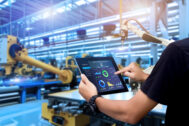
Integrating automation into orthopedic manufacturing processes demands plenty of planning and team-focused initiatives. It’s well worth the effort in today’s workforce environment, as a general shortage of skilled laborers is increasing the importance of automating more segments of device production.
“Companies are struggling to find people with the expertise to operate equipment and manufacture parts,” said Sean Noonan, Application Engineering Manager at GF Machining Solutions. “This has led to an emphasis on standardizing and simplifying processes, which is a natural byproduct of automation.”
Corey Fouquette, Engineering Manager at Metal Craft and Riverside Machine & Engineering, said that adding automation across multiple production areas while still allowing for human interaction within the automated cells maximizes manufacturing uptime and efficiency. He also said incorporating automation’s best practices into a cohesive process demands well thought out execution and monitoring.
“Shortcomings in manual operations can sometimes be masked by skilled operators who inspect and adjust each part as needed,” Noonan added. “But if your process isn’t robust for automation of manufacturing, you can end up with a lot of scrap. Automation pushes you to optimize your machining practices.”
Planning for Flexibility
Fouquette suggests engaging a cross-functional team to collaborate with internal stakeholders and external vendors to determine the goals of an automated manufacturing project.
“This ensures you have the necessary materials, tools and other resources available for production,” Fouquette said. “As you plan and align the goals of a manufacturing process, the role of automation becomes critical in bringing everything together.”
Rely on your enterprise resource planning (ERP) system to provide visibility and alignment of a project’s goals. Metal Craft has customized its ERP system to generate reports that pull open jobs into a clear, visual format for everyone involved. These reports allow the team to quickly identify areas that might be overburdened or running out of capacity. The team can also target parts of the automation process that could be made more efficient.
The software used to automate manufacturing processes is another important factor to consider. Many of the programming and verification tools that Metal Craft uses are highly advanced. For instance, inputting a CNC machining program into the company’s verification software provides real-time feedback regarding optimizations, such as adjusting tool paths or modifying speed around corners. This feedback improves production quality and cycle times.
Noonan pointed out that companies can mix and match the production of various components through the same automated machine without needing to build separate fixtures. This flexibility maintains a continuous production schedule and allows engineers to multitask, maximizing the use of equipment instead of having it sit idle.
“With the rising cost of manufacturing equipment, companies are looking for ways to make the most out of their investment,” Noonan said. “We’ve all felt the impacts of significant price increases, not just in equipment but also in materials, and eventually, those costs trickle down.”
Smooth Execution
Material handling is an important consideration for setting up automated cells in a low- to mid-volume environment, according to Fouquette. “If you’re using a pallet change machine, it’s crucial to have consistent and redundant base workholding systems,” he said. “This allows for a seamless transition between different parts, reducing downtime and improving overall efficiency.”
The way stock sizes are handled is also crucial. “The feeder that supplies material to the automation system must be modular to easily switch between different stock sizes,” Fouquette said. “This flexibility is key to efficient automation.”
Metal Craft uses RFID tags to track the automated manufacturing process and send real-time feedback from the shop floor to the engineering department. The company also uses a file repository to save automation programs and ensure that the latest version is always available, reducing the risk that outdated programs are used during production.
Inspection is a critical but sometimes overlooked part of the automated manufacturing process. “If we don’t collect all the necessary data, our parts aren’t ready for distribution,” Fouquette said. “We’re not just selling the part itself. We’re selling the data that verifies it meets specifications.”
Collecting inspection data directly from the machine during production cycles is essential for maintaining process capability. “Real-time data collection ensures that the automated process runs smoothly,” Fouquette said. “If the process becomes unstable, you risk producing bad parts and needing human intervention, which interrupts automation’s efficiency and productivity.”
Automated vision inspection tools are integral to Metal Craft’s daily operations and help to maintain quality without slowing down production.
Metal Craft also uses in-machine probing, which allows its team to check the critical dimensions of produced parts in real time, adjust offsets directly in the machine and maintain the stability of the production process.
Video monitoring — placing a camera on or inside automated machines — and software that sends alerts via email or texts when something goes wrong allows Metal Craft’s on-call support team to quickly respond to issues and get automated cells back up and running.
Integrating all these processes allows for flexible manufacturing, which involves setting up equipment to collect and exchange data seamlessly. However, Metal Craft can easily modulate the process — moving or parking a piece of automation equipment — and have a person step in to produce parts.
“The ability to switch between automated and manual operation has been key to our success, especially in a low- to mid-volume environment,” Fouquette said.
Noonan said that GF Machining is seeing increased demand for trauma implants designed for use in the wrist and ankle, and noted that orders for knee replacement implants are steadily growing. GF Machining’s customers want more control over their processes and operations, increasing the importance of dialing in automated manufacturing’s specs.
The flexibility that automation offers lends significant advantages in meeting the expectations of GF Machining’s customers. For example, Noonan said palletization systems provide greater repeatability and allow parts to be switched rapidly to enhance productivity and responsiveness.
For these reasons, the company is expanding its automated manufacturing efforts.
“We’re seeing significant growth in this area, especially with more entry-level automation solutions like cobots, which offer easier integrations,” Noonan said. “One of the key challenges we’re addressing is automating the handling of chips — ways to efficiently remove chip bins, swap them out and manage pallets across multiple machines.”
The Bottom Line
Cost, of course, is a key consideration when integrating automation tools into manufacturing processes.
For example, Noonan noted that a company might spend $30,000 on a fixture that could be loaded by a robot. Alternatively, he said, the company could opt for a simpler pallet load system, which costs about $5,000 per fixture. As manufacturing volumes increase, the company might need to buy so many fixtures that investing in automation, even though it’s more expensive on the front end, becomes cost-effective in the long run.
“At the end of the day,” Noonan said, “it’s all about making business decisions that balance cost and efficiency.”
DC
Dan Cook is a Senior Editor at ORTHOWORLD. He develops content focused on important industry trends, top thought leaders and innovative technologies.