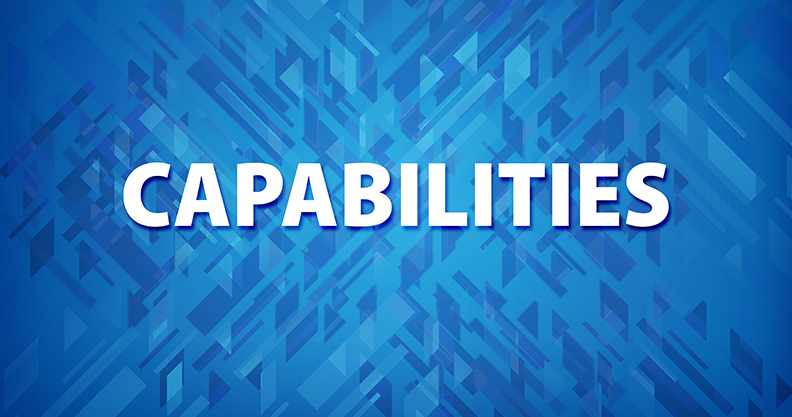
Metal injection molding (MIM) has the potential to reduce manufacturing costs, increase production volume and create highly complex and durable parts. Though the technology has been around for decades, it has only recently made waves in the orthopaedic industry.
Dave Smith, Program Manager at Advanced Forming Technology, outlines several reasons for this recent attention.
“The medical device industry has now adopted MIM as a standard technology in their repertoire rather than a technology in development,” Smith says. “Medical devices are by nature, small, complex geometries with high mechanical and dimensional tolerances. These requirements fit MIM well, and with constant pressures to reduce cost in their components, MIM is a great technology for manufacturers to take advantage of. This is why we think the medical device industry is talking about MIM more and more.”
MIM can offer design flexibility and reduce manufacturing costs by molding from a single tool, eliminating multiple set-up operations and combining components to reduce part count.
Smith defined the four-step MIM process.
“To implement MIM, all that is required from the customer is a viable product design (CAD model and detailed print),” Smith says. “With this information and proper design for manufacturing workshops, a MIM supplier will have enough information to develop an injection mold and sustainable method of manufacture.”
MIM’s adoption by the orthopaedic industry can also be attributed to ASTM’s recent establishment of two standards for cobalt chromium and titanium—common metals used in MIM for orthopaedic devices. Several orthopaedic groups sat on committees responsible for the creation of those standards, according to Joe Grohowski, President at Praxis Powder Technology.
“That’s a big step towards allowing MIM products, or helping MIM products be used in the orthopaedic industry,” Grohowski says. “When there’s not an ASTM standard, people feel adrift. It helps put a stake in the ground. Theadvent of standards, as well as practice of getting to the point where this can be done repeatedly, starts to move the technology to a position where it could be used in the orthopaedic market.”
Though MIM has cost reduction potential, high-volume production rates and the ability to create strong, intricate parts, it’s not suited for all orthopaedic devices. Consider size when determining whether your device can include parts made through MIM. The technology is optimal for smaller parts, such as screws, femoral components and tibial bases. Additional elements to consider are your product’s surface, features and geometries.
“Parts that would be made by combining multiple components can be produced as a single MIM part,” Smith says. “It reduces requirements for finish machining by producing geometries that do not require secondary operations.” Assess your device’s characteristics to determine if MIM is the most efficient and cost effective solution for you.
Send comments on this article to Carolyn LaWell.
Photo Credit: Advanced Forming Technology