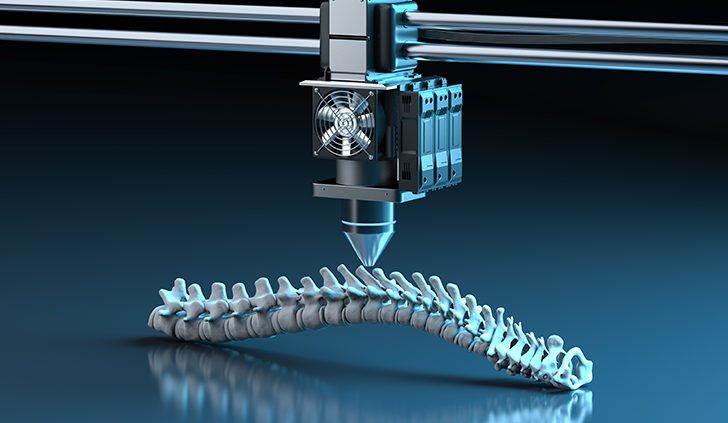
Additive manufacturing continues to see rapid adoption in the spine market. Spine companies seek to leverage additive manufacturing or 3D printing in order to create complex structures and lattice structures that provide better surfaces for osseointegration. We’ve seen nearly all established spine companies add additively manufactured products to their portfolio in recent years.
In anticipation of our launch of THE ORTHOPAEDIC INDUSTRY ANNUAL REPORTⓇ, we looked at the spine products mentioned in the report and highlighted a handful of them here.
Camber Spine, SPIRA-P and SPIRA-T Implants
News of Camber Spine’s national launch of its SPIRA-P Posterior Lumbar Spacer and SPIRA-T Oblique Posterior Lumbar Spacer devices came shortly after the company revealed it received FDA 510(k) clearance for both products.
Camber’s additive products include a patented open architecture design for optimal endplate load distribution. The uniquely designed surfaces allow for cell adhesion and bone cell proliferation, while the interconnected porosity design mimics bone. The company also designs with an arch shape to better distribute load.
The SPIRA-P Posterior Lumbar Spacer can be utilized to accommodate PLIF or TLIF procedures. The SPIRA-T Oblique Posterior Lumbar Spacer is designed specifically to accommodate traditional or “insert and rotate” TLIF procedures. Further, its shape is angled for a 25° oblique insertion technique to optimize lordosis.
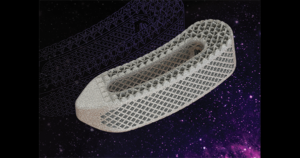
In March 2021, Osseus Fusion Systems officially launched Aries-TC, its 3D-printed transforaminal curved interbody fusion device.
NanoHive Medical, Hive Standalone ALIF System
NanoHive Medical’s Hive Standalone ALIF is a fixated Soft Titanium latticed 3D-printed implant system for anterior lumbar interbody fusion. It is the latest addition to the Hive biomimetic portfolio of interbody spinal devices that leverage the company’s proprietary rhombic dodecahedron lattice design. The implants provide surgeons and patients with biomechanical elastic modulus properties comparable to PEEK, improved diagnostic imaging capability and osteoblastic cell attraction and integration.
NanoHive recently made multiple strategic announcements regarding expansion of its portfolio. In May, the company announced the issuance of U.S. Patent No. 11,253,368 B2, Methods of Designing High X-Ray Lucency Lattice Structures. The company also entered into an agreement with Accelus to expand the distribution network for NanoHive’s Hive Soft Titanium portfolio of interbody fusion devices in the U.S.
NuVasive, Modulus ALIF Porous Implant
NuVasive commercially launched Modulus ALIF, a 3D-printed porous titanium implant for anterior lumbar interbody fusion, in targeted global regions. The product provides implants and instrumentation designed for both supine ALIF and XALIF procedures. Modulus ALIF comes in a variety of sizes and lordotic options to accommodate varying patient anatomy. Highlights of the Modulus ALIF technology include proprietary Modulus titanium design, zero-step locking mechanism as well as low-profile, versatile instrumentation.
This additively manufactured device is the latest addition to NuVasive’s Advanced Materials Science portfolio. We mentioned that orthopedic companies and spine companies, in particular, have rapidly adopted additive technology. In 2015, NuVasive saw an opportunity with additive manufacturing, and went from concept to commercialization in 14 months.
Osseus, Aries-TC Interbody Fusion Device
Osseus Fusion Systems officially launched Aries-TC, its 3D-printed transforaminal curved interbody fusion device. Aries devices are constructed from highly porous, 3D-printed titanium optimized for bone fusion and biological fixation using PL3XUS, Osseus’ proprietary 3D-printing technology.
PL3XUS titanium technology utilizes Selective Laser Melting to create a three-dimensional diamond lattice network with roughened surface topography designed to promote bony fusion onto, into, and throughout the device.
Rob Pace, CEO of Osseus, recently called additive manufacturing the gold standard for spinal fusion devices and a technology poised to deliver creative solutions to existing problems for both implant and instrument designs.
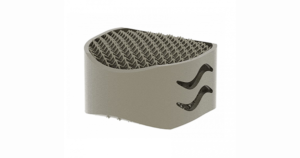
Tsunami Medical introduced Capri-Z, a 3D-printed ACIF cage with a built-in fixation mechanism. The product builds on the first generation ACIF cage Capri (pictured).
Tsunami Medical, Capri-Z
Tsunami’s Capri-Z is a 3D-printed ACIF cage with a built-in fixation mechanism. The product builds on the first generation ACIF cage, Capri. CEO Stefano Caselli said, “The choice for pins instead of screws as an additional fixation mechanism meets with the standards of successfully proven Bone InGrowth Technology.”
Pins also do not require additional raw material on the cage to facilitate the fixation mechanism, therefore the elasticity modulus of the implant is not compromised. Peter Witke, CCO, said that the pins are placed diagonally into the cage, securing rotation stability. The cage is printed in one step, for which there is no assembly of parts required afterward. Implantation and extraction of the pins are performed with the same introduction instrument.
These are just five of the dozens of spine companies adopting additive manufacturing. We expect companies to continue to iterate and innovate as the spine space and additive technology advance.