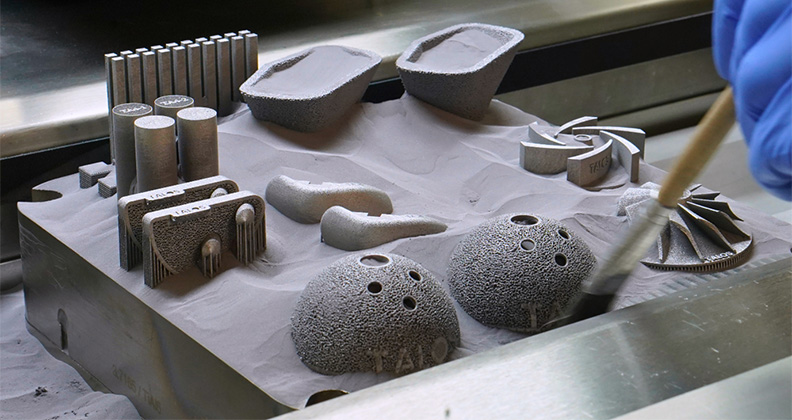
Croom Medical introduced the TALOS technology platform, developed in collaboration with Global Advanced Metals (GAM). TALOS is specifically designed for 3D-printing tantalum components across diverse industries, including medical applications, using advanced laser-powder-bed-fusion.
Tantalum is renowned for its exceptional biocompatibility, corrosion resistance, and high normalised fatigue strength, making it ideal for medical implants. However, its processing challenges have historically limited its widespread use. The TALOS platform overcomes these obstacles, enabling the production of complex, porous, strong and lightweight tantalum structures for medical device applications.
Dr. Shane Keaveney, R&D Manager at Croom Medical, highlighted the significance of this advancement. “Tantalum has long been valued for its outstanding biointegration, corrosion resistance, and mechanical properties. With TALOS, we unlock these intrinsic qualities, allowing precise control over implant ductility and strength to closely match native bone.”
TALOS is now commercially available through Croom Medical’s contract manufacturing services, supporting customer projects from prototype to volume manufacturing. Precise control over tantalum printing parameters and cellular lattice structure design enables engineers to tailor implant ductility, elastic modulus and strength to match native bone. TALOS achieves densities up to 99.99% and delivers highly open porous structures ideal for medical device applications. Furthermore, AM-optimised tantalum is achieving over 40% elongation, reducing fracture risk and enabling complex, flexible designs.
A feature of TALOS is its ability to directly print tantalum onto titanium substrates, merging titanium’s lower density with tantalum’s osteoconductive capacity. This hybrid approach holds the potential for implants with enhanced bone fixation, representing a significant step forward in reducing the need for revision surgeries.
Sustainability is a core aspect of the TALOS platform. It uses ethically sourced, conflict-free tantalum powder supplied by GAM, supporting a closed-loop recycling process. “After 3D printing, leftover powder from Croom Medical is returned to GAM, where it undergoes rigorous refining and reprocessing before re-entering the manufacturing cycle. This approach maximises material efficiency and ensures a secure, consistent supply of tantalum,” explained Dr Gordon C. Smith, GAM’s CTO.
Patrick Byrnes, CEO of Croom Medical, emphasised the company’s commitment to advancing manufacturing technologies. “TALOS™ aligns with our mission to advance manufacturing technologies, significantly improving patient outcomes by producing implants with superior biointegration, reduced stress shielding, and exceptional fatigue resistance. These benefits should lower the rate of surgery revisions, thus avoiding patient discomfort and unnecessary added surgery costs.”
Source: Croom Medical
JAV
Julie A. Vetalice is ORTHOWORLD's Editorial Assistant. She has covered the orthopedic industry for over 20 years, having joined the company in 1999.