materialise’s clinical engineers design each implant based on a patient’s anatomy using 3D data, simulation and artificial intelligence. The result optimizes the fixation and stability of the implant while maximizing bone preservation for more predictable outcomes.
“Demand is growing for personalization of medical devices,” said Brigitte de Vet, Vice President of Materialise. “Orthopedic companies adopt mass personalization by starting with high-value cases and moving toward more high-volume applications.”
This overall trend may drive the orthopedic market toward the adoption of patient-specific implant kits. “Every procedure could eventually include preoperative planning and personalized 3D-printed implants and instruments,” Roche said. “Companies would create kits that include only what’s needed for an individual case.”
The personalization of surgical instruments and patient-specific implants is also increasing as more cases move to ASCs, where surgeons and staff want access to convenient and disposable instrumentation that streamlines surgical workflows.
“I think additive manufacturing will grow in popularity as facilities transition to disposable surgical tools that don’t require storage or sterilization,” said Ben Holmes, Ph.D., CEO of Nanochon.
Creating Complex Designs
One of the key advantages of additive manufacturing is the freedom of design it provides, which allows for the creation of complex lattice structures, porous surfaces and optimized internal architectures — features that promote osseointegration, reduce an implant’s weight and improve its mechanical properties.
Additive manufacturing also allows for the utilization of a wide range of materials suitable for orthopedic implants, including biocompatible metals like titanium and cobalt-chrome alloys, biodegradable polymers and bioactive ceramics.
Dr. Kelly emphasized that additive manufacturing has revolutionized the production of complex porous structures, such as lattice designs, which were previously impossible to manufacture without 3D printing. These lattice structures optimize implant performance by providing load reinforcement in areas with higher stress and reducing stress in areas with lower loads.
At restor3d, implants that require bone ingrowth incorporate the company’s proprietary TIDAL technology, an interconnected porous architecture created by a lattice. This design optimizes ingrowth and fixation, ensuring long-term implant stability.
Materials used in additive manufacturing vary, though 3D-printed titanium is commonly applied in implants that require a porous surface for bone osseointegration. Roche said that many implants on the market are made of titanium, particularly for bone-facing components, because of additive manufacturing’s capability to selectively apply porous coating where it’s needed. “Additively manufactured implants with porous coatings have more potential for ingrowth,” Roche said.
The Kinos Axiom Total Ankle System made by restor3d is an example of leveraging 3D printing to optimize implant surfaces for applications in specific procedures. The system combines porous structures for bone ingrowth and polished surfaces for articulation, which leads to an implant that mimics the movement of a natural, healthy ankle.
“The ability to create porous areas needed for bone ingrowth and polished surfaces for articulation in the same implant is incredible,” Dr. Kelly said.
Dr. Holmes highlighted Nanochon’s focus on optimizing the material used for its Chondrograft knee implant, a load-bearing device and tissue growth scaffold that is placed arthroscopically. While years away from FDA approval, it’s expected to be a game-changer for younger, more active patients who suffer from osteoarthritis but aren’t ready for a joint replacement.
The Chondrograft implant consists primarily of a unique polymer, predominantly biodegradable nylon, that simulates collagen bundles to aid in cartilage rebuilding. “Additive manufacturing allows us to create a 3D porous structure that is not possible with traditional manufacturing,” Dr. Holmes explains. “Our material essentially maintains a collagen-like nanostructure.”
Optimizing Time to Market
Rapid prototyping and iterative design processes facilitated by additive manufacturing can lead to reduced time-to-market for complex, personalized orthopedic implants. The ability to quickly respond to market demands and introduce innovative solutions is a significant benefit.
Dr. Kelly said insourcing additive manufacturing capabilities has been the right decision for restor3d. Housing the manufacturing components under one roof allows the company to be a full-service provider. Company reps meet with surgeons to discuss their specific clinical needs for a particular surgery and deliver 3D-printed implants and instrumentation in roughly four weeks.
“It’s helpful for us to be agile and in control of what we print and when we print it,” Dr. Kelly said. “Our team also benefits from understanding the capabilities of the technology. We see firsthand how the machines run and how they work.”
The use of additive manufacturing technology makes offering a variety of implant sizes and shapes much more possible than in the past. Device manufacturers and their R&D teams are no longer confined to specific molds. They can also scale production runs. “It’s not difficult to model a range of implant sizes and then make those components without using any unique tooling,” Roche said.
Foundation for Future Growth
Though the evolution of additive manufacturing has been eye-opening, the technology is still not a cost-effective option for use across all orthopedic procedures. “Certainly, in the commercial space, desktop plastic printers were really expensive a decade ago and now they’re much more affordable,” Roche said. “Down the line, 3D printing can lower costs in the medical device space.”
Eventually, Roche added, additively manufactured patient- and procedure-specific instruments and implant kits could make the technology more cost-effective and widely adopted. “That would change the economics and open the door for many more applications,” he added.
While challenges and cost considerations remain, the potential for additive manufacturing to reshape the orthopedic device landscape is undeniable. As the industry continues to embrace this innovative approach, patients and surgeons can look forward to a future in which personalized, efficient and effective orthopedic solutions become the norm.
“We’ve proven that additive manufacturing works,” Dr. Kelly said. “Now we have to make the technology more scalable, capable of plug-and-play applications and not as burdensome to incorporate into product development.
“There are going to be a lot more devices that will come through the additive manufacturing pipeline because the foundation for success has been set. That’s what I’m excited about.”
KK
Kendal Kloiber is a contributing editor.