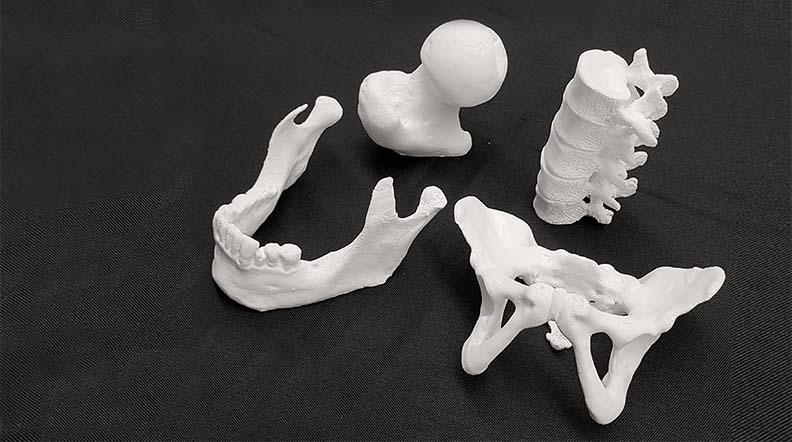
Additive manufacturing has transformed orthopedic device manufacturing and is poised to continue to deliver sweeping changes in the decades to come. To learn more specifics, we interviewed four experts positioned with different perspectives on the industry. Not surprisingly, predictions focused on significant shifts toward personalized implants, faster machines and enhanced materials. Of course, to see some of these predictions to fruition, orthopedics must overcome regulatory and healthcare infrastructure hurdles.
To provide context, we spoke to:
- Benjamin Johnson, Vice President, Portfolio and Regulatory, 3D Systems
- Andy Elsbury, President, Nexxt Spine
- Adam Jakus, Ph.D., Co-Founder and CTO, Dimension Inx.
- Andy Christensen, additive manufacturing, entrepreneur and veteran
With a focus on transformative technologies within the medical device industry, Benjamin Johnson is the Vice President, Portfolio and Regulatory at 3D Systems. Johnson predicted three major trends when asked how additive manufacturing would evolve in orthopedic technology over the next 20 years.
“First is in the hardware, with the print systems and the printers themselves becoming more productive and reliable. Here at 3D Systems, we’re investing in production printer systems that can improve print speed and maintain our best-in-class quality of the printed part that comes off of the printer. And that’s in terms of dimensional accuracy, mechanical properties and surface roughness.”
Ultimately, investments in advancing machine technology will lead to lower production and part costs.
“The second advancement is going to come from software and software tools that are used to design and simulate, build and manage the entire additive manufacturing workflow,” Johnson said. “I think we’ll see advances that leverage technology such as artificial intelligence to connect the dots between each step of the additive manufacturing process and to also provide a feedback loop to inform and adjust the process as conditions change again, leading to increased productivity from that workflow.”
The third trend that Johnson identified was the continuation of advancements in materials capabilities.
“We anticipate that material development that targets specific applications in the regulated industry we’re in that meets performance criteria and complies with material standards will continue to evolve in the future,” he said. “Today, we find ourselves working on materials that are commonly used in medical devices, such as titanium and titanium alloys, stainless steel, cobalt chrome and nylon. But I suspect in the future we’ll start to see material development of novel metallic alloys and polymers that are made possible by additive manufacturing processes that perform even better than the offerings that we have today from a material standpoint.”
According to Johnson, the additive manufacturing advancements he predicted are likely to usher in an era of accelerated innovation and lower costs in orthopedics and healthcare, broadly, with underserved populations likely to receive significant benefits. He also envisioned a future of personalized medical implants and point-of-care 3D printing services set up at hospitals with tools and implants printed on-site for specific surgeries.
The OEM perspective we sought out said that major changes would need to occur in the industry before prediction of patient-specific additive manufacturing services becoming available at most hospitals. Andy Elsbury is the President of Nexxt Spine, a spinal implant company that uses additive manufacturing technology to build its products. When the topic of hospitals hosting additive manufacturing services was broached, Elsbury listed significant challenges.
“Sterilization to accommodate this is currently done in a building that’s about the size of a football field, so that’s one obstacle. If FDA changes its allowable sterilization methodologies, then it could move into a hospital. There are also some heat-treating processes that are facilitated in equipment that’s about the size of a pickup truck. That’s going to be kind of cost-prohibitive for a hospital to pick up. There are also machining centers to consider, because we do some machining with these as well. Those are all obstacles. These elements have to be able to come apart and go right into the hospital.”
While Elsbury didn’t think that hospitals could surpass these challenges to host 3D printing processes anytime soon, he did say that the additive manufacturing technology and regulatory climate would soon allow for customizable orthopedic implants to be printed, sterilized and delivered in as little as two days. Currently, it takes two weeks to achieve this, Elsbury said.
When asked what potential advancements in additive manufacturing technology excited him the most, Elsbury said that a plethora of “completely different” materials were likely to be used in 3D-printed orthopedic devices in the coming years.
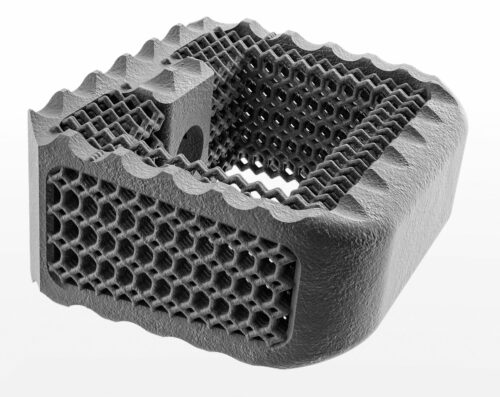
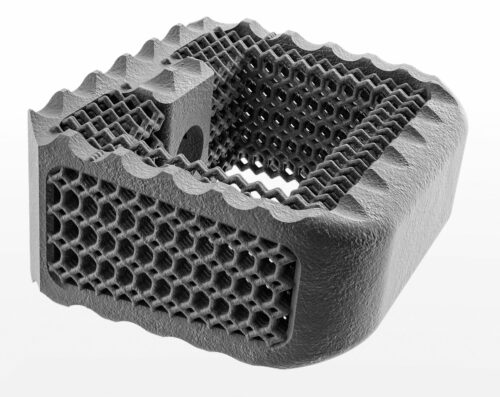
Nexxt Step additively manufacturers its cervical cages.
Adam Jakus, Ph.D., is the Co-Founder and CTO of the medical technology company Dimension Inx. Dr. Jakus has a specific interest in designing regenerative biomaterials for 3D printing and additive manufacturing. He shared his thoughts on how he thought additive manufacturing in orthopedics would shift over the next two decades.
“Metal additive manufacturing has now become pretty mainstream,” he said. “Orthopedics is the big field in terms of volume and number of patients served, and I think metal additive is here to stay in orthopedics for a long time. I think what you’ll start to see is a lot of new additively manufactured metal products that really take advantage of additive manufacturing. I’m starting to see a lot of really unique types of style cages that are possible through additive. And then we’re seeing a lot more in the orthopedic space, particularly in trauma with complex patient-matched 3D-printed metal devices. I think you’re only going to see more of that. It’s become mature now, and it’s only going to get better.”
Dr. Jakus was careful to point out that metals in orthopedics had limitations, and that additive manufacturing technologies were likely to seek alternative materials in the coming years.
“Metal is not the answer to everything,” he said. “A lot of metal is being used that’s good for structural and mechanical support, such as orthopedic implants, but they’re not particularly regenerative. They are very difficult to use with pediatric patients because metal doesn’t grow with them. So, a lot of the big players in the space are starting to look ahead beyond metal to regenerative materials and regenerative devices that can be used on their own or in conjunction with metals.”
Dr. Jakus predicted that many more 3D-printed tissue regenerative products would be available in orthopedics within the next five to 10 years, such as demineralized bone matrixes and resorbable ceramics. The next 10 to 20 years will deliver an even more complex set of 3D-printed products that will leverage stem cells, said Dr. Jakus. When asked what posed the greatest challenges to making these new additive advancements a reality, Dr. Jakus cited regulatory issues and complacency on behalf of orthopedic surgeons as major factors.
“But a lot of the younger surgeons are very intrigued with the new technologies out there, and even a lot of them in medical school now and in residency are being trained in, or at least exposed to, 3D printing,” he said. “I think what will impact this the most is the number of younger surgeons and orthopedists just getting into the space who are not set in their ways as much, so it’s just a matter of time.”
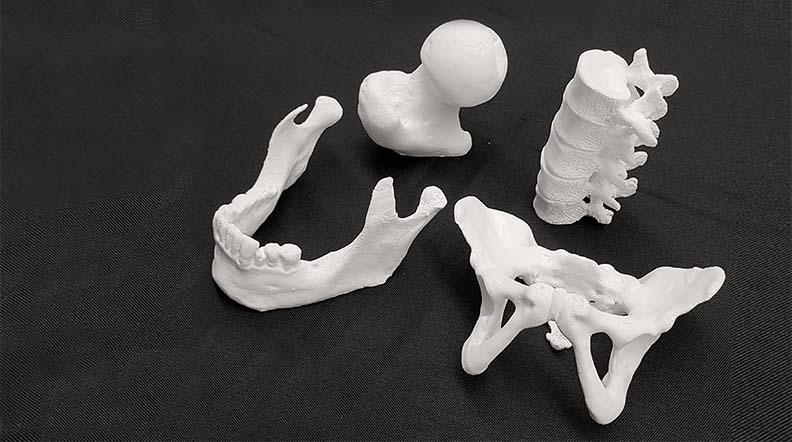
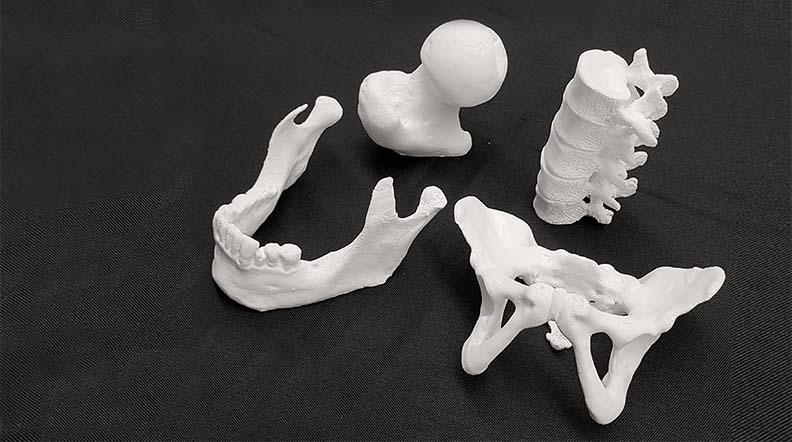
Dimenion Inx. focuses on regenerative biomaterials for additive manufacturing and 3D printing.
Andy Christensen’s professional background in additive manufacturing dates back to the mid-90s. One of the most important parts of Christensen’s work was taking data from various CT scans and trying to turn them into something that could be printed. He served as Founder and President of Medical Modeling Inc. from 2000 to 2014, when it was sold to 3D Systems. He is now Adjunct Faculty in the Department of Radiology at the University of Cincinnati and known as an additive manufacturing entrepreneur and veteran.
Christensen predicted shifts in orthopedic additive manufacturing ranging from faster processing speeds that will cut healthcare costs to specialized knowledge of how to use the technology spreading to smaller companies that are currently outsourcing their 3D printing needs. He also pointed to an industry where 3D-printed implants that are more personalized will become the norm.
“I think the trend toward the use of additive to produce serial parts for hip, knee, spine and other areas will definitely continue,” Christensen said. “Additive has been really good for small parts, but it’s more challenging for large parts to make the economics work. But I think what you’ll see is larger parts becoming financially feasible.”
Moving on to the topic of personalization in additive manufacturing, Christensen noted that personalization has become a buzzword in orthopedics, thanks in part to robotics.
“Surgical robotics is pushing further the ability to do something more personalized because most of the systems allow for pre-planning. And then, instead of using a 3D-printed guide, template or a personalized implant, the robot helps transfer the surgical plan to the patient. Given how hot robotics is, I think that story is going to help raise the whole industry’s awareness of personalization, and of what can and should be demanded by patients.”
Christensen predicted that a combination of improved additive manufacturing technologies and broader 3D printing knowledge would be critical in addressing the current challenges holding custom implants back in orthopedics.
“I think what we’ll see is more personalized implants beyond what we have available today. If you’re making thousands of some part, you can take the time to really dial the process in and have reliable production output. But if you have to make one part and it has to come off fairly quickly and needs to be right, it turns out to be quite a bit more challenging. A lot of knowledge goes into how to design a part for additive that will come out the first time and be ready to go. I think that process is getting better, becoming more reliable. And if the machines are faster, that whole workflow can eventually come down to where you can do personalized implants on a volume basis.”
The adoption of new technologies by orthopedic surgeons and hurdles put forth by regulatory bodies make guessing what might happen over the next two decades difficult. However, the orthopedic industry, along with surgeons and regulatory and standards bodies are currently researching and debating the future of custom and on-site built implants as well as new materials that will extend implants to soft tissue needs. All of which is worth noting for OEMs seeking to advance their use of additive manufacturing.
PM
Patrick McGuire is a BONEZONE Contributor.