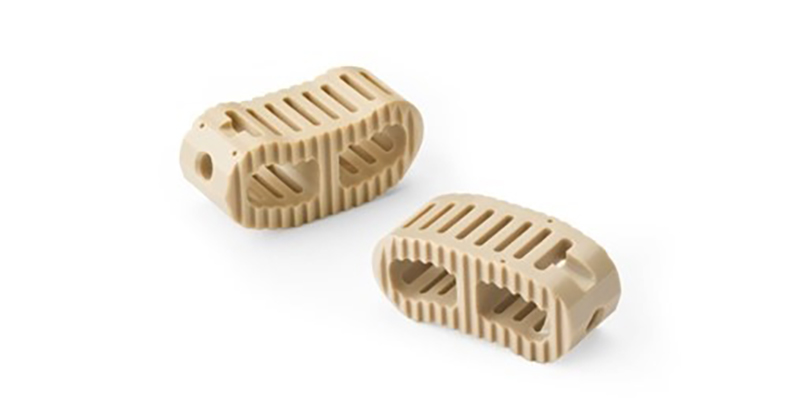
Near net shape (NNS) technology has emerged as a highly effective manufacturing method for the production of surgical orthopedic implants such as large joint orthopedics, knee and hip implants, spinal cages and suture anchors. NNS technology enables implantable parts to be produced into nearly-finished forms that are close in shape to the final product.
A major reason for developing the new technology was to reduce systems costs when machining finished components from expensive highly regulated implantable thermoplastic materials such as polyetheretherketone (PEEK), ultra high molecular weight polyethylene (UHMW-PE) and the emerging UHMW-PE/PEEK hybrid for implant designs for orthopedics.
NNS can reduce or even eliminate the need for surface finishing like machining or grinding and delivers bottom line benefits that can result in significant savings in production costs. NNS parts are compliant with ASTM F648 and ISO 5834-2 for ultra-high molecular weight polyethylene (UHMW-PE), and ASTM F2026 for PEEK for use in Class III Implants (>30 days). Both PEEK and UHMW-PE have an excellent history of clinical performance.
This unique manufacturing technology provides customers with productivity improvements and a simplified supply chain for the production of PEEK and UHMW-PE shapes. NNS is also an important tool in supporting sustainability programs by reducing the amount of required resin.
Cost and Sustainability Benefits for PEEK and UHMW-PE Implants
PEEK polymers have proven to be well-suited for use in surgical orthopedic implant applications. They are machined and formed into specific shapes, including the well-known osteotomy wedge system and “banana” wedge designs that are as effective as they are innovative. Complex components take time and tooling to machine precisely so that less material is removed, and shapes can be produced faster. Less machining means less material waste, which is an important consideration for meeting sustainability goals. NNS reduces machining time, lowers the part, reduces stress, and improves dimensional stability.
The reduction in machining also helps to compress the product development cycle. By using one of the various NNS technologies that are available, manufacturers can produce a component very close to the final form. Due to the complex profiles of NNS, special fixturing technology has been developed to compensate for the unique shape profile.
The following are examples of some of the NNS technology formats that are available.
- Direct compression molding
- Simple profile extrusion
- Complex cored or hollow components
- Proprietary molding technology
Some NNS technology can improve mechanical strength and can reduce material mass by 15% to 45% when PEEK hollow profiles are produced. During the molding process, a proprietary cooling technology independently manages the cooling rate and temperature through the cross-section which can greatly reduce stress. This enables a unique annealing process window for improved management of time, temperature and thermal change (cooling) rate, thus mitigating the potential for built-in stress in the product. Annealing greatly improves mechanical properties, dimensional stability, and warp/camber on the length of the extrusion. Depending on the application, melt rheology and annealing are managed to reduce stress, improve mechanical properties and dimensional stability, and reduce porosity.
For UHMW-PE implant applications, NNS direct compression molding makes a formed thermoplastic component while the Ram extrusion process is used to produce simple and complex profiles. Both are then formed into near net shapes. Ram extrusion converts UHMW-PE into various profiles which provide comparable material properties and performance, while utilizing different geometrical options that can improve overall cost by minimizing machining waste. These geometries are targeted for knee and hip applications as well as other smaller part geometries.
The unique technology provides a near net shape benefit with removal of 5% to 25% of the UHMW-PE in the raw material blank size. The complementary benefits are a reduction in machining time, tool wear, material chip generation and the disposal costs associated with the waste material that previously required removal. Ram extrusion provides all of these benefits while still maintaining the critical material performance properties.
The Ram extrusion process has also evolved beyond round rods to produce complex profiles that are nearer in shape to the final component, delivering improvements in both value and waste reduction. New geometries include shapes such as a modified kidney bean profile that correlates as a near net to tibial implant shapes or a butterfly profile for use in knee trials.
Conclusion
As manufacturers focus on reducing their carbon footprint, NNS delivers real cost and operational benefits for medical device manufacturers and customers, and reduces the environmental impact as a whole. This technology will continue to meet the growing demands of medical implant manufacturers who seek production efficiencies that reduce cost and improve part performance and design flexibility.
Mitsubishi Chemical Advanced Materials’ (MCAM) MediTECH® Implantable Polymers division manufacturers PEEK and UHMW-PE thermoplastic shapes. The MediTECH division partners with implant manufacturers to supply the prototyping, testing, validation and product support in order to meet the expanding needs of the medical device industry. For more information, please visit www.mcam.com.
Eric Tech is the Strategic Growth Manager Healthcare for Mitsubishi Chemical Advanced Materials Inc.