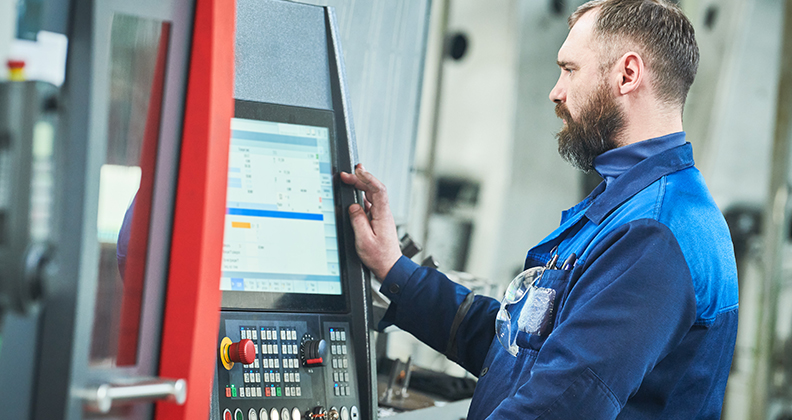
Think about the intimidation factor of standing in front of a CNC machine’s control panel for the first time. Deciding which buttons to push and which dials to adjust must feel like trying to choose between cutting the red or blue wire of an explosive.
“The initial intensive training can be overwhelming for someone who has never worked in orthopedic manufacturing,” said Ted Bloomfield, Vice President of Operations and Machining at Orchid Orthopedic Solutions. “Their heads are spinning because of all the information they’re asked to absorb.”
It’s no wonder finding new workers to fill orthopedic manufacturing jobs has become extremely difficult as experienced machinists retire and workforce shortages limit the talent pool. Plus, some new hires quit before they’ve had a chance to get their feet wet.
“The effective training of new workers is at a premium,” Bloomfield said. “In many cases, you’re teaching someone who has never worked in orthopedic manufacturing, so getting them up to speed can be challenging. We recognize that starting out in manufacturing is intimidating, and we’re committed to reducing uncertainty for every new associate.”
Orchid has gradually implemented a comprehensive onboarding program and learning culture that continues to evolve. The effort has decreased the employee turnover rate by about 10%, particularly among workers who have been on the job for less than a year. Investing in the proper onboarding of employees pays off; Bloomfield estimates the training of new hires costs about $50,000.
Building your onboarding protocols on the following foundational elements will make sure new hires — no matter their roles — hit the ground running and understand the value of committing to a career in orthopedic manufacturing.
Structure the Process. Bloomfield suggests taking a project management approach to the training of new hires. “We’ve developed a structured plan that resembles a Gantt chart,” he said. “Each step is spelled out and serves as a communication tool, ensuring new team members remain on the right path throughout their orientation.”
During the first three days on the job, Orchid’s new hires complete a comprehensive orientation that covers a wide range of information, including mandatory safety procedures and regulatory requirements, before they step onto the production floor. Bloomfield said that replacing text-heavy directives with diagrams and pictures makes the teaching points easily digestible and more memorable.
Check in Regularly. Documenting the performance of new hires allows you to compare the progress of individual workers as they move through the training process. Bloomfield said Orchid’s leadership meets with new hires at the two-week mark to provide feedback about how they’re doing. That might sound overbearing but, in fact, the opposite is true.
“It’s our way of ensuring they’re meeting our expectations, which helps them feel at ease,” Bloomfield said. “We want to make sure everyone feels comfortable and confident. This approach creates a supportive environment for our team members.”
Bloomfield suggests meeting with employees 30, 60 and 90 days after their start date to discuss their ongoing performance. The goal is to make sure new hires are learning the required skills, integrating with the team and feeling comfortable with their progression.
“Some new machinists question whether they’re cut out for the job,” he said. “It’s crucial to reassure them that feeling that way is expected. Let them know that veteran associates experienced the same uncertainty and once faced the same early challenges.”
One-on-one meetings with new associates also provide insights into what they like and don’t like about their position. “Recognize that people have varying workplace preferences,” Bloomfield said. “Some associates want to develop complex machining skills while others are completely satisfied with simpler responsibilities. By understanding an employee’s preferences, you can tailor a personalized career path that aligns with their aspirations.”
That doesn’t mean workers shouldn’t be nudged out of their comfort zones if you recognize that they have the potential to offer more than their current responsibilities.
“Anyone in any type of position needs someone who believes in them and provides encouragement,” Bloomfield said. “Taking a step outside of your comfort zone often requires a degree of support and motivation to take that risk. This is where effective communication is truly essential. One-on-one discussions allow individuals to receive the feedback they need to look beyond their current responsibilities. Having someone who believes in them is crucial to their success.”
Tap into Trainers. Assigning experienced machinists to train new hires is an effective strategy. Their practical advice and understanding of the difficulties involved in learning new skills are reassuring. Not everyone has the natural abilities to be an effective trainer, however, so consider personalities and a willingness to help others when identifying employees to serve in the role.
“A good trainer possesses specific qualities,” Bloomfield said. “They serve as mentors and coaches, helping new hires feel comfortable and supported during the onboarding process.”
Effective trainers also pay attention to the seemingly small details that can make a significant difference to new hires, such as making sure they have someone to sit with at lunch.
“It’s tough to feel comfortable in a new job surrounded by complete strangers,” Bloomfield said. “Creating an environment that fosters a feeling of belonging is essential. As new associates start to make friends and settle in, life becomes easier for everyone on the team.”
Promote Future Growth. Outline and share potential career paths that make working in orthopedic manufacturing an exciting opportunity. Make sure new hires understand that they can move through several tiers as their skills develop, evolving from a bench operator to a sophisticated CNC machinist in five to seven years — and the significant jump in salary and responsibilities they’ll achieve.
Bloomfield pointed out that the detailed documentation of an effective onboarding process provides written proof of clear career pathways and the benefits of progressing along them.
It’s also beneficial to develop employees with a cross-functional team approach in mind. “This ensures skilled associates can step into various roles when staff scheduling challenges arise,” Bloomfield said.
Cross-training also provides new hires with the opportunity to diversify their skill sets and allows them to explore different roles within the company. This versatility exposes them to potential new opportunities that could increase staff retention.
Having a documented training program in place gives employees added confidence to advance their careers. “The difference between taking an ad hoc approach versus a structured process is significant,” Bloomfield said. “When associates know trainers and leaders have a plan in place to help them acclimate to new roles, they’re more open to learning additional skills and growing within the company.”
This level of support also helps to boost workplace morale.
“We’ve had employees express their gratitude for the investment we’ve made in their development,” Bloomfield said. “Effective onboarding and training lead to significant personal and professional growth among team members. We witness individuals flourishing in their roles and being enthusiastic about working in manufacturing. This energy and drive are palpable and create a positive work environment.”
DC
Dan Cook is a Senior Editor at ORTHOWORLD. He develops content focused on important industry trends, top thought leaders and innovative technologies.