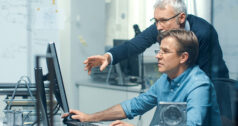
Computational modeling and simulation (CM&S) tools are fast becoming indispensable in the design and development of orthopedic devices. CM&S allows designers to create detailed 3D models of implants and devices in ways that accurately represent how the solutions will work in real-world practice.
Marc Horner, Ph.D., Distinguished Engineer in Healthcare at Ansys, a company that develops simulation software, said that CM&S is yet another frontier where orthopedics is benefiting from technology that advances personalized patient care. “The industry is continually exploring innovations that benefit patients or reduce costs,” he explained.
Dr. Horner said CM&S can also optimize the product development process in ways that the orthopedic industry is only beginning to tap into. For example, he said, the impact that new materials have on implant performance and the evaluation of alternative sterilization processes can be achieved through physics-based modeling.
CM&S creates virtual prototypes of devices and tests them in simulated environments before they are used in patients, reducing the need for physical prototypes, which can be costly to manufacture. Designs developed through CM&S also allow for rapid iteration and refinement of materials, dimensions and geometries — and simulate their effects on device performance without the time and expense of creating new physical prototypes.
Product engineers are therefore able to identify potential design flaws and performance issues early in the development process, reducing costly downstream redesigns and potential recalls. Engineers can analyze factors in real time, such as stress distribution, fatigue resistance and wear characteristics, to identify areas for improvement and optimize designs for maximum performance and longevity.
CM&S can also streamline the regulatory approval process by providing comprehensive data and analysis to support submissions to regulatory agencies. This can reduce the time and resources required to obtain regulatory approval, speeding up the time to market for new devices. By leveraging advanced simulation tools and techniques, orthopedic companies can innovate more efficiently to commercialize high-quality devices faster and at a lower cost.
Capitalizing on the Potential
Dr. Horner said that CM&S can support implant development throughout a product lifecycle, but is especially important in the design stage. “This is because the early insights provided by modeling and simulation help to identify design weaknesses very early in development,” he explained. “Most feasible designs progress to prototyping and eventually manufacturing.”
CM&S can also streamline physical testing during design validation. For example, a typical requirement for hip stems is to ensure that they have sufficient fatigue strength and wear resistance. “The burden on mechanical testing can be significant,” Dr. Horner said, “because these devices come in multiple sizes to fit the diverse patient population. But instead of testing every size in the family of implants, CM&S can be used to identify the worst-case implant size for mechanical testing. This results in significant savings in testing time and cost.”
Another benefit, Dr. Horner explained, is that CM&S increases product development throughput and reduces the risk of redesigning late in the process. “This means that manufacturers are getting to market earlier than expected,” he said. “That means companies are not only generating additional revenue but also differentiating themselves from competitors, which are top-line concerns in today’s competitive environment.”
CM&S allows product engineers to sweat design details and create and edit features long before a product is produced to save time and money on the front end, while helping to create the best possible end products for patients.
For example, many orthopedic implants are now created using additive manufacturing (AM). Dr. Horner said these implants are lighter, provide more flexibility in their design and exhibit improved biocompatibility.
“An AM approach to implant design decreases development time because rapid prototyping can be used to create test specimens,” he said. “But AM implants also introduce technical design challenges, which the orthopedic industry is addressing with CM&S.”
Many current AM build process simulations can accurately forecast induced residual stresses, distortions, recoater interference, surface roughness, hotspots and shrink lines.
“Multi-scale simulations can also predict the presence of manufacturing process defects on the microscale and macroscale,” Dr. Horner said. “Simulations also deliver insights on the expected material properties, which can be used to fine-tune property distributions.”
Integrating AM simulations with durability analysis aids in the development of orthopedic implants with lattice structures, Dr. Horner noted. “This enables the prediction of thermal hotspots, porosity and residual stresses that could influence implant mechanical performance,” he said. “End-to-end AM simulation workflows can also help design engineers understand stress relief processes.”
The ability to preempt problems that products could introduce to patients before they happen may be impossible to monetize, but AM simulation can help to ensure that a component is free of defects from the first printing prototype, thereby reducing lead times, trial-and-error iterations, costs and surgical planning. It can also ensure that the part is durable and complies with regulatory requirements, Dr. Horner said.
One important trend that Dr. Horner is closely observing is how orthopedic manufacturers are not only relying more heavily on CM&S to accelerate R&D, but ways in which CM&S is being incorporated into apps that automate repeatable workflows.
For example, the ASTM F2996 standard currently outlines a step-by-step procedure for performing stress analysis in hip stems. “Because of their prescriptive nature, standards such as these are readily implemented into vertical software tools,”
Dr. Horner said. Benefits to the R&D process include rapid design iteration, automated reporting and compliance to the requirements of the standard.
“CM&S apps broaden the availability of simulation,” Dr. Horner explained, “because many of the technicalities associated with using specific computational tools are ‘behind the curtain’ and managed in the background.”
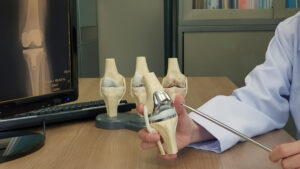
Modeling and simulation can improve how well orthopedic implants function in clinical practice.
Scratching the Surface
Industry experts are determining how to move CM&S processes forward to ensure that better use of the technology allows for improved overall manufacturing specific to orthopedics.
Dr. Horner said a well-established regulatory framework supporting the use of CM&S as part of medical device submissions needs to be widely available to device manufacturers. Currently, the framework is described in the recent
FDA guidance document “Assessing Credibility of Computational Modeling and Simulation in Medical Device Submissions,” which defines an end-to-end process for using the testing results in regulatory submissions, from planning to execution to assessment and reporting of the model.
Dr. Horner said the current document borrows heavily from the ASME V&V 40 standard on “Assessing Credibility of Computational Modeling through Verification and Validation: Application to Medical Devices.”
For background, this guideline was initially developed in collaboration among device manufacturers, FDA and other industry stakeholders to address concerns regarding the required level of model credibility for CM&S activities. To better address these issues, Dr. Horner said the standard needs to outline a risk-based framework for establishing the credibility requirements of a computational model.
“Lower-risk modeling activities require less verification, validation and uncertainty quantification than high-risk modeling activities,” Dr. Horner said.
This, he added, is a major benefit for device manufacturers and regulatory bodies because it allows them to have a structured discussion about how much validation needs to be performed before initiating the modeling activity.
FDA’s guidance, when used with the ASME V&V 40 standard, provides a predictable and consistent pathway for using CM&S as part of regulatory submissions and represents a major step forward for the industry, Dr. Horner said.
The orthopedic industry is also exploring the use of in silico clinical trials (ISCTs) to understand device performance in patients even before new products are released, Dr. Horner added.
ISCTs replicate a clinical trial to assess a product’s performance related to a clinical endpoint. The simulation needs to incorporate patient anatomy and physiology, treatment delivery, as well as the patient’s response to the treatment.
“The process begins with databases of imaging data that can be used to create a virtual population of bone shapes and associated bone quality metrics,” Dr. Horner explained.
Loading conditions that represent activities of daily living — such as standing, walking and sitting — are applied to simulate the patient’s movements as they go about their day, according to Dr. Horner. He said the patient response in terms of stresses and other factors is summarized and evaluated for the entire patient cohort to predict real-world performance.
Dr. Horner admitted that while strides in ISCTs provide significant benefits, they also come with unique challenges. For example, ISCTs require a significant degree of automation because of the substantial number of virtual patients who will be evaluated.
“They also require significant computer resources to evaluate the virtual patient cohort under all use conditions,” Dr. Horner said. “We are working to support process automation coupled with high-performance computing and automated reporting to help manufacturers reach this new horizon.”
These advances are poised to improve the development of orthopedic devices and their uses in patients. They’re also helping to create solutions in newer and more accurate ways that improve fit and function, minimize trauma at the surgical site and optimize clinical outcomes.
It’s expected that products created through CM&S will show better long-term performance by predicting how wear, fatigue and material degradation will fare over time, ideally reducing implant-related complications and the need for revision surgeries in most cases.
Overall, CM&S offers a cost-effective means of improving the design and development of innovative orthopedic devices. That much is easy to predict.
NHM
Natalie Hope McDonald is a contributing editor.