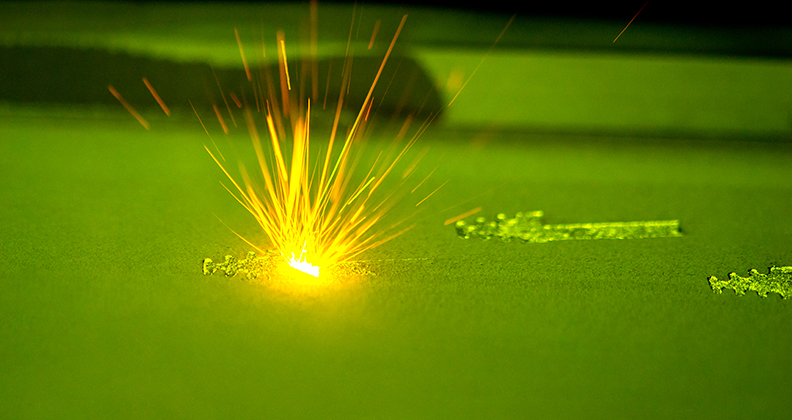
As additive manufacturing continues to shape the orthopedic industry, companies face a host of exciting new opportunities and solutions. The next five to ten years will deliver even more profound 3D printing advancements for the design and manufacture of orthopedic implants.
What makes additive manufacturing an endlessly challenging and promising technology is the sprawling scope of what’s possible to create through it, said Steve Willis, Director of Product Development at Camber Spine.
“Whatever the engineer can think of, you can print it,” Willis said. “That opens the door for a lot of innovation – a lot of different things that you couldn’t do with [subtractive] manufacturing. Also, now you can incorporate features into your device that can contribute to the fusion and healing processes.”
We spoke to three orthopedic companies leveraging the technology to consider what the next generation of additively manufactured devices might look like and the challenges ahead.
Designing Shape and Surface
A focus on surface technology and implant geometry has led Camber Spine’s portfolio development. The company uses 3D printing to imbed highly complex porous structures onto implants that adhere naturally to bone; these are designed with an arch shape to distribute the load throughout the entire surface of the implant.
Camber Spine’s Vice President of Contract Manufacturing, Bob Henderson, said that the open surface of the arched implants features highly complex porous structures designed to promote cell attachment and proliferation.
“The trabecular surface that’s added to those arches provides that mechanical fusion, that initial fixation,” Henderson said. “Not only do we have load distribution, but we also have something on the surface that can help with the fusion process.”
The company’s implants are engineered to imitate spongy bone. According to Henderson, the technology needed to print structures so complex didn’t exist five years ago.
“One thing that’s really exciting about 3D printing is that the laser parameters to make spongy bone are different from the laser parameters to make the solid core of the part,” Henderson said. “The parameters’ sets have developed so much in the last five years that we can zone right in on that spongy surface and create an immensely repeatable process.”
Camber Spine’s 3D printing achievements weren’t developed without overcoming significant challenges, Willis said. Understanding and combining the disparate pieces that additive manufacturing relies on to function was a considerable challenge for adopting the technology and pushing it forward. This is a challenge that will continue as additive manufacturing evolves.
“It’s challenging to understand any given application for 3D printing, because of the range of machines, software, powders, etc.,” said Willis. “For anyone starting in 3D printing, it’s a challenge because it’s new.”
Designing for the Procedure
Osseus Fusion Systems specializes in developing minimally invasive spinal procedures. Additive manufacturing is critical to the company’s identity and mission.
Rob Pace, CEO of Osseus, called additive manufacturing the gold standard for spinal fusion devices and a technology poised to deliver creative solutions to existing problems for both implant and instrument designs.
“It allows us to produce highly porous interbodies while maximizing mechanical strength, endplate contact area and graft volume,” he said. “Our patented mesh design creates 80% negative space, meaning a surgeon can fit more bone graft into the interbody without sacrificing endplate contact area, which decreases the risk of subsidence. Additionally, the additive manufacturing process creates micro-roughness, which, when combined with our proprietary multi-axis mesh, promotes boney on-growth, in-growth and through-growth throughout the implant to enhance fusion.”
When asked how his company is using additive manufacturing in ways that set the company apart from its competitors, Pace pointed to better serving the patient and surgeon instead of purely focusing on the implant.
“Most of what we see with additive is focused on the implant,” he said. “In developing our new PISCES-SA system, Osseus implemented AM to design better instrumentation that helps the surgeon and the patient. Our new PISCES-SA interbodies utilize continuous endplates that maximize the biocompatibility of titanium, allowing the implant to actively participate in the fusion process.”
When it comes to advancements in additive manufacturing, Pace pointed to the need for better collaboration amongst all players. Pace said that as technology evolves, device companies, suppliers, manufacturers, sterilizers and standard and regulatory bodies need to improve communication.
“Additive manufacturing processes are improved every year, but the standards and regulations aren’t keeping up,” he said. “General education is also a hurdle. Many hospitals are still skeptical of the benefits of additive manufacturing.”
Additive Manufacturing Automation
Additive manufacturing is integral in developing many implants in Stryker’s product portfolio. An early adopter of the technology, the company is seen as a leader in the space.
“Additive manufacturing allows us to push beyond conventional manufacturing techniques to address design complexity and achieve previously difficult or unmanufacturable geometries,” said David O’Gorman, Director of Advanced Operations at Stryker. “The design freedom allowed by the process enables Stryker to stay at the forefront of the industry.”
O’Gorman points to AMagine, Stryker’s proprietary approach to implant creation using additive manufacturing, as a method that is deftly expanding the company’s possibilities for innovative device designs and ushering in new ways to create products.
“The AMagine process allows us to tackle previously difficult or impossible design complexities and address unmet surgeon needs with unique material characteristics,” he said. “As we continue to push the boundaries, we are excited about what additive manufacturing can help us create.”
While several promising additive manufacturing advancements are on the horizon for Stryker, O’Gorman said the company is specifically setting its sights on automation and information technology.
“Cost reduction, quality, metallurgy and post-processing are where Stryker will continue to focus efforts,” he said. “We believe advancements can be made in machinery, software (machine and design), digital integration and a general education on additive manufacturing capabilities.”
In considering additive manufacturing in orthopedics as a whole, hundreds of companies are adopting this ever-evolving technology. Orthopedic companies are seeking to position themselves at the forefront of a movement aimed at unlocking implant breakthroughs that have been accomplished through significant investment and innovation. As the technology matures in orthopedics, companies will need to continue to evolve their implant designs and stay educated on the latest advancements.
PM
Patrick McGuire is a BONEZONE Contributor.