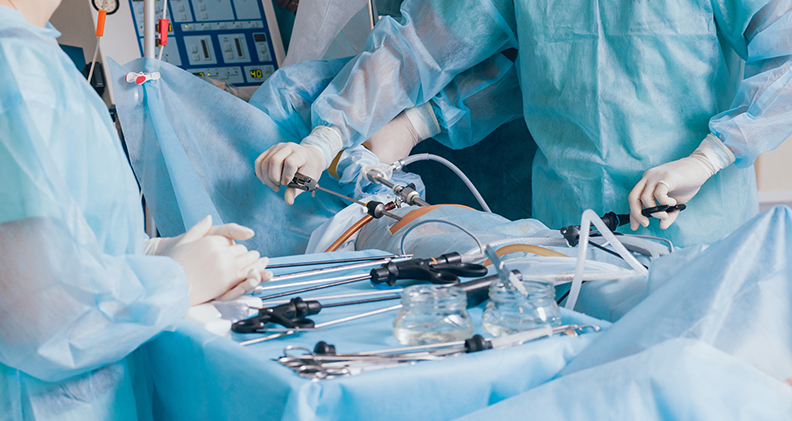
Orthopedic engineers need to account for design, manufacturing, regulatory, quality considerations and more when choosing the best materials for their application. Thermoplastic shapes offer orthopedic companies broad applicability for their implants and instruments. We seek to answer four questions, ranging from design to sterilization, that orthopedic companies often ask about incorporating thermoplastic shapes in their next product launch.
Can you give us an idea of the range of the products and services you offer the medical industry? What are some examples of how they can be used?
Mitsubishi Chemical Advanced Materials’ (MCAM) Life Science Grade (LSG) portfolio consists of pre-assessed thermoplastic shapes developed for the fabrication of medical devices, surgical instruments and diagnostic equipment. Customers have found that our LSG portfolio contains excellent candidates for a wide range of applications with a variety of sterilization and performance needs. Typical applications include surgical instruments, target devices, diagnostic equipment, robotics, and lab equipment.
In addition, the MediTECH® implantable polymers division manufactures thermoplastic shapes compliant to ASTM F648 and ISO 5834-2 for UHMW-PE and ASTM F2026 for PEEK. These materials have been selected by customers for use in Class III implants (>30 days). Implantable polymers, such as UHMW-PE and PEEK, have been used for surgical orthopedic implant applications, including large joint orthopedics, knee and hip implants, spinal cages and suture anchors.
MCAM is in a unique position to support customers from the orthopedic device development through surgical instrument, sterilization and sustainability efforts.
How are you developing new materials and manufacturing technologies to respond to the changing regulatory environment and industry trends?
At MCAM, we focus on combining our knowledge of the global regulatory landscape, industry segments, point of care research and customer engagement, which drives our R&D strategy. This allows the company to identify unmet needs and industry trends, which drives the development of innovative products and technology solutions for medical device developers.
Once an unmet need is identified, MCAM can initiate a fast-track process of research, testing and support to beta test solutions before the commercialization of new shapes to make sure they are properly validated. Equally, MCAM’s highly integrated supply chain enables full collaboration between our R&D and materials teams throughout the product development cycle, so customers can experience a significant reduction in time to market of the resulting shapes.
MCAM’s exclusive SPRINT™ (a technology platform for rapid injection molding of functional parts) and free-form injection molding manufacturing technology can help medical device manufacturers compress prototyping development down to three to five days, which may assist customers in providing an accelerated path to FDA 510(k) clearance and production.
In addition, our unique clean compounding system (CCS) for manufacturing thermoplastics shapes significantly reduces gels, inclusions and black specks, resulting in much higher quality devices and improved productivity through the fabrication process.
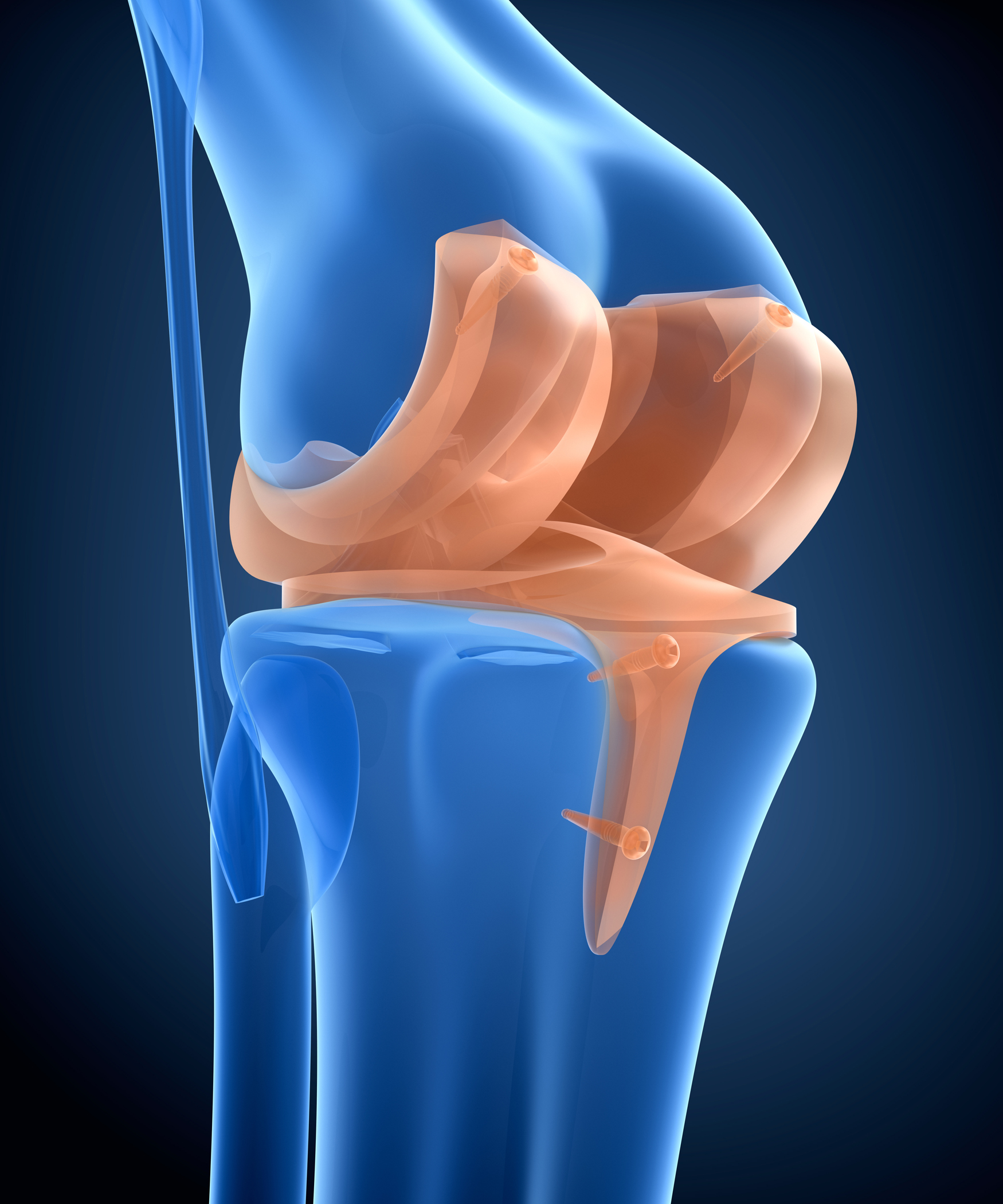
An x-ray illustration of knee and titanium hinge joint.
What’s your approach to working with product developers to support their designs and identify the right materials and technologies for their needs? How does that feed into your R&D strategy?
Strategic collaboration and good communications with our customers is key to supporting their designs. Once identified, MCAM can initiate a R&D fast track process of research, testing, and support to beta test solutions before commercialization to make sure they are properly validated. We recognize that enhancing the patient’s positive experience is the ultimate goal. Utilizing collaboration, combined with concurrent engineering, we can significantly compress the product development cycle and lead to a truly differentiated medical device or implant.
How do you approach challenges around sterilization across such a wide portfolio?
MCAM looks at sterilization needs from the regulatory level to the point of use. As an example, because of issues around healthcare-acquired infections (HCAI) and the spread of COVID-19, chemical wipes and disinfectants have been getting more aggressive. To keep up with this, we have continued to enhance our chemical and environmental stress cracking (ESCR) testing protocol, which helps support customers informed decisions about suitability for use. In addition, MCAM has initiated ultraviolet C (UVC) testing protocols to understand the cosmetic and mechanical effects on our portfolio from UVC and other technologies to develop new products.
Ensuring MCAM understands the latest industry sterilization needs like UVC, combined with maintaining an updated sterilization database for our portfolio, allows us to provide customers with a variety of product options and support data to guide them to suitable material for use in their applications with high confidence, reduced risk and improved safety.
Eric Tech is Strategic Growth Manager Healthcare, Mitsubishi Chemical Advanced Materials.
Mitsubishi Chemical Advanced Materials (MCAM) is a global leader in the production of engineering thermoplastics and composites in the form of semi-finished shapes and finished parts. We partner with customers to help them find the right materials, designs, and production systems to get their ideas to market with greater safety, speed and confidence. The MediTECH® division at MCAM is the purveyor of the market’s most comprehensive portfolio of implantable UHMW-PE and PEEK stock shapes.