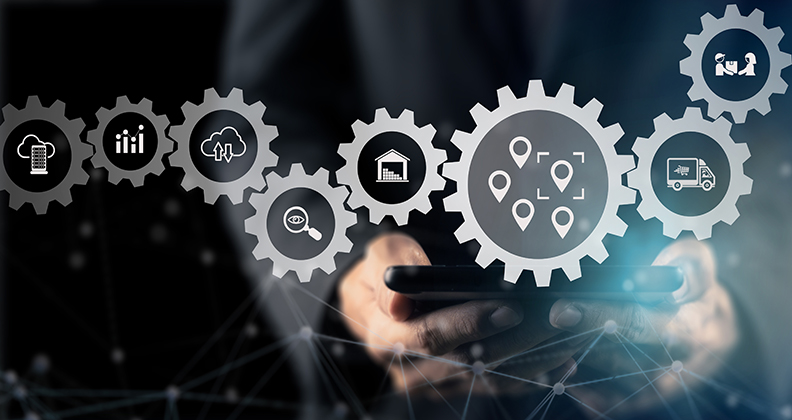
Effective supply chain management is no simple task. Geopolitical unrest, natural disasters and global demand fluctuations constantly threaten access to critical materials, forcing orthopedic manufacturers to adopt a proactive approach to managing material shortages. Supplier diversification and collaboration, contingency plans and the vigilant monitoring of industry trends and international news are prerequisites to bringing products to market.
It’s a lot to manage.
“Success in managing supply chain challenges hinges on accurately mapping your supply base and staying in touch with your suppliers,” said Tom Williams, General Manager at Millstone Medical Outsourcing. “But adjusting to the realities of the market’s supply and demand also requires remaining nimble.”
Supply chain nimbleness is essential in today’s manufacturing environment, according to Williams. He added that the ability to adapt to market forces is critical to maintaining capacities without sacrificing quality when pivoting to alternative materials or vendors.
“Build a robust supplier network with redundancy built in to protect your ability to fulfill contractual commitments while still leaving room for new client service,” Williams said. “We constantly forecast and plan for growth, which enables us to proactively reduce lead times.”
Millstone’s ability to anticipate and navigate material shortages and other global supply chain disruptions helped the company cope with the tumult of the pandemic, a global disaster from which supply chains have only begun to recover.
The company navigated shortages in recent years by expanding to a broader set of packaging materials for its products, which has enabled more customers to adopt their use, according to Williams. The shift has relieved resource constraints for Millstone’s customers during a turbulent period.
“Many of the material shortages and shipping-driven delays that occurred between 2020 and 2022 have mostly been resolved,” Williams said.
Millstone does not currently have trouble obtaining materials for its customers, according to Williams. “In addition, lead times are starting to trend downward, which has enabled us to maintain coverage and avoid stock-outs.”
Material shortages can lead to costly delays in project timelines, said John Webber, CEO of GForce Life Sciences, a consulting firm and staffing agency that specializes in medical device manufacturing. “Delays cause a cascade of issues, flowing down to product release, distribution and, ultimately, delivery to the patient,” he added.
Webber pointed to the shutdown of elective surgeries in the first quarter of 2020 during the COVID-19 pandemic as an example. “This was even before material shortages truly began to impact the manufacturing business,” he said. “Extended lead times for critical materials can, have and will disrupt project schedules, affecting the overall amount of time it takes to deliver medical devices to market.”
Webber said that orthopedic device manufacturers need to place special emphasis on safety and quality assurance during material shortages, as production teams might be forced to use alternative suppliers or even materials that may not meet the same stringent standards.
“Ensuring the safety and efficacy of medical devices becomes more difficult when there are limitations in accessing the necessary materials for manufacturing,” he said. “Do not ever let sales dictate your quality process.”
Ready to React
Identifying potential material shortages before they become supply chain problems demands constant monitoring of the market.
“Stay finely attuned to the industry, suppliers, customers and market forces so you can be proactive in addressing emerging challenges with as much time to solve them as possible,” Williams said.
In addition to standard tools like materials requirement planning (MRP) and scheduling platforms, Millstone utilizes forecasting software technology to monitor global trends.
“This software removes some of the noise from forecasting, so we can better predict incoming demand,” Williams said. “The tool gives us a level-set based on historical demand and relevant factors — and with it, we have greater confidence in material demands and our needs.”
Williams recommends giving supply chain vendors longer planning windows to ensure that critical materials are always available.
“This can be accomplished by issuing blanket purchase orders, which enable vendors to schedule their facilities in a more streamlined way while still supplying essential components as needed,” he said. “The ability to issue blanket purchase orders hinges on an advanced look into your manufacturing needs and demand. It ultimately allows you to build collaborative partnerships to manage inventory levels within your supply chain.”
When material shortages do occur, Williams suggests building resilience into the supply chain operations by mapping out the customer base and taking a constant, birds-eye view of the landscape.
“With the two facets of this approach, we have built redundancy into management processes wherever possible,” he said. “This enabled us to steer customers through the unprecedented supply chain pressures of the last four years while managing lead times, even during unexpected disruptions like shipping delays and material shortages.”
Williams noted that solving material shortages quickly requires a strong relationship with supply chain vendors and demands two-way flexibility that transcends the buyer-seller relationship. “In practice, building relationships is predominantly about maintaining open lines of communication,” he said. “The best contingency plan you can have in place is a relationship that gives you the ability to pick up the phone and work through issues with suppliers proactively and productively.”
The rising costs of scarce materials can lead to budget overruns, putting significant financial strain on device development projects. “Orthopedic companies might need to reassess budgets, potentially cutting costs in other areas, or seek additional funding to cope with the increased expenses associated with material shortages,” Webber said.
Material shortages necessitate frequent communication and collaboration with suppliers to secure available resources, Webber explained.
“This requires efficient coordination among project management teams,” he said. “Clear and transparent communication becomes crucial to managing expectations, both internally and externally, as teams work through the challenges posed by material shortages in the medical device industry. As I like to say, ‘Clear is kind.’”
People Power
Webber said material shortages can have unpredictable and negative impacts on manufacturing operations, which leads to staffing challenges. Maintaining cost-effective staffing models becomes difficult when key materials are scarce, because additional time and effort are needed to identify alternative sources or substitutes.
“It’s not just about the materials — the human element matters,” he said. “Project managers may need to allocate more staffing resources to manage supply chain issues, diverting personnel from other essential tasks and potentially straining project teams.”
Nimbleness helps here, too. Orthopedic manufacturers could downsize staffing levels when faced with drastic manufacturing delays that are caused by material shortages, Webber noted.
“That provides temporary relief to the bottom line, but it will be an issue when companies are ready to ramp production levels back up,” he said. “The answer to this dilemma involves incorporating a flexible workforce strategy. Hiring interim talent during manufacturing downturns allows orthopedic companies to look for full-time employees or consider converting those interim players into permanent roles when production levels return to normal.”
PM
Patrick McGuire is a BONEZONE Contributor.