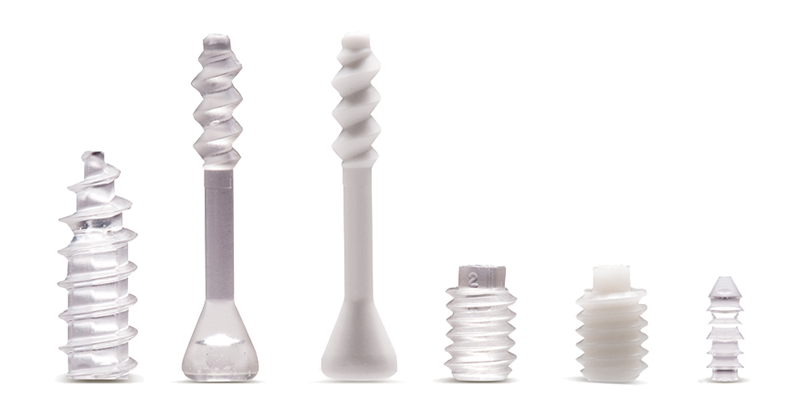
Bioresorbable polymers such as RESOMER® have been used for decades in sports medicine, orthopedic and surgical applications. The fact that they are bioresorbable is advantageous because a second surgical intervention is not needed to remove the device. These polymers are commonly used for fabrication of suture anchors and interference screws. However, over the past few years, 3D printing technologies have expanded the capabilities to produce other types of biodegradable implants, as illustrated in Figure 1.
There are four main 3D printing technologies in which RESOMER® can be used to fabricate 3D-printed implants:
- Plastic Freeforming uses polymer granules or pellets that are melted and transferred into droplets layer-by-layer on a moving building platform.
- Bioprinting can use different 3D printing techniques to combine cell and biomaterials to create a tissue-like structure.
- Fused Filament Fabrication (FFF) uses a continuous solid filament that is fed through an extruder head and deposited layer-by-layer on a platform.
- Selective Laser Sintering (SLS) uses a laser to sinter layers of powdered polymers.
In this article, we discuss how RESOMER® can be used for manufacturing 3D-printed implants.
What is Selective Laser Sintering? How is it Used in Medical Device?
Selective laser sintering is a printing process in which powder (in this case, polymer powder) is melted and sintered via a laser beam and printed layer by layer. SLS printing is the fastest printing method of the four listed above and is suitable for large-scale print volumes. SLS technology is also capable of printing objects with complex geometries, as it does not require any support structures to be printed with the final part (Figure 2).
Evonik has produced the world’s first bioresorbable powder for SLS printing of medical implants. The RESOMER® PrintPowder C 212 F is a ready-to-print material that is a free-flowing powder for high-resolution 3D printing. The particle size fits into narrow distribution and specifications. The material is fully biocompatible and made with medical grade polycaprolactone, which means that it is manufactured in ISO Class 8 clean rooms, ISO 13485 and GMP (Good Manufacturing Practice) quality systems. GMP-grade material for human implant use is currently available.
The Relationship Between Printability and Flowability
Free flowable powder is needed for SLS printing because powder with low flow can result in pores, agglomerates, uneven surfaces or further unwanted effects. On the other hand, powder with high flow can cause shifting due to a non-stable printing base. The optimum flowability results from having a narrow particle size and a specific temperature range that allows the material to flow at elevated temperatures (Figure 3).
Key Printing Parameters Needed to Successfully SLS Print a Medical Device
Successful printing of a medical device with the desired mechanical characteristics relies on effective use of multiple printing parameters. The key parameters that can be altered and used to impart energy into the powder surface are laser power, hatch distance and canning speed. Successful printing of a medical device with desired mechanical characteristics relies on the effective use of multiple printing parameters (Figure 4).
What are the Challenges with SLS Printing?
Typical challenges with SLS printing are shrinking, curling and shifting. In shrinking, the laser parameters are too high, and a melt pool is created, causing the material to shrink. With curling, the printing temperature is too low and the material crystallizes too quickly, causing the material to curl. Lastly, in shifting, the part shifts from its original position during recoating.
Consistency of the printing parameters is key to successful printing. Therefore, a powder with narrow specification is required. For example, printed parts from the same batch will perform differently if the porosity is not controlled. As shown in Figure 5, different porosity can be achieved by changing the scanning speed, hatch distance and laser powder.
Comparing SLS Printed Parts with Injection Molded Parts
SLS printing can produce parts with high compressive strength. When comparing SLS to injection molding, SLS 3D-printed parts typically have slightly lower mechanical properties than injection molding. However, the benefit of SLS printing is that complex shapes and multiple device designs can be rapidly produced and tested without expensive molds used in injection molding. Degradation times range from less than six months to a few years. Producing complex devices rapidly with consistent mechanical properties can be achieved with SLS.
Conclusion
In this article, we have described the benefits of using RESOMER® PrintPowder, the world’s first bioresorbable powder for SLS printing, to produce 3D-printed parts. RESOMER® PrintPowder is available as a standard product or customized powder. Different compositions, properties, particle sizes and additives are available made to order. For more information about how Evonik can provide medical device solutions, please contact us.
Dr. Thiago Borges is manager for customer projects at Evonik’s biomaterials center in Birmingham, Alabama. He has 13 years of experience in the medical device industry and is responsible for managing customer projects, providing technical application support and managing internal innovation projects for medical device solutions. Thiago joined Evonik in 2015 and was previously a project manager for RESOMER® Filament and other products, where he coordinated the development of technical grade and GMP grades for this product. Prior to Evonik, he worked for eight years in the medical device industry, holding different positions in R&D and operations, in particular working with stents and embolization devices. Thiago holds a bachelor’s degree in Chemistry from the University of Sao Paulo and a Ph.D. in Polymer Science & Engineering from Case Western Reserve University in the U.S.
Dr. Cécile Boudot studied mechanical engineering in a binational diploma program at Arts et Métiers ParisTech in France and Karlsruhe Institute of Technology in Germany. In the scope of her Ph.D. studies at the Institute of Medical and Polymer Engineering of the Technical University of Munich, she worked on the development of implantable catheter systems based on silicone elastomers. She continued her research activities at the Centre of Advanced Composite Materials, the University of Auckland in New Zealand, and worked on the processing of biodegradable polymeric stents based on polylactic acid blends. Cécile joined Evonik in 2017 and is responsible for the application technology for medical devices in the EMEA region. Cécile was project manager for scale-up and GMP integration of RESOMER® PrintPowder.