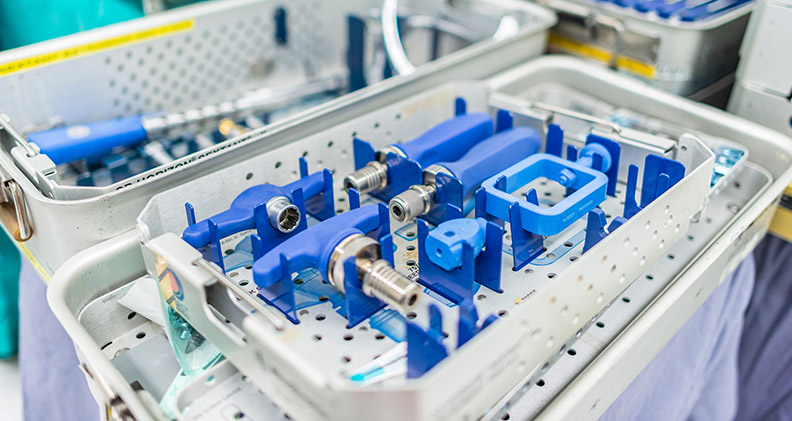
Wendy Mach is quick to point out that packaging is paramount to the safety and effectiveness of orthopedic devices.
“It’s important to understand that the design of packaging solutions is as crucial as the design of the devices they hold,” said Mach, Senior Director of Technical Services at Canyon Labs. “You can’t have one without the other.”
Packaging solutions maintain the sterile barrier and ensure the safe delivery of devices to the operating room. They’re also a marketing tool, providing information about the product and instructions for use that are referenced by end users.
Still, many orthopedic companies fail to prioritize the design of packaging for the devices they’re developing. It’s an unfortunate and all-too-common oversight that often leads to packaging failures during the testing phase. Packaging defects can delay the market launch of new products by six months to several years, according to Mach.
To avoid costly and avoidable mistakes when designing packaging solutions for orthopedic devices, Mach suggests beginning the process with the end in mind.
Starting Points
Effective packaging design involves establishing the physical performance requirements of the solution as a foundational element. “Consider the voice of the customer,” Mach said. “What improvements do they suggest over current market offerings? Is your competitor’s packaging hard to open? Can you make your device easier to access?”
Thermoformed trays are effective options, but you must consider the device’s weight and the durability of the plastic to withstand drops. Also, ensure that shipping containers are sturdy enough to carry the weight of the devices they contain. This is especially important for orthopedic trays that often house numerous heavy instruments.
Mach said protecting orthopedic devices isn’t as simple as using an off-the-shelf pouch or tray. “You often need to incorporate the device’s geometry into the packaging design to ensure safe and accurate transport and easy access,” she explained. “Sharp edges and coatings on devices also need to be considered when designing the interaction between packaging and product.”
When deciding how to protect a device and maintain its sterile barrier through delivery, make sure the protective pouch or tray can’t be punctured, won’t show signs of wear and supports multiple usage cycles. “Many instruments used for device implantation are reusable, so it’s essential that they don’t degrade through the delivery process,” Mach said.
Sustainability is another increasingly important focus for companies. “There’s a significant push in the industry to reduce the amount of packaging that healthcare facilities must manage,” Mach said. “Recent developments on this front have been exciting.”
The use of recyclable materials and bulk packaging, which combines multiple components into a single set, are ways to reduce the environmental impact of shipped devices, according to Mach. She said various organizations, like Kilmer Innovations in Packaging (KiiP), are actively working on sustainability and recycling programs.
Sterility Concerns
Sterilization is a key design input for packaging solutions. “Companies often don’t consider that the compatibility of sterilization methods with packaging materials can impact their performance,” Mach said. “It’s critical to consider this factor early on during the packaging design process to avoid failures.”
Mach noted that common medical device packaging sterilization methods include ethylene oxide (EO), radiation and steam, while chlorine dioxide and nitric oxide are emerging options.
She suggests referring to AAMI TIR17: Compatibility of Materials Subject to Sterilization, which is currently being updated, to learn more about the ways each sterilization method impacts device packaging. The current standard uses a dot system to rank compatibility: Four dots indicate high compatibility; one dot suggests the material is not compatible with a particular sterilization method.
The updated version of AAMI TIR17 will provide detailed considerations for various sterilization modalities and packaging materials, according to Mach. She provided practical considerations to keep in mind for each method:
EO. Device packaging should be permeable enough to allow gas inside and residuals to escape during the sterilization process. The configuration of the packaging is also crucial. For example, layering breathable pouch surfaces can create a non-porous environment. Packaging systems that are subjected to EO sterilization must also withstand pressure and vacuum changes, as well as temperature fluctuations, particularly compared to steam sterilization.
Mach pointed out that low-temperature (63°C) EO sterilization is typically used for temperature-sensitive devices.
“It’s crucial to understand how EO is absorbed by different materials,” she said. “Polymers absorb EO significantly more than metals, so knowing the residual EO levels after exposure is vital.”
Radiation. Gamma, E-beam and x-ray sterilization are gaining in popularity as concerns about EO’s environmental impact grow. Mach noted that radiation sterilization can alter the properties of packaging materials.
Gamma radiation makes polymers brittle if they’re overexposed, so packaging suppliers often add stabilizers to materials to prevent brittleness. When E-beam and gamma sterilization are used, suppliers must consider the mass and layout of the products because these methods rely on the penetration of electrons or radiation rays. “It’s therefore crucial to avoid overly thick packaging and to distribute the mass evenly,” Mach said.
Packaging labels also require attention with these sterilization methods. “Metals in labels can become inductive under radiation, potentially making the packaging radioactive,” Mach said. “It’s important to ensure the inks used to print labels won’t cause such issues.”
Steam. Moist heat or steam sterilization leaves no residues, is a quick process and can usually be performed in-house, according to Mach. “However,” she said, “it requires porous packaging materials that are compatible with high temperatures and moisture.”
Flexible packaging for steam sterilization must withstand pressure changes and maintain stable seals. Mach noted that water is used during steam sterilization, so the device must be validated to ensure it dries sufficiently post-process, and the packaging must facilitate this drying.
Mach highlighted an interesting development in steam sterilization involving the increased use of reusable cassettes, which often include silicone mats that hold devices in place. “When designing packaging with these mats, ensure they are vented on the bottom so steam can enter from underneath and access the device from all angles,” Mach said. “A solid bottom surface creates contact points that steam cannot reach, potentially leaving microbes behind.”
Biocompatibility is a major topic in medical device packaging. “Current standards require that packaging solutions pass a cytotoxicity test,” Mach said. “When evaluating the biocompatibility of a device, it’s important to consider the interaction between the packaging and the device. Any substances that might leach from the packaging during sterilization or use must be tested.”
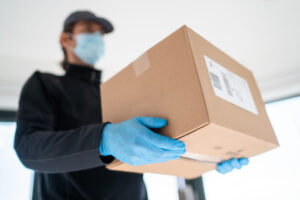
Packaging solutions must be made to withstand the rigors of shipment and delivery.
Distribution Details
The method used to ship orthopedic devices — boat, air, rail or truck — affects the packaging design. For instance, shipping by boat exposes packages to saltwater air and significant shock and vibrations. “Understanding these environmental factors early on is essential for a successful packaging design,” Mach said.
A product’s Device Master Record (DMR) must include packaging specifications. “It should note how to build, package and box the device,” Mach said. “It might also include in-process testing, such as minimum peel force and seal width, as outlined by various ASTM methods.”
The DMR should define critical quality attributes and acceptance criteria. “Purchasing departments use this information to source raw materials and supplies,” Mach said. “This documentation ensures the packaging system meets quality, safety and functionality standards, which are FDA’s primary concerns during inspections.”
Package verification involves examining and providing objective evidence that the requirements identified in the DMR are fulfilled. It requires package tests, materials testing for biocompatibility and bioburden testing.
Package tests must be validated, which takes about six months to complete. “Validation confirms that the objective evidence has been consistently met across multiple lots,” Mach said. “This is where neglecting packaging design until the end of product development can cause problems.”
Mach said packaging validations, which are governed by ISO 11607: Packaging for Terminally Sterilized Medical Devices, are intense but follow an easy flow that assesses various shipping environments and the different temperatures the product will encounter during transit.
Distribution testing examines factors such as drop shock, vibration frequencies, altitude and compression. Packaging is also exposed to a range of temperatures, from -29°C to 95°C. High humidity and desiccated environments are also used. “Packaging materials are essentially put through the wringer,” Mach said.
ASTM D4169: Standard Practice for Performance Testing of Shipping Containers and Systems guides distribution testing. Mach said the standard has recently been updated to reflect current shipping technology, specifically as it pertains to vibration standards. “Testing used to be based on trucks with leaf springs, which have a higher shock capacity compared to modern air ride systems,” she said. “It’s great to see testing methods evolving with technology, reducing unnecessary stress and preventing artificial failures in packaging configurations.”
The integration of artificial intelligence in this process is also an exciting development, according to Mach. “Companies can monitor the entire shipping process in real time to collect and analyze data on temperature fluctuations and other environmental factors,” she said. “This information reveals what packages experience during transit and ensures testing methods are not overly extreme.”
Testing the Performance
Companies should conduct three tests at baseline to assess packaging solutions: strength, integrity and microbial barrier. Mach suggests repeating these tests at a minimum of two additional points: an accelerated aging time point (usually at the shelf life’s end) and a real-time point.
Mach highlighted the importance of conducting the same tests throughout each time point that were run at baseline. Switching tests might make it appear like you’re covering up a failure,” she said. “Consistency is key.”
Ensure the sample size you use is statistically valid, Mach noted, because FDA has specific preferences for statistical levels for attribute and variable data. “Justify your methods and sample sizes according to the test methods and output requirements,” she added.
Mach served as the technical expert for the ASTM F1608 test, which uses the exposure chamber method for microbial ranking of porous packaging materials. She said FDA has stressed the importance of running the test more than once.
“This ensures that the packaging material maintains its microbial barrier effectively throughout its lifecycle,” she said. “If you’re not demonstrating strength, integrity and a microbial barrier across multiple time points, you can’t be sure the packaging will remain valid and sterile throughout its labeled shelf life.”
Mach recommends noting a separate shelf-life validation on packaging labels. “Distinguishing between storage and transportation temperatures is crucial,” she said. “Storage temperature is usually 25°C, but the packaging range is set from distribution and that can include higher temperatures.”
Real-time aging must be used with accelerated aging to test a product’s shelf-life, Mach noted. “This newer standard was introduced because companies were relying solely on accelerated aging, which is only optional data, without providing real-time aging information,” she said.
Don’t overlook the impact packaging suppliers can have on the overall performance of the solutions they provide. “Despite quality agreements, suppliers might make small changes that seem insignificant to them but can have significant impacts on your end product,” Mach said. “Always consider that a supplier change could be a factor in packaging failures.”
Essential Element
Orthopedic device manufacturers continuously seek to design, develop and produce devices that are safer and cost-effective. Achieving these goals involves considering packaging design inputs early in the product development process and assessing them through regular reviews, validations and verifications.
“Doing so will help you succeed and bring your product to market faster,” Mach said.
DC
Dan Cook is a Senior Editor at ORTHOWORLD. He develops content focused on important industry trends, top thought leaders and innovative technologies.