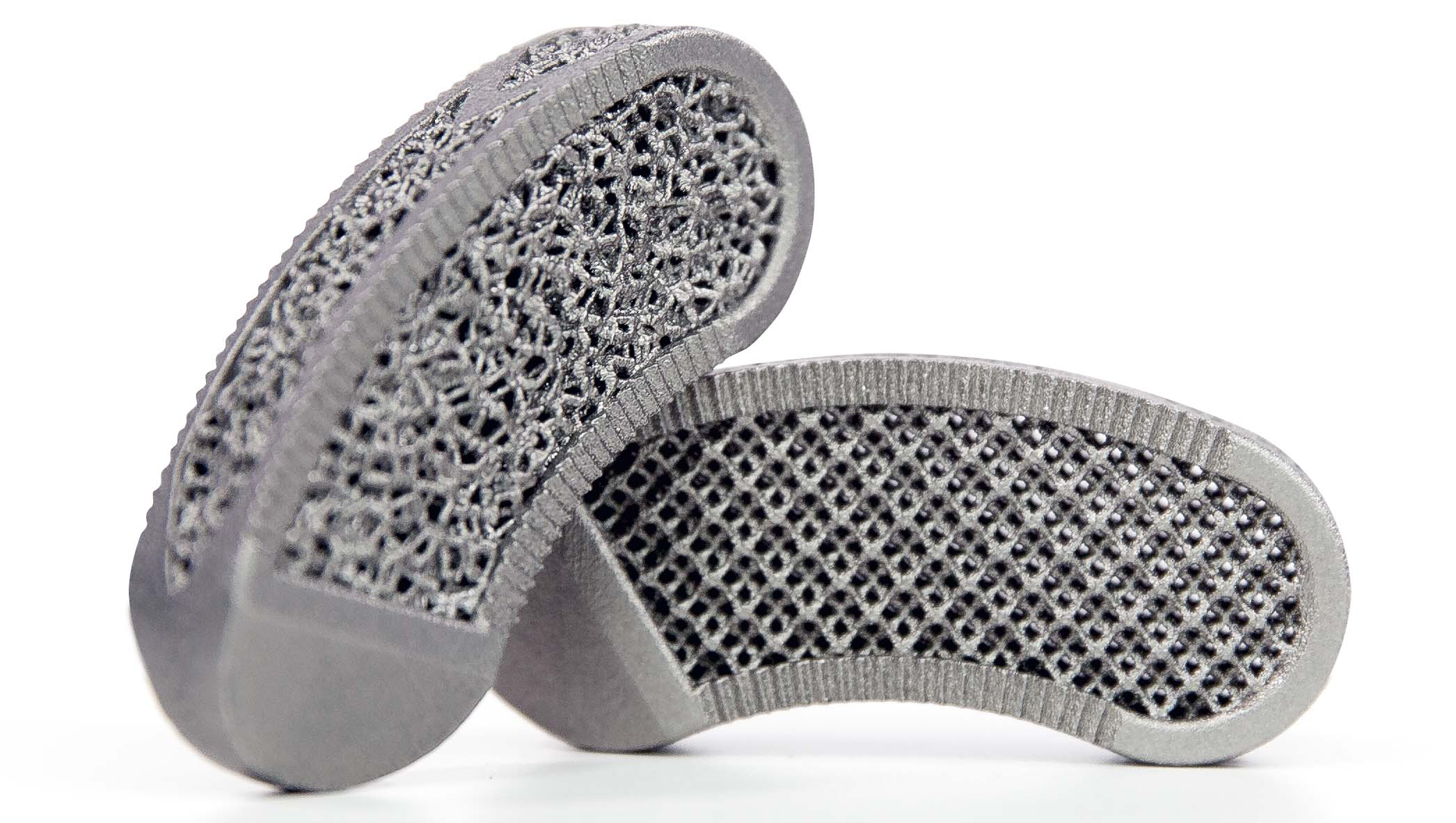
With more than 1.6 million patients seeking treatment for adult spinal deformities, the market for interbody cages is growing. To help meet the demand, spine companies have adopted 3D-printed titanium implants.
Additive manufacturing or 3D printing enables the design of porous scaffolds and intricate lattice structures that have been shown to optimize bone ingrowth. Additionally, with ongoing productivity improvements, such as multi-layer print platforms, direct metal printing offers a more cost-effective alternative to traditionally manufactured devices.
This webinar discusses new innovations and trends in additive manufacturing for orthopaedic spine surgeries. The panel of experts from 3D Systems share recent applications such as:
• The Kumovis R1, a new extrusion platform enabling manufacturers to 3D-print interbody cages in PEEK with biphasic calcium phosphate to enhance cell attachment and proliferation
• Trial spacers in Radel® PPSU that are resterilizable up to 500 cycles and available with barium sulfate filler for X-ray visibility
• Bone plates in carbon-fiber-reinforced PEEK (CFR-PEEK), an implantable material with a modulus close to human bone
• Patient-specific interbody devices in titanium, which have demonstrated better planned spinal alignment, reduced stress on endplates, and improved bone graft loading when compared to standard devices