-
Norwood Medical
2122 Winners Circle
Dayton, Ohio
45404
United States - 700,000 sq ft.
- 937-228-4101
- 1250+ employees
- Founded in 1920
- Operating in North America
- Visit Website
Vice President Sales & Marketing
Changes saved
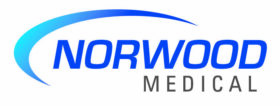
- Equipment/Machinery
- Instruments
- Manufacturing
- Packaging
- Surface Preparation/Treatments
Norwood Medical has more than 40 years of experience in contract medical manufacturing, with advanced capabilities to produce the most complex medical devices and implants. Supporting customers in orthopaedic and minimally invasive surgery markets, Norwood Medical quickly gained a reputation for tackling complex parts and projects that other contract medical manufacturers were unable to produce. Throughout our history, our willingness to embrace complexity has produced a culture of innovation.
Our manufacturing campus with 700k sq ft in Dayton, Ohio provides expertise, scale and speed to our customers.
- Stamping, Mill, Heat Treat & Assembly (80k ft2)
- Engineering, Tool Shop & Prototyping (62k ft2)
- Swiss Manufacturing – Components & Implants (62k ft2)
- Instrumentation & Mid-Level Volume Programs (71k ft2)
- Swiss, Mill, Laser Weld & Marking (47k ft2)
- Receiving Inspection, Inventory & Material Prep (20k ft2)
- Mill, Turn & Assembly (54k ft2)
- MIM, Plastic Injection Molding, Mill & Assembly (76k ft2)
- Swiss & Mill (107k ft2)
- Mill, Assembly (33k ft2)
- In construction (72k ft2)
Manufacturing Campus
Our manufacturing campus with 700k sq ft in Dayton, Ohio provides expertise, scale and speed to our customers.
- Stamping, Mill, Heat Treat & Assembly (80k ft2)
- Engineering, Tool Shop & Prototyping (62k ft2)
- Swiss Manufacturing – Components & Implants (62k ft2)
- Instrumentation & Mid-Level Volume Programs (71k ft2)
- Swiss, Mill, Laser Weld & Marking (47k ft2)
- Receiving Inspection, Inventory & Material Prep (20k ft2)
- Mill, Turn & Assembly (54k ft2)
- MIM, Plastic Injection Molding, Mill & Assembly (76k ft2)
- Swiss & Mill (107k ft2)
- Mill, Assembly (33k ft2)
- In construction (72k ft2)
Validated processes lead to quality
Norwood assures customer satisfaction and product safety through a robust and proven Quality System that is 21 CFR 820 FDA Quality System (QS) Regulation compliant and ISO 13485:2016 certified. The quality of each one of our products will have a direct impact on a patient’s well-being, and because of this, we address quality with unwavering diligence.
Our comprehensive approach to quality process excellence includes:
- Validation of all special processes to ensure objective evidence that our product consistently meets the specified requirements utilizing IQ, OQ and PQ procedures
- Deploying certified Black Belt engineers using lean manufacturing/Six Sigma tools to eliminate waste and remove variation from our manufacturing processes
- Utilizing ISO 14971:2012 risk management system for medical devices to aid in risk management.
Quality metrology inspection laboratories
Each of our production facilities contains a dedicated Quality metrology inspection laboratory. Certified inspectors perform detailed inspections, including first piece, last piece and in-process dimensional verifications to ensure product integrity. The laboratories are equipped with the latest metrology tools, including CMMs, Optical Gaging Systems, Comparators and Hardness Testers and a host of mechanical inspection gauges.
Quality inspection stations
Dedicated manual inspection stations are in place at each of our production facilities. Employees inspect each part with microscopes and other inspection tools, and are trained to recognize and remove the slightest imperfection or debris. Other stations requiring more sophisticated inspection rely on a combination of computer-based mechanical evaluation and manual measurements to precisely inspect the geometry of each part to ensure its integrity.
Accreditations
Norwood Medical holds the following certifications and accreditations:
- ISO 13485:2016
- ASQ Certified Staff
- GMP 21CFR820
Dedication to Quality
Validated processes lead to quality
Norwood assures customer satisfaction and product safety through a robust and proven Quality System that is 21 CFR 820 FDA Quality System (QS) Regulation compliant and ISO 13485:2016 certified. The quality of each one of our products will have a direct impact on a patient’s well-being, and because of this, we address quality with unwavering diligence.
Our comprehensive approach to quality process excellence includes:
- Validation of all special processes to ensure objective evidence that our product consistently meets the specified requirements utilizing IQ, OQ and PQ procedures
- Deploying certified Black Belt engineers using lean manufacturing/Six Sigma tools to eliminate waste and remove variation from our manufacturing processes
- Utilizing ISO 14971:2012 risk management system for medical devices to aid in risk management.
Quality metrology inspection laboratories
Each of our production facilities contains a dedicated Quality metrology inspection laboratory. Certified inspectors perform detailed inspections, including first piece, last piece and in-process dimensional verifications to ensure product integrity. The laboratories are equipped with the latest metrology tools, including CMMs, Optical Gaging Systems, Comparators and Hardness Testers and a host of mechanical inspection gauges.
Quality inspection stations
Dedicated manual inspection stations are in place at each of our production facilities. Employees inspect each part with microscopes and other inspection tools, and are trained to recognize and remove the slightest imperfection or debris. Other stations requiring more sophisticated inspection rely on a combination of computer-based mechanical evaluation and manual measurements to precisely inspect the geometry of each part to ensure its integrity.
Accreditations
Norwood Medical holds the following certifications and accreditations:
- ISO 13485:2016
- ASQ Certified Staff
- GMP 21CFR820
We offer E2E manufacturing and engineering solutions along the entire value chain to our customers.
DFM, Engineering & Process Development:
Program Management: Dedicated program managers support customers on their program needs
Engineering: Experienced team to address design challenges and co-develop new processes
Prototyping & Tooling Development:
R&D – Prototyping: Dedicated R&D center enables quick prototypes & product design development
Tooling Development: In-house design & build
capacity with focus on tooling, programming & inspection
Precision Machining & Processing:
Best-in-class Manufacturing: >750 CNC machines & automation improve process stability, scrap rates & efficiency
Manufacturing Campus: 700k sq ft manufacturing site with 11 buildings ensure ability to scale, proximity & speed
Value-add Secondary Processing:
E2E Manufacturing: Full-service provider with >30 vertically integrated capabilities
Lean Supply Chain: One-stop shop with lean operations to fulfill customers’ product & process needs
Testing, Assembly & Packaging:
Quality Excellence: Embedded quality mindset & processes assure excellence at every step of manufacturing
In-house Assembly: Dedicated facilities & resources to provide final assembly & packaging incl. cleanroom
E2E manufacturing
We offer E2E manufacturing and engineering solutions along the entire value chain to our customers.
DFM, Engineering & Process Development:
Program Management: Dedicated program managers support customers on their program needs
Engineering: Experienced team to address design challenges and co-develop new processes
Prototyping & Tooling Development:
R&D – Prototyping: Dedicated R&D center enables quick prototypes & product design development
Tooling Development: In-house design & build
capacity with focus on tooling, programming & inspection
Precision Machining & Processing:
Best-in-class Manufacturing: >750 CNC machines & automation improve process stability, scrap rates & efficiency
Manufacturing Campus: 700k sq ft manufacturing site with 11 buildings ensure ability to scale, proximity & speed
Value-add Secondary Processing:
E2E Manufacturing: Full-service provider with >30 vertically integrated capabilities
Lean Supply Chain: One-stop shop with lean operations to fulfill customers’ product & process needs
Testing, Assembly & Packaging:
Quality Excellence: Embedded quality mindset & processes assure excellence at every step of manufacturing
In-house Assembly: Dedicated facilities & resources to provide final assembly & packaging incl. cleanroom
We Continuously Invest in Automation to Increase Efficiency and Cost Savings
Robotics:
- We use robots for many applications including assembly, machine loading and deburr
- $1.5m invested in robots in last 3 years
- Reduced direct labor costs by up to 50% resulting in savings for our customers
Vision Systems:
- >80 vision systems used for error proofing and part inspection
- >40 CMM systems available for inspection
- Increased repeatability by >10% due to automated visual inspections
Lasers:
- $2m invested in lasers in last 3 years
- Specialized in precision welding with a materials lab capable of weld qualification
- >120 lasers in operation for validating and verifying welds throughout process
Automation Overview
- 40+ dedicated team members in automation designing & building automated custom solutions
- 3% of revenue spent on automation p.a. showing Norwood’s commitment to process improvement
- 160+ active automation machines incl. robotics, vision systems, laser marking, cutting & welding
- 130+ automated production processes
Automation
We Continuously Invest in Automation to Increase Efficiency and Cost Savings
Robotics:
- We use robots for many applications including assembly, machine loading and deburr
- $1.5m invested in robots in last 3 years
- Reduced direct labor costs by up to 50% resulting in savings for our customers
Vision Systems:
- >80 vision systems used for error proofing and part inspection
- >40 CMM systems available for inspection
- Increased repeatability by >10% due to automated visual inspections
Lasers:
- $2m invested in lasers in last 3 years
- Specialized in precision welding with a materials lab capable of weld qualification
- >120 lasers in operation for validating and verifying welds throughout process
Automation Overview
- 40+ dedicated team members in automation designing & building automated custom solutions
- 3% of revenue spent on automation p.a. showing Norwood’s commitment to process improvement
- 160+ active automation machines incl. robotics, vision systems, laser marking, cutting & welding
- 130+ automated production processes
We Offer customers a range of MIM and molding capabilities:
Our MIM journey started in 2010 and since then we steadily advanced our MIM capabilities demonstrating our commitment to enable our customers as full-service manufacturing partner.
Michael Stucky, President of the Metal Injection Molding Association (MIMA), leads our MIM department.
Our MIM equipment in 2024 includes:
- 5 Arburg molding machines
- 2 high-capacity pusher furnaces with H2 generation
- In-house feedstock mixing
We continue to grow our MIM capabilities:
- by expanding to MIM complete parts
- by increasing prototyping and rapid tooling options
- by investing in 3D printing for rapid steel cavities
MIM and Molding Capabilities
We Offer customers a range of MIM and molding capabilities:
Our MIM journey started in 2010 and since then we steadily advanced our MIM capabilities demonstrating our commitment to enable our customers as full-service manufacturing partner.
Michael Stucky, President of the Metal Injection Molding Association (MIMA), leads our MIM department.
Our MIM equipment in 2024 includes:
- 5 Arburg molding machines
- 2 high-capacity pusher furnaces with H2 generation
- In-house feedstock mixing
We continue to grow our MIM capabilities:
- by expanding to MIM complete parts
- by increasing prototyping and rapid tooling options
- by investing in 3D printing for rapid steel cavities
With our value-add secondary processing we provide customers a full-service offering.
Laser Marking & Welding – We have 120 lasers for marking and welding in use for >100 different products manufactured.
Polishing & Blasting – We offer customers 3 polishing approaches in-house: bead blast, belt and hand polishing.
Electropolishing – We offer specialized electropolishing for selected products and expand capabilities as needed.
Heat Treating – We have 13 heat treatment ovens (vacuum and temper) and treat >15m parts per year.
Coating – We offer 3 coating technologies in-house:
- PTFE dry film
- sodium stearate
- siliconization
Ultrasonic Cleaning – We have >50 ultrasonic wash lines installed and clean >5,000 parts per hour.
Overmolding – We have 15 years of expertise in overmolding and produce >400k overmolded parts per year.
Passivation – We have cleanrooms (class 7 & 8) in-house and passivate >8m parts per year.
Value-add Secondary Processing
With our value-add secondary processing we provide customers a full-service offering.
Laser Marking & Welding – We have 120 lasers for marking and welding in use for >100 different products manufactured.
Polishing & Blasting – We offer customers 3 polishing approaches in-house: bead blast, belt and hand polishing.
Electropolishing – We offer specialized electropolishing for selected products and expand capabilities as needed.
Heat Treating – We have 13 heat treatment ovens (vacuum and temper) and treat >15m parts per year.
Coating – We offer 3 coating technologies in-house:
- PTFE dry film
- sodium stearate
- siliconization
Ultrasonic Cleaning – We have >50 ultrasonic wash lines installed and clean >5,000 parts per hour.
Overmolding – We have 15 years of expertise in overmolding and produce >400k overmolded parts per year.
Passivation – We have cleanrooms (class 7 & 8) in-house and passivate >8m parts per year.
Norwood Medical is a Leading Supplier in the Orthopedic Market.
- We are a trusted supplier for the leading Ortho players in the industry
- ~750k & assemblies manufactured in 2022
- ~550 unique SKU’s manufactured and shipped to customers in 2022
- Our customers rely on our expertise and lean supply chain to help develop complex implant and fixation solutions for their patients
- Our products are used for procedures in arthroscopic, spinal, trauma surgery, joint reconstruction and sports medicine
- Our exemplary product catergories include ankle clamps, needles, impaction handle, Screws & Plates, and Stems
Leading Supplier in Orthopedics
Norwood Medical is a Leading Supplier in the Orthopedic Market.
- We are a trusted supplier for the leading Ortho players in the industry
- ~750k & assemblies manufactured in 2022
- ~550 unique SKU’s manufactured and shipped to customers in 2022
- Our customers rely on our expertise and lean supply chain to help develop complex implant and fixation solutions for their patients
- Our products are used for procedures in arthroscopic, spinal, trauma surgery, joint reconstruction and sports medicine
- Our exemplary product catergories include ankle clamps, needles, impaction handle, Screws & Plates, and Stems
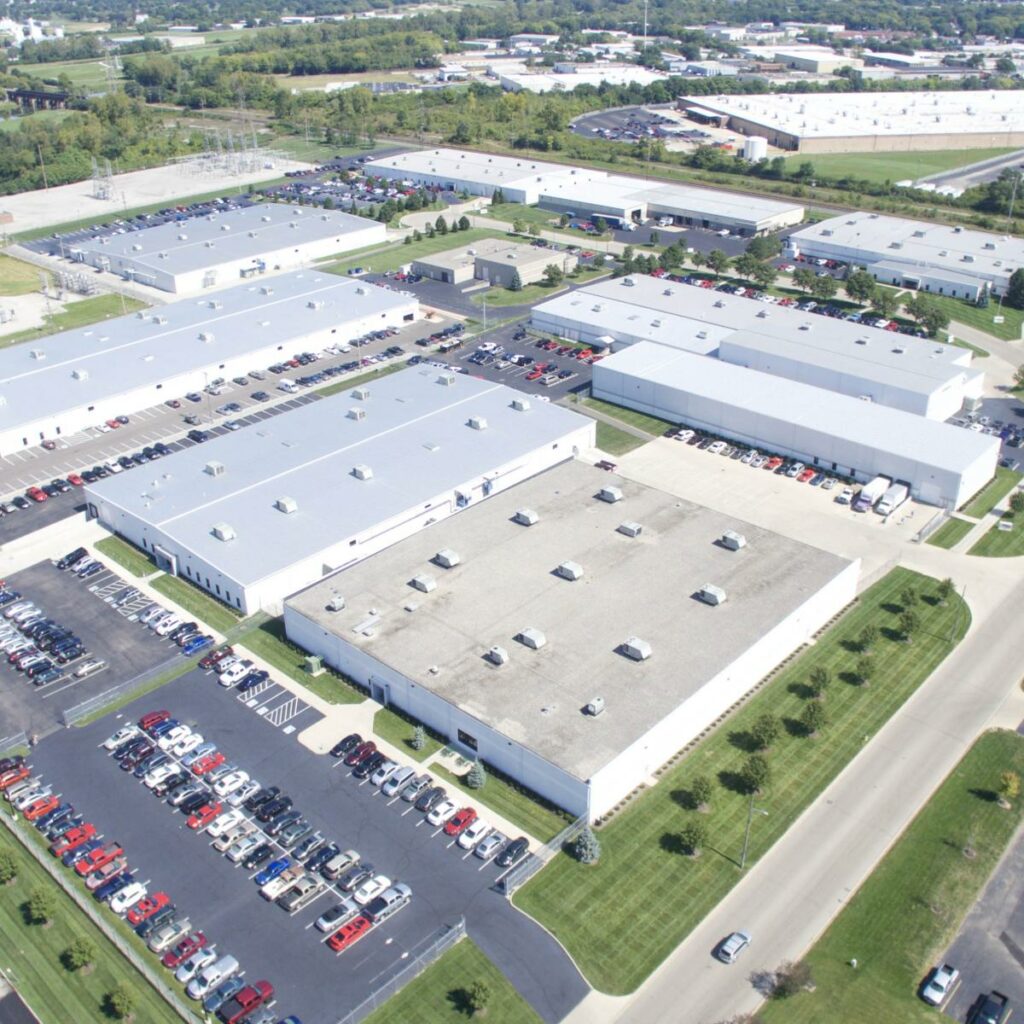
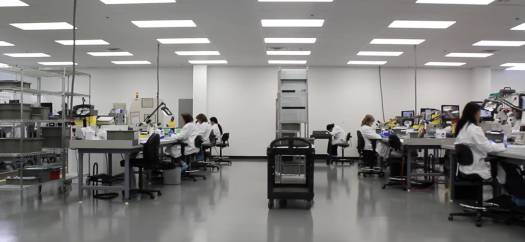
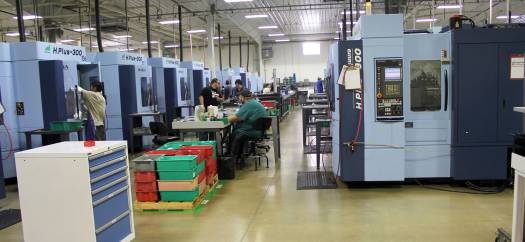
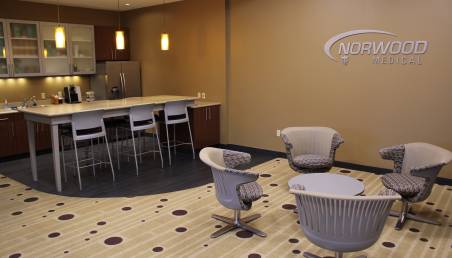

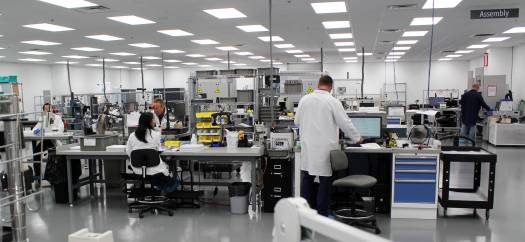