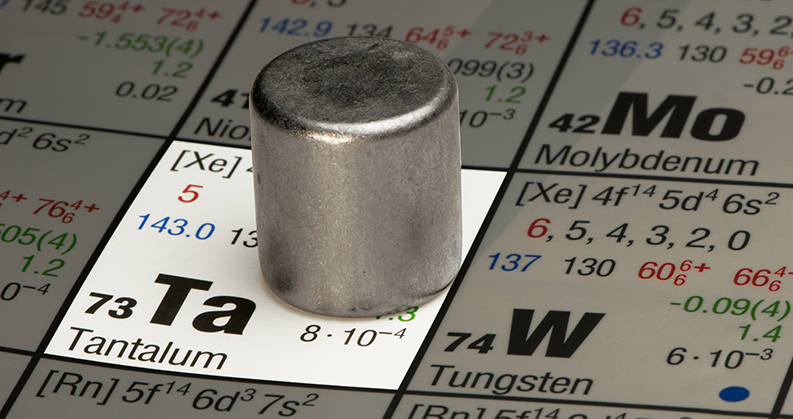
After decades of successful use in orthopedics, tantalum metal is once again at the forefront of discussions about advanced materials used to make orthopedic implants thanks to its biocompatibility, osseointegration and properties that reduce the risks of surgery.
Croom Medical and Global Advanced Metals (GAM) have recently collaborated to introduce a tantalum-based additive manufacturing capability.
“The use of tantalum scaffolds in medical implants is well established, though historical commercial successes are not based on 3D-printed tantalum scaffolds,” said Shane Keaveney, R&D Manager at Croom Medical. “The platform at Croom Medical allows OEMs to leverage tantalum into the design of implants and create scaffolds that enhance osseointegration and fixation.”
It Takes Two
U.S.-based GAM has more than 70 years of experience in manufacturing high-grade tantalum powders, typically for use in electronics and other applications. The company recently developed a spheroidized tantalum powder to 3D print parts with the material.
Croom Medical in Ireland is a contract manufacturer serving medical device companies and other OEMs. Their expertise in additive manufacturing has increased in recent years, with more than 20,000 additively manufactured devices completed to date.
The two companies have teamed up to offer contract manufacturing services. The partnership capitalized on GAM’s spheroidized tantalum powder and Croom Medical’s additive manufacturing, testing and finishing processes. GAM will provide spherical tantalum powder derived from ethically and conflict-free sourced tantalum raw material. The team at Croom Medical will manufacture devices and components using a recently acquired GE M2 printer that’s solely dedicated to the project and material and used for prototyping and volume manufacturing.
Addressing Known Risks
Any implant surgery involves risk. These risks may include failed devices, toxicity and thrombus formation. Porous tantalum, however, lends itself to implantable devices. Studies have demonstrated its biocompatibility, resistance to blood clot formation and corrosion, osseointegration and high ductility and fatigue strength.
Tantalum’s enhanced osseointegration alone is expected to significantly reduce the need for revision surgeries. Tantalum showed improved bone grafting performance when compared with the more common device material Ti6Al4V in controlled studies. It also integrated better with natural anatomy and demonstrated improved long-term performance. Furthermore, its high surface friction stabilizes devices after implantation for better bone growth.
Gordon C. Smith, Sc.D., Chief Technology Officer at GAM, noted that around 10% of individuals who have a surgical procedure involving an implant need to have it revised. The majority of these revisions are due to the implant shifting or becoming dislodged, necessitating it to be replaced. Reducing revisions by about 10% represents a multi-billion-dollar savings to insurers and providers, according to Dr. Smith.
The mechanical properties of tantalum prevent stress shielding, which leads to osteoporosis. Bone must carry load (stress) to maintain mass. Without load over an extended time, bone sheds calcium and becomes weak and brittle. These risks are lessened with tantalum because its mechanical properties closely match those of natural bone. Further, the material has high fatigue strength, meaning implants are not likely to fail under repeated use.
Tantalum’s radiopacity also provides a high contrast during intraoperative imaging, a benefit that gives orthopedic surgeons a clearer picture of an implant’s placement and accuracy.
Added Customization and Performance
Additive manufacturing offers several advantages in the production of tantalum. It reduces material waste, adds design flexibility, creates complex geometries and allows for customization. The orthopedic industry is evolving toward personalized solutions. Additive manufacturing provides a way to make devices that fit the individual needs of patients.
“Additively manufactured and customized tantalum scaffolds offer the advantages of customization in conjunction with improved osseointegration,” Dr. Smith said. “A customized device matches a patient’s anatomy. Altering the pore size and geometry of the implant optimizes bone fixation.”
Additive manufacturing will likely offer a more affordable customization solution compared to traditional subtractive manufacturing approaches. The reproducibility of additive manufacturing processes, as well as the reduced scrap, have positive impacts on the bottom line.
Furthermore, the 3D printing of tantalum allows for the tailoring of porosity to optimize mechanical properties and the rate and depth of bone fixation for an even more customized approach to patient care.
“With 3D printing, gradations in porosity within the same implant could be easily implemented,” Dr. Smith said. “Future tantalum implants will be unencumbered by design limitations, enabling even more advanced performance.”
Multiple companies, including Croom Medical, Amnovis and ARCH Medical, will provide in-booth presentations on advancements in materials and additive manufacturing at OMTEC 2023.
HT
Heather Tunstall is a BONEZONE Contributor.