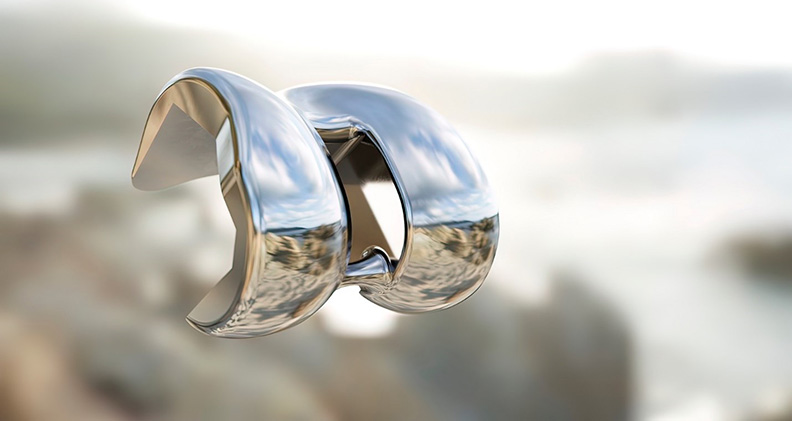
The intercondylar area, specifically the box and cam areas located between the condyle/bearing surfaces of the femoral knee implant, is a manufacturing challenge. The tolerances and roughness required for a perfect knee joint are tight.
The CoCr casting knee implant material has a hardness of 50HRC+ and high-strength properties and ranks among the most difficult to machine. It is also a medical-grade type, incorporating alloys that enhance wear and corrosion resistance. Additionally, it has poor thermal conductivity.
Traditionally, 5-axis milling operations, combined with post-processing methods, are used to machine the box and cam.
Shadows, defects and surface mismatches, which are common, can compromise the product’s quality and reduce the lifetime of the knee implant. Eliminating these defects requires tedious post-processing operations and costly rework, and sometimes, a high scrap rate is the result.
Secondary burrs, even micro-ones, are a by-product of milling, which requires relying on post-processing operation. And because most areas are hard to reach, manual post-processing is often part of the post-milling process, which also has shortcomings, such as quality inconsistency.
Of course, improving the milling strategy, the machine and the tool quality can enhance the overall quality of knee implants, but manufacturing the intercondylar area remains a multi-step process, taking between 12 and 20 minutes to complete and costing about $11 a part.
A Game-changing Solution
Electrochemical Machining (ECM) is a cold 25°C to 30°C (77°F to 86°F), stress-free process that removes material up to 0.55 mm (0.022 in) in thickness. The knee implant box and cam tolerances achieved with ECM are within 0.1 mm (0.004 in). The parallelism is within 0.05 mm (0.002 in), and the roughness is below RA 0.2 µm (8 Ra µin).
With ECM, you can target specific box and cam areas and perform roughing and finishing in one pass. The workpiece is heat-affected zone-free, with no mechanical or thermal stress load.
Achieving 50HRC or more isn’t a problem for ECM, which works independently of the material’s hardness.
The transition between the different surfaces, whether planned, curved or as complex as they may be, is always flawless. Because the ECM principle dissolves the material, it creates smooth transitions between ECM-processed surfaces or between machined and ECM-processed surfaces. As the ECM process dissolves the material, there will be no secondary burrs. Therefore, you do not need intercondylar area post-processing, and especially no manual operation, so you won’t face labor issues such as finding or hiring skilled workers at a high cost.
With robust, automatic process control, ECM eliminates inconsistency and leaves nothing to chance.
ECM efficiency remains high compared to CNC milling for difficult-to-machine materials, such as CoCr. ECM dissolves that material as if it were stainless steel.
When you compare ECM machining efficiency with CNC milling for different materials, you notice that ECM’s efficiency remains firm while CNC’s efficiency decreases with increasing material hardness.
Head-to-head efficiency comparison between CNC machining and ECM for different materials.
Tool life, also known as cathode life, is another benefit provided by ECM.
The tool lifetime is short because the CoCr knee implant material is difficult to mill. On the other hand, the material hardness does not impact ECM. The lifetime of ECM cathodes is independent of the material and, consequently, contributes to reducing running costs.
The ECM outcome is a fast, efficient machining operation.
ECM requires only 90 seconds per knee, with four processed simultaneously in a multiple-fold fixture. In contrast, CNC milling takes an average of 17 minutes per piece, including machining and finishing time, for the same box and cam area.
ECM offers a significant boost in productivity.
The difference in machining operation costs is substantial: $1.60 for ECM versus $11 for CNC.
Meeting Specification and Ensuring Functionality
Thanks to the cathode design, ECM permits targeted material removal at precisely defined locations.
Let’s examine this feature in more detail.
ECM is a mirroring process governed by Faraday’s law of electrolysis; therefore, we must design a cathode that produces the expected geometry. The cathode will envelop the area to be processed, leaving a gap between the cathode and the workpiece, which, in this case, is our knee implant. That gap will permit the electrolyte, typically NaCl solution for the CoCr material, to flow in between.
The electrolyte facilitates the charge transfer from a pulsed direct current between the tool (cathode, -) and the workpiece (anode, +). The electrolyte pressurized flow also removes the metal hydroxide generated during the machining—the electrolyte benefits from a continuous filtration process that separates the hydroxide from the electrolyte to continuously replenish the machine with a clean electrolyte. The mass of metal dissolved is proportional to the electrical charges transferred to the cathode.
The ECM control features real-time monitoring of current and electrolyte chemistry, ensuring traceability.
ECM productivity comes primarily from the machine’s power. There is a direct relationship between the cumulative surfaces that you can process and the available power.
The fixture also plays a crucial role in ensuring maximum productivity, as it enables the handling of multiple workpieces simultaneously. A four-fold fixture is a standard for the knee implant intercondylar area.
With years of experience in the high-volume industry, ECM technology is well-suited for integrating automatic loading and unloading.
At Extrude Hone, we aim to enhance the capabilities of our technologies. Offering the market new solutions to help with quality and productivity improvement.
This ECM knee implant, box and cam machining solution ticks all the boxes to support knee implant manufacturers.
To learn more about this solution, visit extrudehone.com or email the company.
Authored by Bruno Boutantin, Marketing & Business Development Director at Extrude Hone Group.