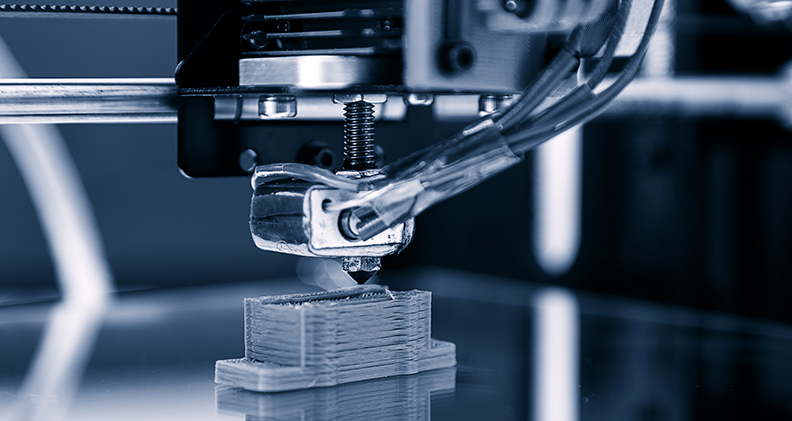
Additive manufacturing (AM) allows orthopedic engineers to create complex shapes, textures and assembled parts that traditional manufacturing methods cannot make.
The obvious benefits of AM come with clear challenges, however, including the lack of consistent product design documentation and difficulties in maintaining clear lines of communication between engineers and manufacturing teams. AM also generates reams of data that must be properly protected and explored to take full advantage of this emerging technology.
Multiple standards committees, regulatory bodies and organizations have released updated AM guidance to help orthopedic device manufacturers produce high-performance implants and instruments.
Streamlined Communication and Production
Subtractive manufacturing involves 2D design sketches, which have been a sufficient way for engineers to communicate design needs to manufacturers. However, AM requires 3D modeling to accurately represent the specific features of desired products or components.
AM can be difficult for device manufacturers to add without clear instructions on how to document and communicate 3D models. This factor has stalled widespread adoption.
The American Society of Mechanical Engineers (ASME) has been developing AM guidance since 2017, when the organization released the first draft of its Y14 standards. The standards include definitions of terms and features unique to AM technologies, as well as recommendations for their uniform specification in product data and related documents.
Fredric Constantino, ASME Project Engineering Advisor, stated that many standards require 3D models and digital data to define or design a product. “The model-based design aspect, which really shines with additive manufacturing, has led to numerous updates of the standards,” he said.
ASME has used research and advice from the National Institute of Standards and Technology (NIST), America Makes and industry groups to develop their work. The result is the updated Y14.46 Product Definition for Additive Manufacturing standard, released in June 2022.
Bone replacements with internal lattice structures are lighter and easier to fit with the body’s natural anatomy. “Subtractive manufacturers haven’t considered making these types of structures,” Constantino said. “So, we focused on how to convey those design elements to customers, clients and vendors, and inspection agencies such as NIST so they understand how to monitor AM processes.”
AM standards are reviewed approximately every five years. Constantino said Y14.46 standards will be constantly monitored, allowing engineers to update various sections as AM technology evolves and its use becomes more widespread.
Working with quality standards accredited by the American National Standards Institute and vetted through the organization’s consensus standard may increase the adoption of AM, according to Constantino, who said companies that use the standards are more likely to adopt the technology to improve their manufacturing process.
Data Usage and Management
AM is a digital manufacturing process that produces enormous amounts of data, which is invaluable when it comes to process improvements. The digitization of the manufacturing process provides the ability to monitor and react during a production run.
Paul Witherell, Associate Program Manager in the Engineering Laboratory at NIST, said data streams have enhanced additive manufacturing. “Collecting data during and after production, and using it to adjust the process, provides significant benefit,” he added.
Real-time access to manufacturing data provides instant feedback and supports long-term process improvements and knowledge.
“Data for each part of the process is being collected at the terabyte level by some companies,” Witherell said. “There’s been an enormous amount of information collected and added to the knowledge base.
“As AM processes mature, we’ll better understand the context in which certain data was created and certain measurements were made. That information will be key in instituting feedback control and improving designs through better predictive modeling and simulations.”
Shawn Moylan, Engineer and Project Lead at NIST, stated that much focus has been placed on data management in AM. “Recent work has concentrated on translating raw data into accessible and usable formats for the industry,” he said.
In September 2022, the ASTM Committee F42 on Additive Manufacturing Technologies published guidance on using and protecting data effectively. ASTM E3353-22 addresses the ways in which manufacturers can use data created from digital-physical communication (such as between computers and actuators) to monitor and adjust AM processes in real time.
Several standards are being created to guide the acquisition and storage of data related to AM processes, metadata requirements and the visualization and representation of products.
An updated version of ASME Y14.41, which establishes requirements and reference documents applicable to the preparation and revision of digital data sets, should be released by 2024.
ASME Y14.47 promotes organizing AM data to ensure successful transfer between manufacturers and inspectors. An update to this standard is expected in 1Q23.
“The rise of machine learning and artificial intelligence has led to the gathering of more data. The more data you get, the better algorithms you can develop,” Witherell said. “And the better algorithms you develop, the more useful your data gets. It’s an iterative loop.”
Benefitting From Best Practices
Data usage and sharing related to AM has been a controversial topic in orthopedic circles. The use of digital tools and data collection can benefit the industry as a whole, however.
“As we learn from the data, we can make better observations about specific manufacturing processes,” Witherell said. “Manufacturers can add AM more easily, without needing the same amount of knowledge base as before.
“When small- and medium-sized manufacturers integrate AM machines, monitoring equipment and data collection capabilities, they can adjust their processes without building their own proprietary knowledge base.”
Orthopedic manufacturers must share their knowledge to help develop best practices, standards and guidance for data usage and AM process improvements. The more device engineers and industry professionals engage in the creation of standardized recommendations, the better.
HT
Heather Tunstall is a BONEZONE Contributor.