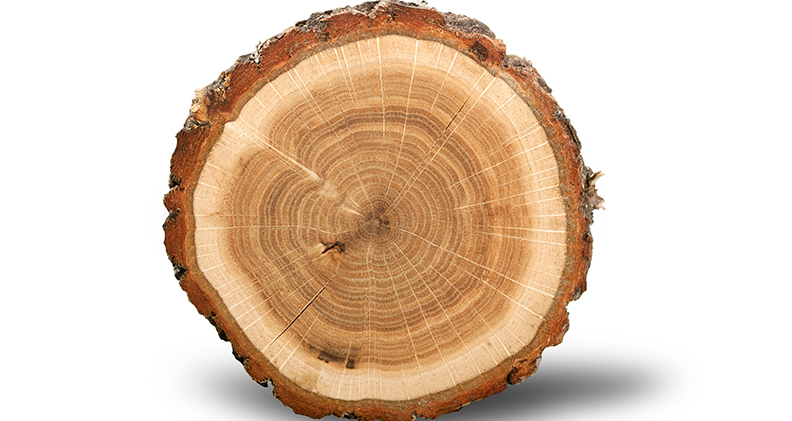
It’s always interesting to count the rings of a felled tree to estimate how long it stood and imagine what it witnessed. Researchers at Washington State University’s School of Mechanical and Materials Engineering see something different in the circular layers of aged wood: structural strength.
The way layered rings of various materials interact in birches to create a natural sturdiness also occurs in bone. These examples led the WSU researchers to integrate standard welding equipment into a CNC machine to 3D-print precision parts made from two metals.
Amit Bandyopadhyay, Ph.D., a professor in the School of Mechanical and Materials Engineering at WSU, said the additive manufacturing method his team developed has the potential for broad application in orthopedics. He pointed to younger patients who are undergoing joint replacement surgery, a trend that requires the development of durable implant materials.
“There is a clinical need for stable implants that offer longer lifespans in vivo and have an inherent antibacterial surface to prevent infection,” he said. “Those implants might not be made of only one material — perhaps they will be bimetallic. Our technology platform offers hope to manufacture such devices.”
Combined Strength
Dr. Bandyopadhyay and his team have been working on the 3D printing of bimetallic and multi-material structures for about 15 years. However, much of their work used powder-based laser-directed energy deposition (L-DED). This is their effort at creating bimetallic structures with wire-fed arc welding (arc-DED).
Most wire arc additive manufacturing or arc-DED systems use one welding system connected to a robot or a CNC machine, Dr. Bandyopadhyay pointed out. “This typically involves metal inert gas (MIG) welding,” he said. “In our home-built system, we have connected two MIG welding systems with one CNC machine.”
That way, Dr. Bandyopadhyay explained, two materials could be deposited along the X, Y and Z directions. “We then used two different steels with slight variations in the coefficient of thermal expansion (CTE) and printed them in a radial bimetallic configuration that resembled a wood structure,” he said. “The thermal mismatch between the two structures created mechanical locking and improved the overall properties of the steels.”
The setup’s two MIG welding heads worked in back-to-back cycles on a circular layer to print two metals with specific properties. Dr. Bandyopadhyay and his team created a corrosion-resistant, stainless-steel core inside an outer casing made of inexpensive “mild” steel.
The two metals shrank at different rates as they cooled, so the researchers created an internal pressure within the printing chamber to join the metals together. Subsequent testing showed the metals were stronger together than they would have been on their own.
Additive manufacturing that involves multiple metals currently requires pausing to change the metal wires, the researchers noted. They said their method placed multiple metals on the same printing layer while they were still hot, eliminating the need to pause the printing process.
The circular motion of the printing process was also key.
“Our method deposits the metals in a circle instead of a line. Doing that fundamentally departs from what’s been possible in 3D printing,” said Lile Squires, a WSU mechanical engineering doctoral student. “The circular motion essentially allows one material to bear hug the other material, which can’t happen when printing in a straight line or in sandwiched layers.”
The researchers found a 33% relative increase in compression strength for radial bimetallic specimens over monolithic mild steel and a 42% relative increase in strength over monolithic stainless steel. Thermal stress analysis of the CTE mismatch between the two materials during the final cool down period suggested a residual stress effect that resists crack propagation, according to Dr. Bandyopadhyay.
His team published their findings in the journal Nature Communications and submitted a provisional patent application for their bimetal 3D printing process.
Reimagining What’s Possible
Bimetal 3D printing presents the promise of broad applications because welding can be expanded to include design concepts that combine hard and soft materials almost simultaneously, according to Dr. Bandyopadhyay.
He believes the bimetal 3D printing process could be used to produce joint replacement implants made of a magnetic steel core with healing properties surrounded by a durable titanium surface.
“Our concept employs two welders for printing, so we can use multiple materials in the same layer to create property advantages as they combine,” Dr. Bandyopadhyay said. “The method isn’t limited to two materials. It can be expanded to include multiple metals.”
Dr. Bandyopadhyay noted that metal additive manufacturing has made a difference in load-bearing orthopedic devices only in the last five to eight years, and they’re typically made with a single metal. “There is a need for bimetallic technologies to manufacture devices with resorbable metal at the outer surface for osseointegration and a solid, non-resorbable material at the core. Technologies like this will help engineers dream of different devices that do not exist today.”
DC
Dan Cook is a Senior Editor at ORTHOWORLD. He develops content focused on important industry trends, top thought leaders and innovative technologies.