-
Lincotek Medical
3110 Stage Post Dr, Ste. 101-107
Bartlett, Tennessee
38133
United States - 11 Facilities
- 901-590-4240
- 900+ employees
- Founded in 1992
- Operating in Asia, Europe, Global, North America
- Visit Website
Changes saved
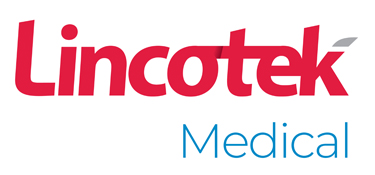
- Additive Manufacturing
- Instruments
- Logistics/Supply Chain
- Manufacturing
- Materials/Bio and Performance
- Materials/Metals
- Packaging
- Product Development
- Regulatory/Quality Assurance
- Surface Preparation/Treatments
- Testing
Lincotek Medical provides contract, full-service medical device development and manufacturing for spine, reconstruction, sports medicine & trauma, and extremities markets. With a focus on innovation and market speed, we partner with OEM customers to deliver products that enhance quality of life and standard of care for patients. It is the only company of its kind with the ability to guide our partners through every step of the device development process – from ideation to high-volume production.
Our disruptive renewed strategy allows us to provide true “Concept to Launch” support to OEM customers. We are able to assist our customers during all stages of their manufacturing journey, from device conception and manufacturing through to finishing and polishing, and eventual packaging, simplifying the supply chain, and shortening the overall lead time.
With decades of experience and a continuous strengthening of our development engineering and manufacturing expertise, we provide a unique and comprehensive portfolio of services for the medical OEM journey.
Integrated Supply Chain Solutions
Our disruptive renewed strategy allows us to provide true “Concept to Launch” support to OEM customers. We are able to assist our customers during all stages of their manufacturing journey, from device conception and manufacturing through to finishing and polishing, and eventual packaging, simplifying the supply chain, and shortening the overall lead time.
With decades of experience and a continuous strengthening of our development engineering and manufacturing expertise, we provide a unique and comprehensive portfolio of services for the medical OEM journey.
From first concept to creating the final technical file, our research and development and regulatory teams have more than extensive experience in developing orthopedic instruments, orthopedic implants, and dental implants, and are ready to support you throughout the design process.
Design
From first concept to creating the final technical file, our research and development and regulatory teams have more than extensive experience in developing orthopedic instruments, orthopedic implants, and dental implants, and are ready to support you throughout the design process.
We are known for our rapid and precise prototyping capabilities – this market critical step is vital to getting innovations to market quicker. Our Co-Innovation® process is a market-leading offering where we partner with not only OEM customers to bring products to market, but also key opinion leader (KOL) surgeons who have an innovative and disruptive product that requires the technical know-how to take it to market.
Prototyping
We are known for our rapid and precise prototyping capabilities – this market critical step is vital to getting innovations to market quicker. Our Co-Innovation® process is a market-leading offering where we partner with not only OEM customers to bring products to market, but also key opinion leader (KOL) surgeons who have an innovative and disruptive product that requires the technical know-how to take it to market.
We have championed innovation in additive manufacturing solutions since 2006. We produced over 100,000 parts per year with best-in-class yield rates, material consumption and per-unit costs, enabling true Additive Serial Production with our Additive Plus offer. When you have 3D-printed the part, you need to be able to complete it: post-processing of AM parts is fundamental and truly challenging.
Our unique portfolio of special processes allows us to combine additive and conventional manufacturing, and offer a complete value chain. What sets us apart is the integration between the different processes that are already part of the design and development phase.
Additive Manufacturing
We have championed innovation in additive manufacturing solutions since 2006. We produced over 100,000 parts per year with best-in-class yield rates, material consumption and per-unit costs, enabling true Additive Serial Production with our Additive Plus offer. When you have 3D-printed the part, you need to be able to complete it: post-processing of AM parts is fundamental and truly challenging.
Our unique portfolio of special processes allows us to combine additive and conventional manufacturing, and offer a complete value chain. What sets us apart is the integration between the different processes that are already part of the design and development phase.
Our new, fully robotized facility is completely dedicated to orthopedic applications and carries an ISO 1345 certification. It also has its own ISO 17025 certified internal lab. The forging we offer is unique in its level of automation throughout the manufacturing process – meaning we can guarantee state-of-the-art product quality, total process control and repeatability.
Forging
Our new, fully robotized facility is completely dedicated to orthopedic applications and carries an ISO 1345 certification. It also has its own ISO 17025 certified internal lab. The forging we offer is unique in its level of automation throughout the manufacturing process – meaning we can guarantee state-of-the-art product quality, total process control and repeatability.
Our superior metallurgical experience paired with a passionate and dedicated workforce brings our customers’ vision to market through scale manufacturing. Our centrifugal and static casting and broad knowledge of key medical-grade alloys allow us to produce implantable medical devices and medical instruments of any configuration and ensure the highest quality end product.
Casting
Our superior metallurgical experience paired with a passionate and dedicated workforce brings our customers’ vision to market through scale manufacturing. Our centrifugal and static casting and broad knowledge of key medical-grade alloys allow us to produce implantable medical devices and medical instruments of any configuration and ensure the highest quality end product.
We combine years of machining craftsmanship along with the newest technology to machine implants and medical instruments. We offer swiss-turning, 3-5 axis milling, lathing, turning and grinding solutions to make your ideas become products. We can manage all the supply chain steps for manufacturing hip, knee, shoulder, fixation, trauma, spine, and dental components to give you a complete one-stop-shop solution.
Machining
We combine years of machining craftsmanship along with the newest technology to machine implants and medical instruments. We offer swiss-turning, 3-5 axis milling, lathing, turning and grinding solutions to make your ideas become products. We can manage all the supply chain steps for manufacturing hip, knee, shoulder, fixation, trauma, spine, and dental components to give you a complete one-stop-shop solution.
Using the latest robotic technology, we have completely automated processes for finishing and polishing hip, knee, shoulder and other orthopedic implants.
Finishing and Polishing
Using the latest robotic technology, we have completely automated processes for finishing and polishing hip, knee, shoulder and other orthopedic implants.
We offer a range of coating solutions, including plasma spray coatings, calcium phosphate coatings, and physical vapor deposition (PVD) coatings.
Coating Solutions
We offer a range of coating solutions, including plasma spray coatings, calcium phosphate coatings, and physical vapor deposition (PVD) coatings.
Our electrochemical treatments include titanium anodization and chrome coating. We offer different types of titanium anodization, such as that used to enhance mechanical performance or that used to color the individual parts. Our chrome coating process enables a low-friction surface to be created that improves the service life, performance, and cosmetic appearance of a medical device.
Electrochemical treatments
Our electrochemical treatments include titanium anodization and chrome coating. We offer different types of titanium anodization, such as that used to enhance mechanical performance or that used to color the individual parts. Our chrome coating process enables a low-friction surface to be created that improves the service life, performance, and cosmetic appearance of a medical device.
We take great care in ensuring that our customers’ products are packaged according to applicable industry standards. Our clean rooms are classified ISO 5 and ISO 7.
Cleaning and Packaging
We take great care in ensuring that our customers’ products are packaged according to applicable industry standards. Our clean rooms are classified ISO 5 and ISO 7.
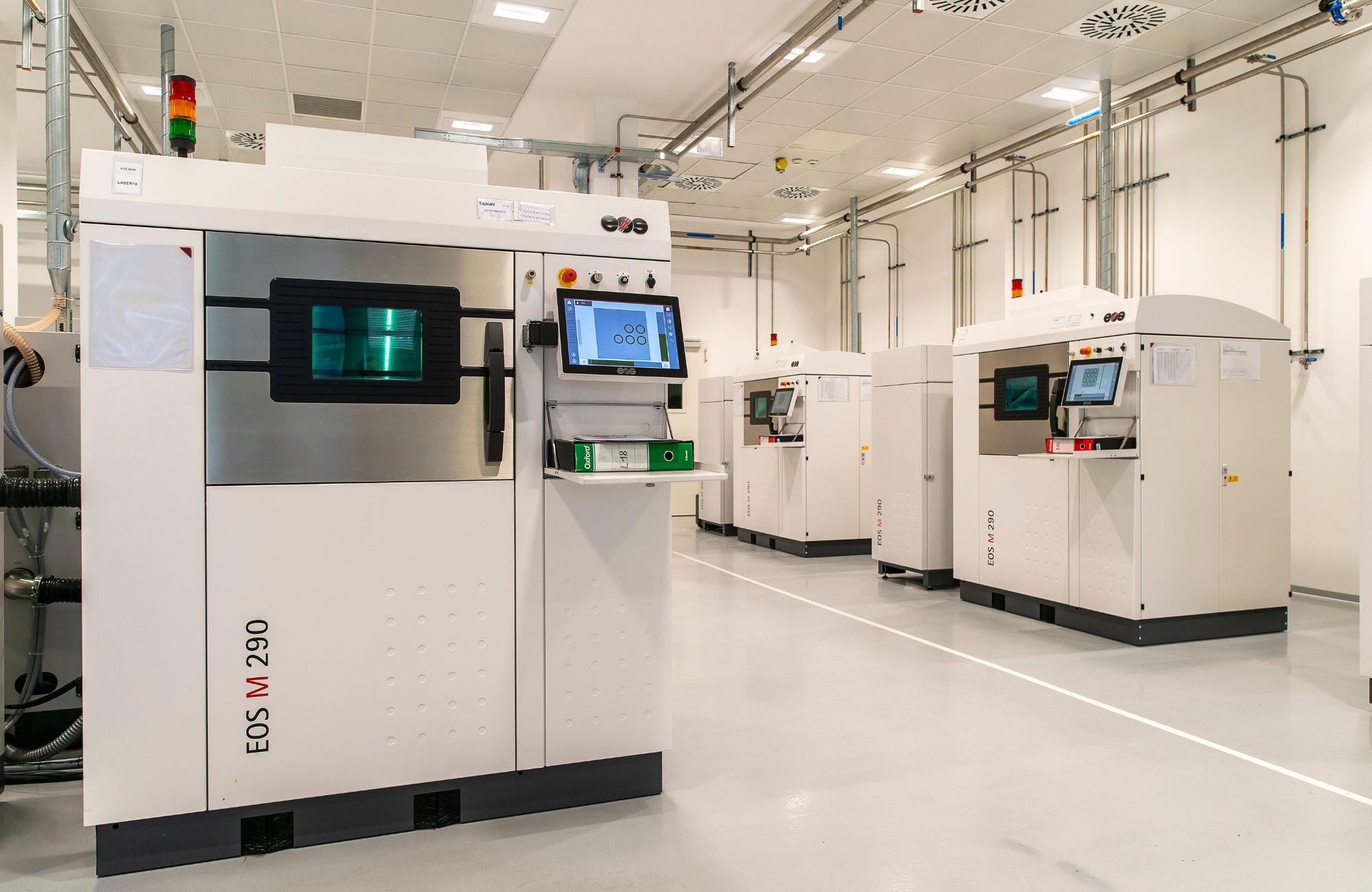
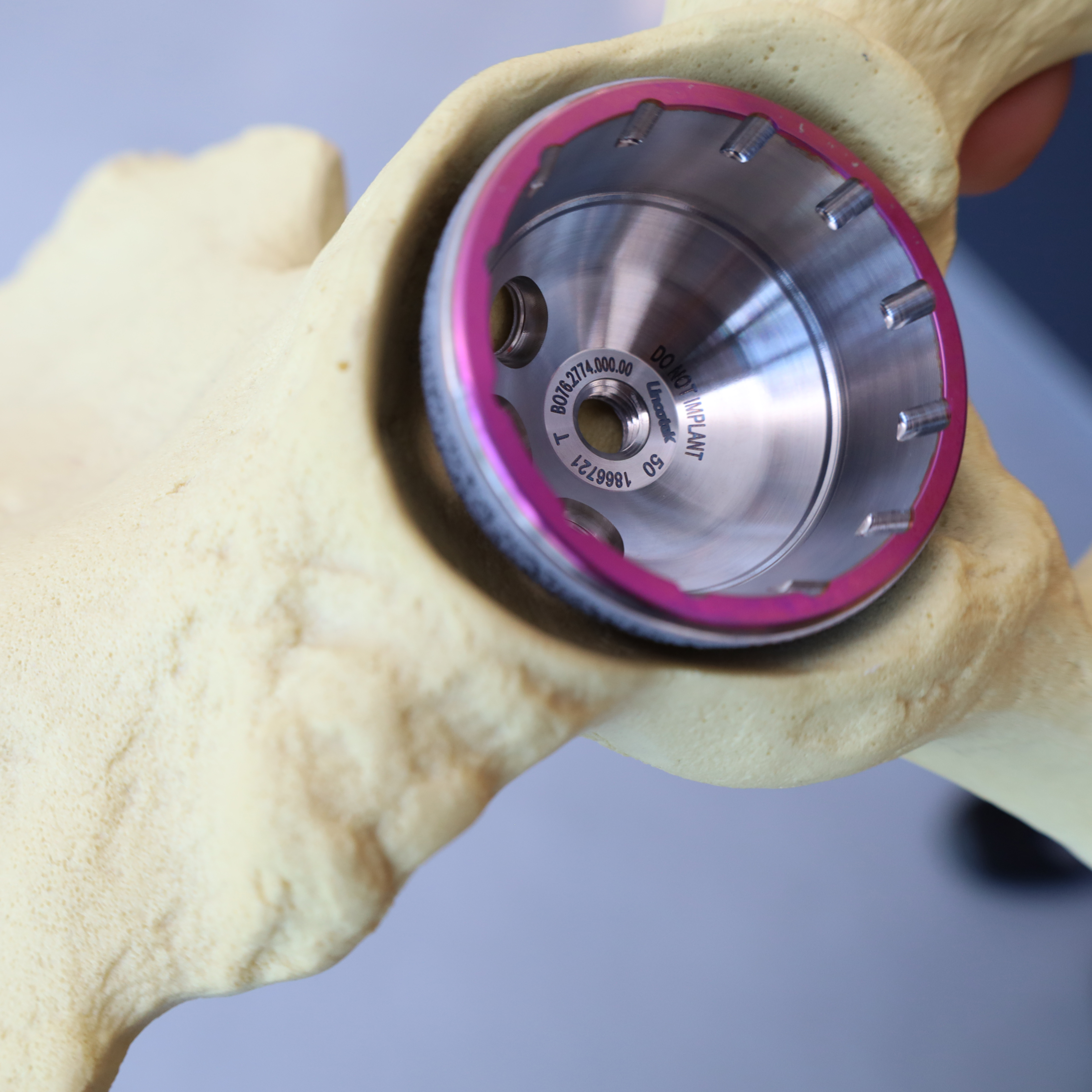
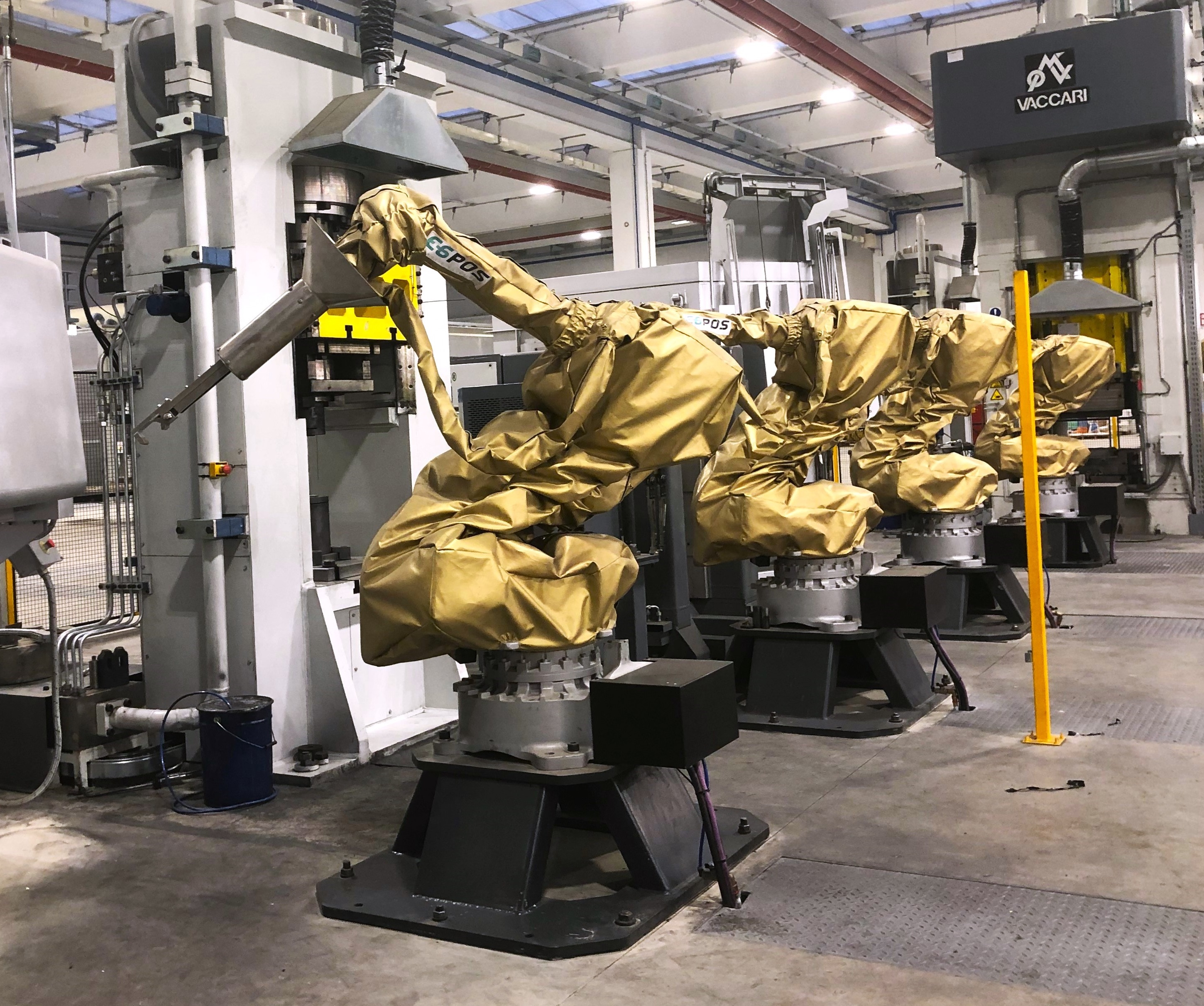
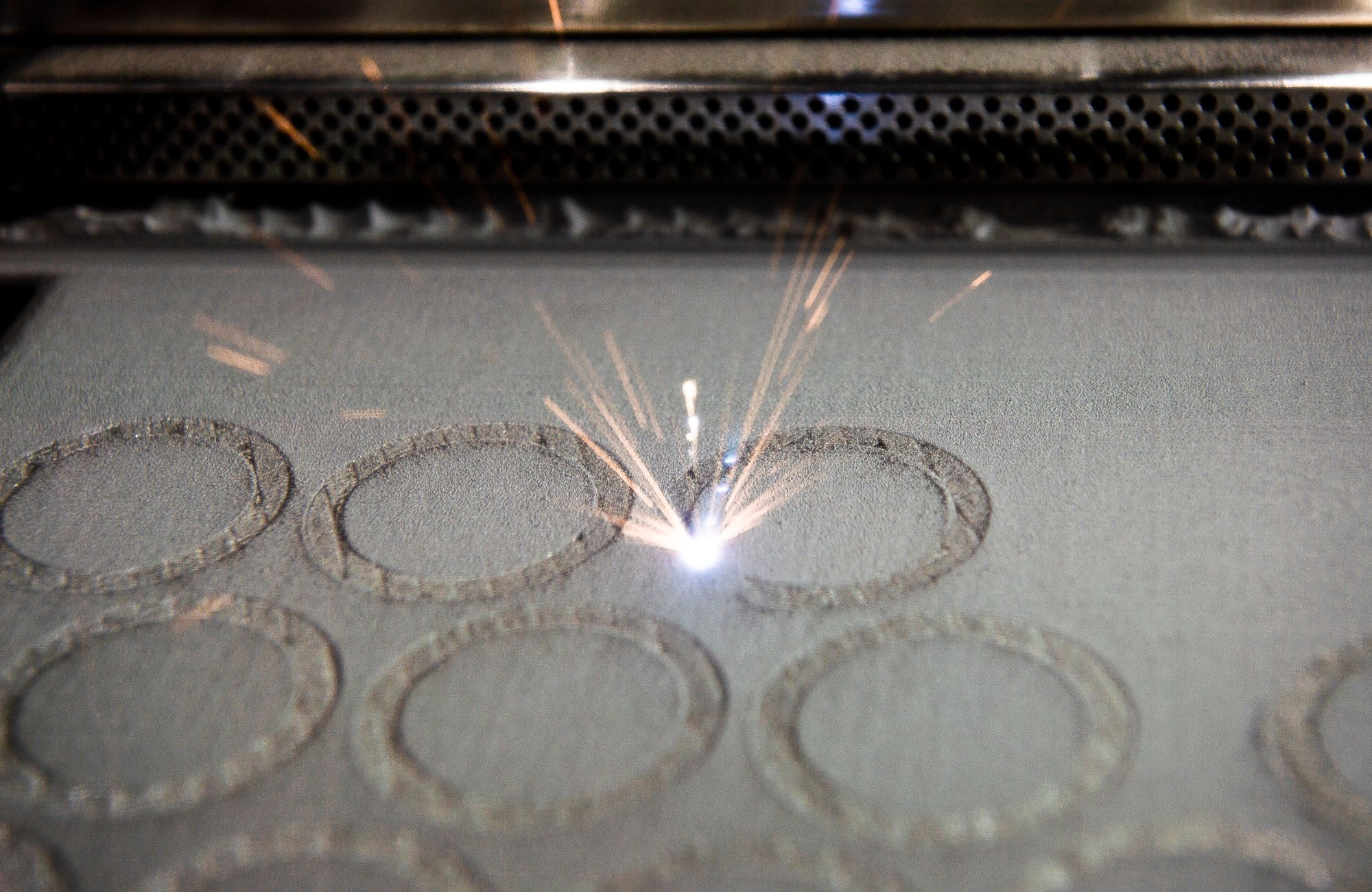
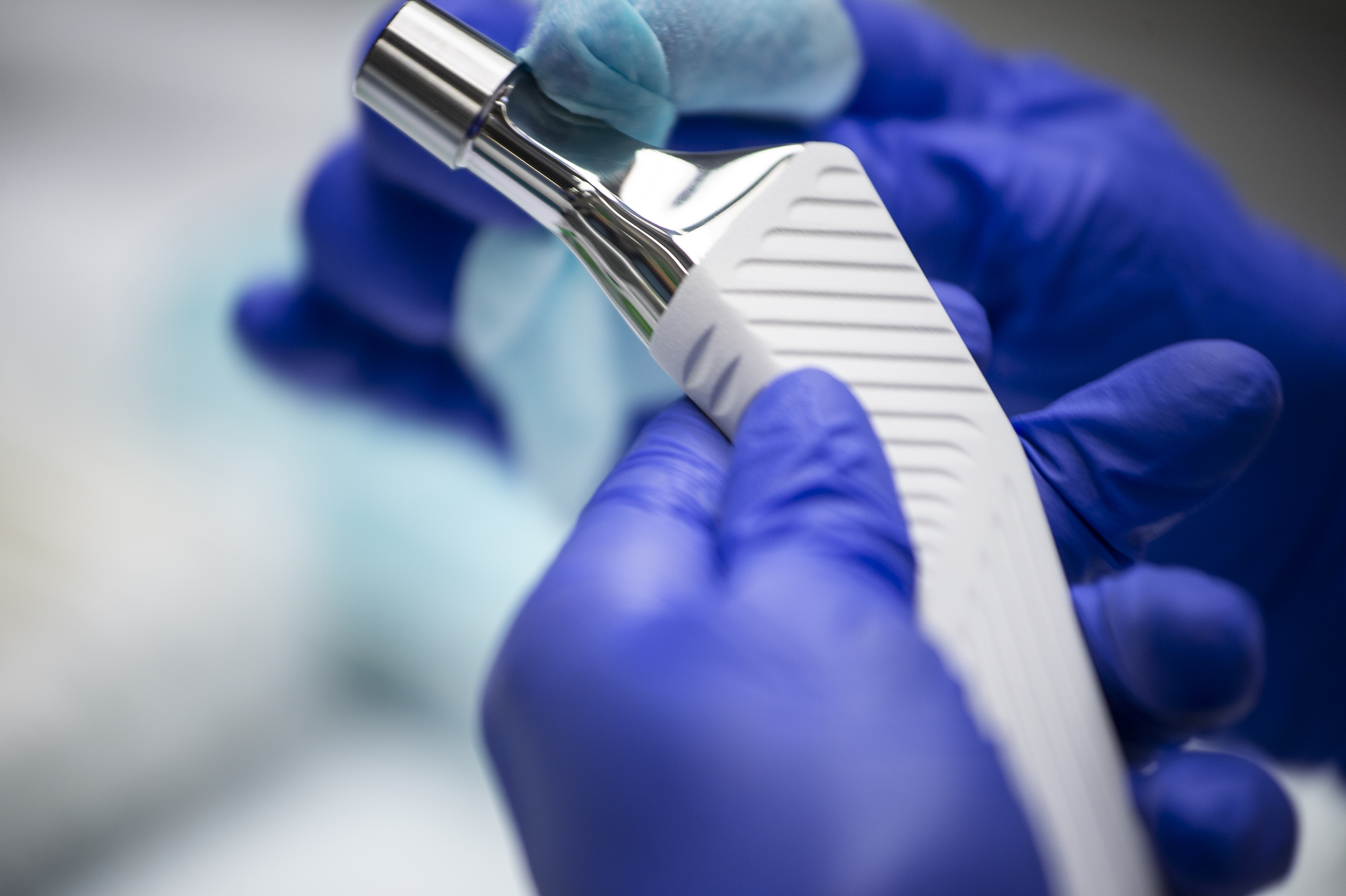
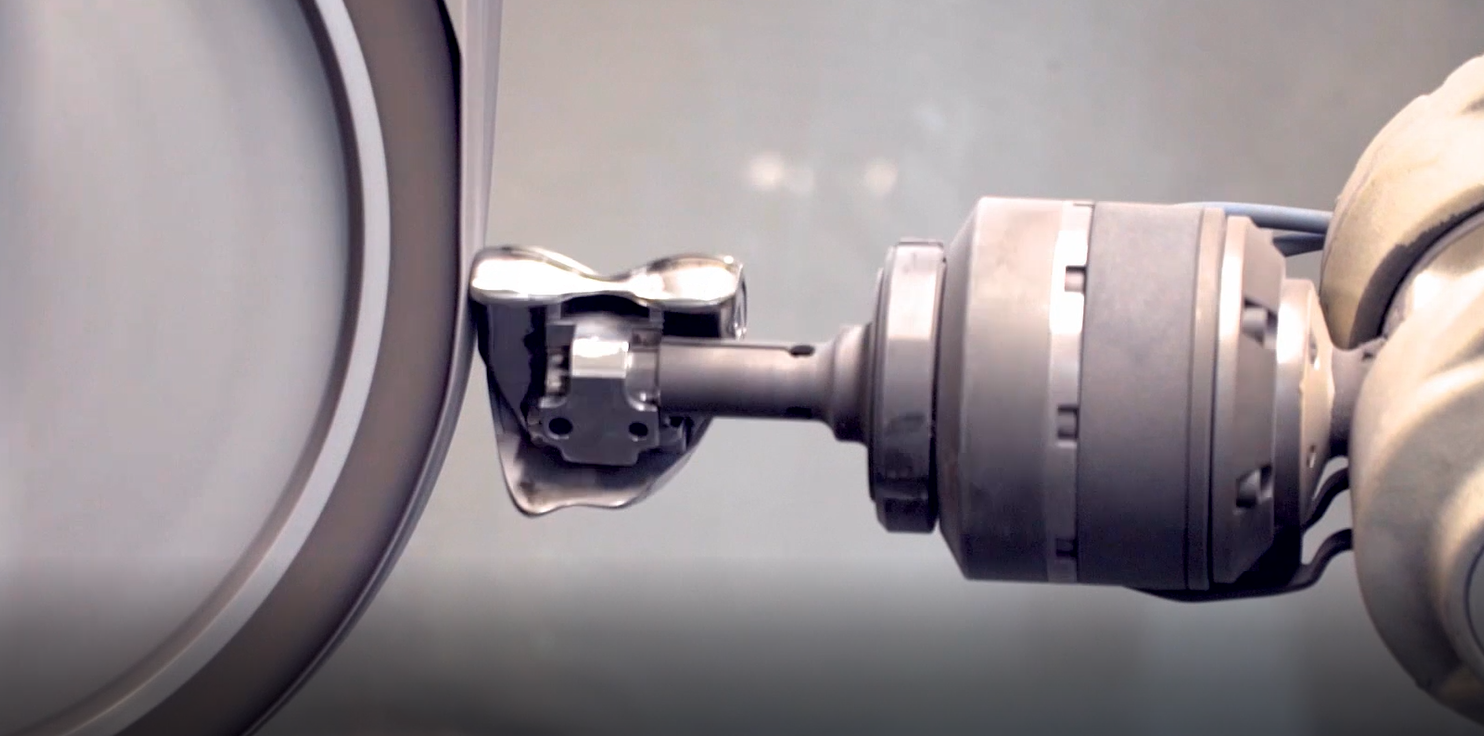
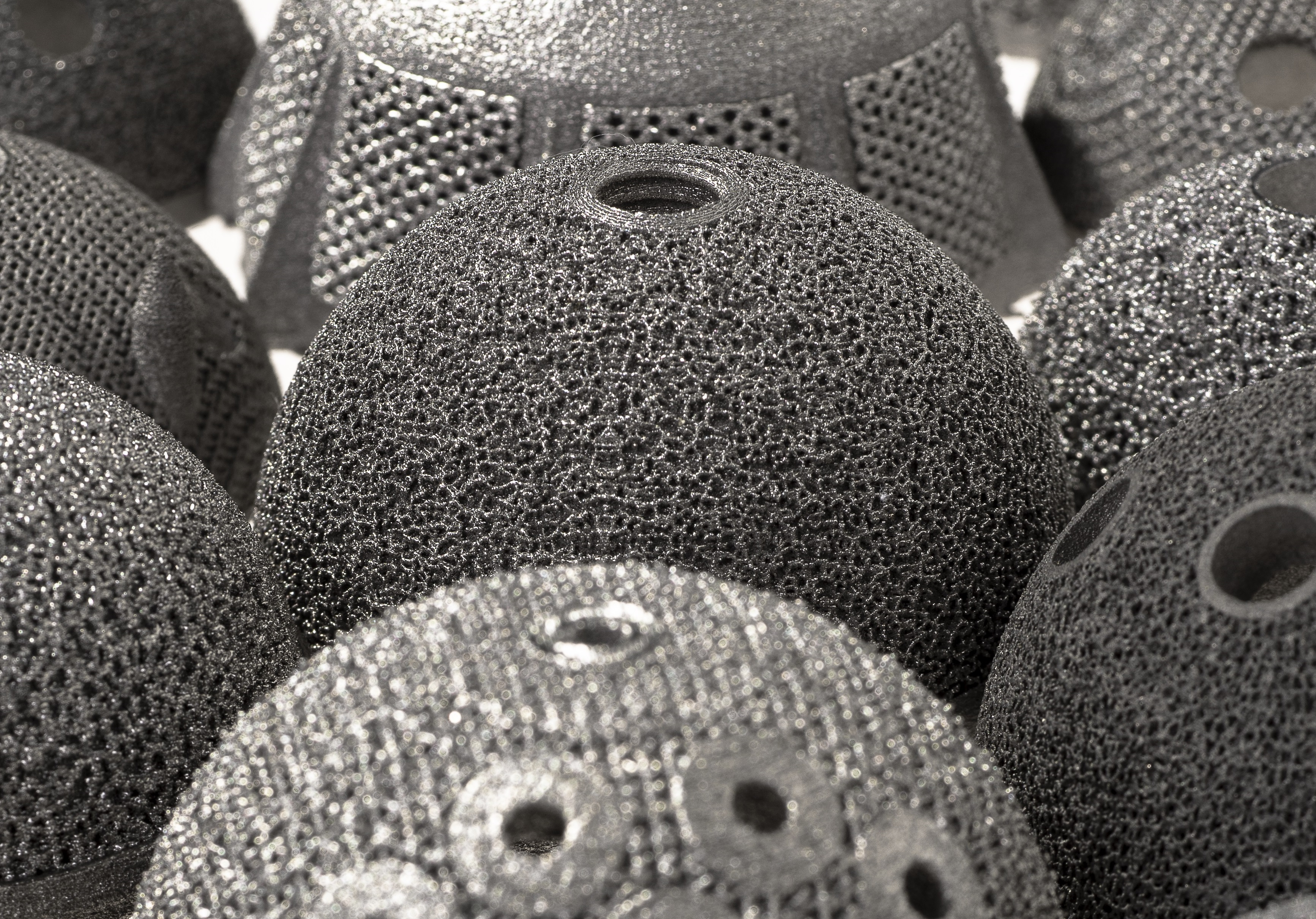
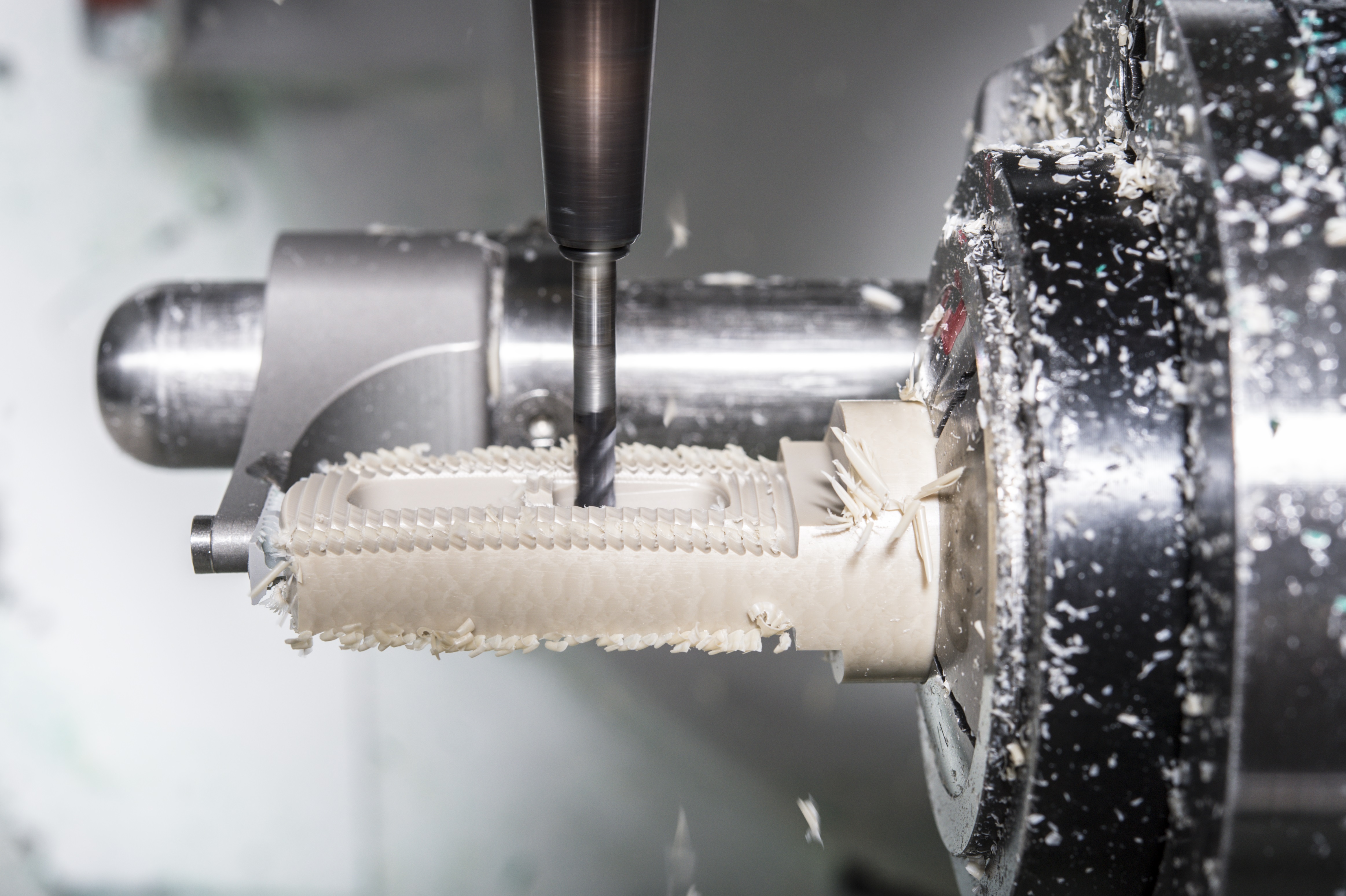
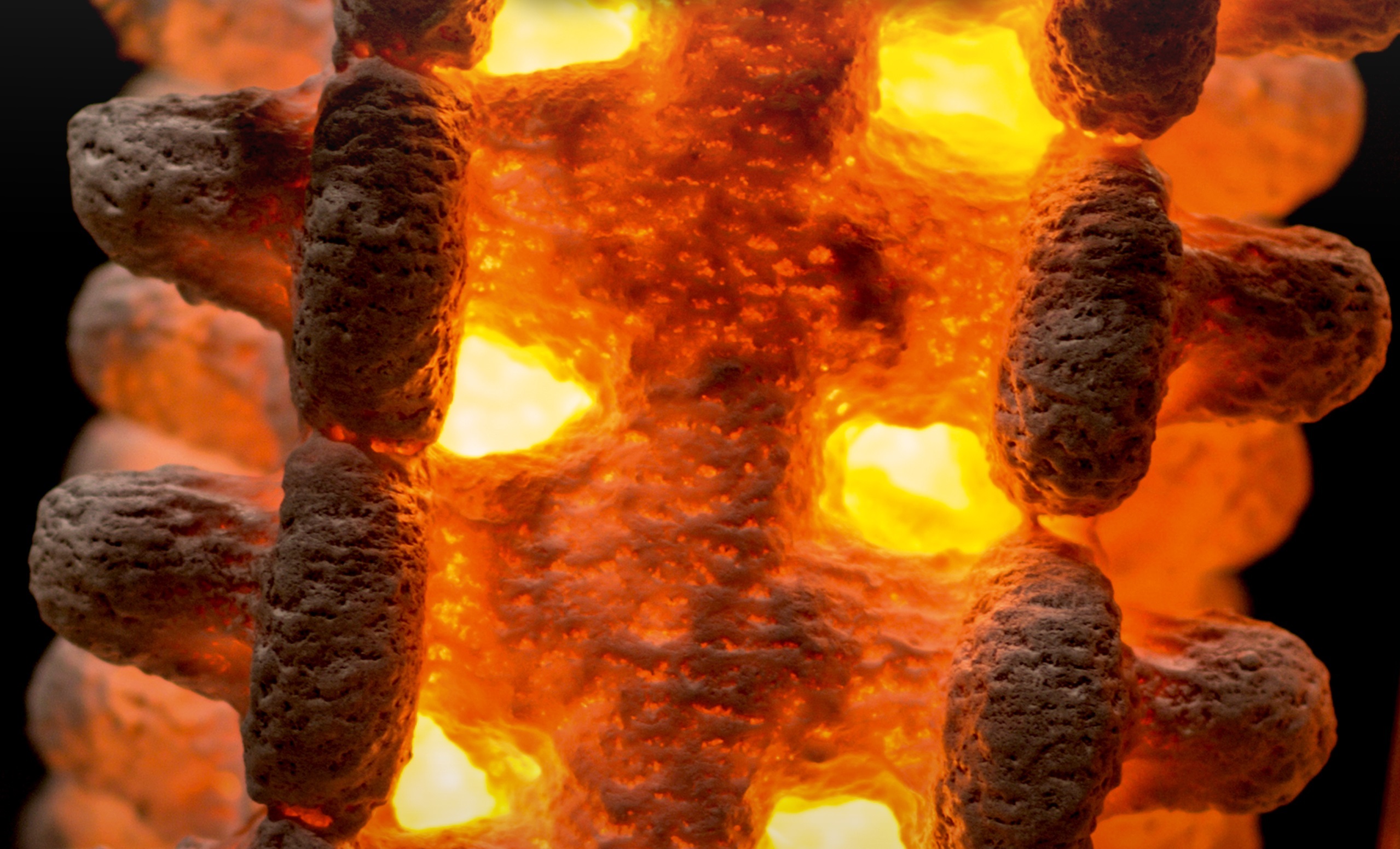
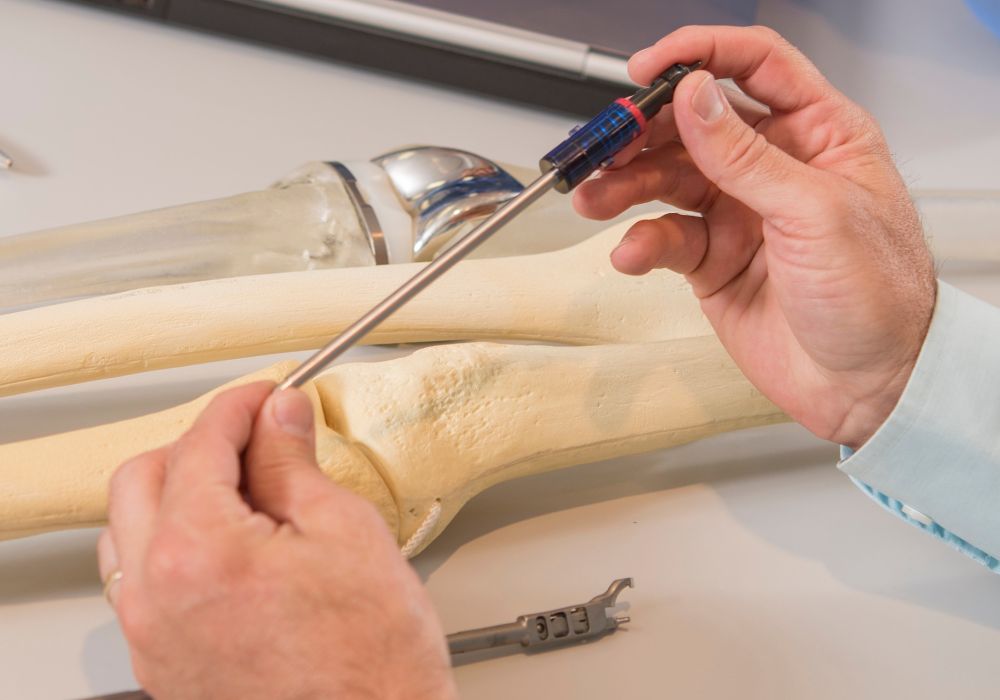
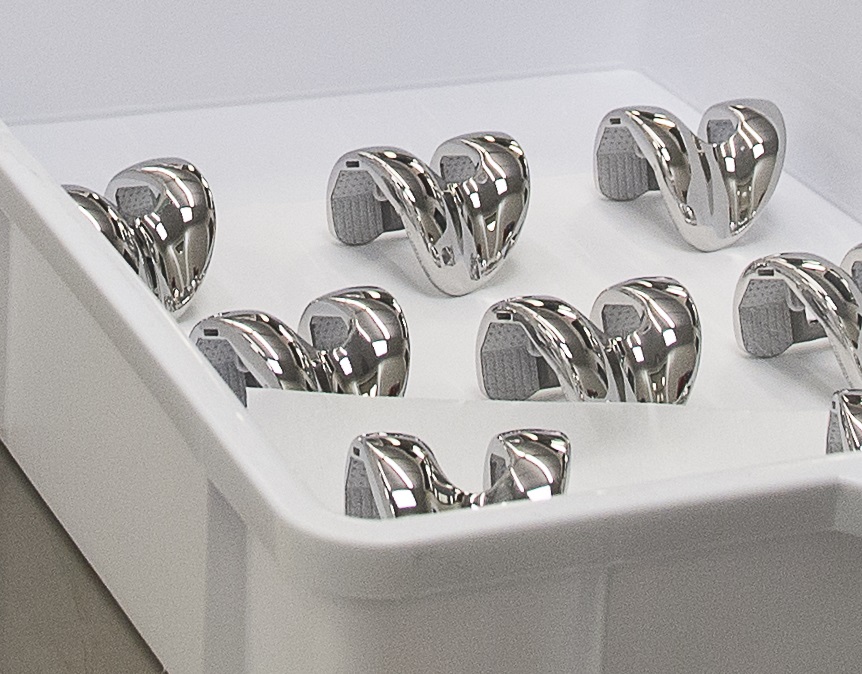
Ste. 101-107 Bartlett
Memphis, TN
United States
Molalla – Portland, OR
United States
Vandalia - Dayton, OH
United States
Providence, UT
United States
2450 Deelyn Drive
Warsaw, IN 46580
United States
Via Al Dos de la Roda, 60, 38057
Pergine Valsugana, Trento
Italy
40057 Cadriano di Granarolo
Emilia, Bologna
Italy
Lotto D 29 – Area P.I.P.
Eboli, Salerno
Italy
Via Polo dello Stampaggio a caldo 8, 10080
Busano, Torino
Italy
#30 Wanquan
Wuxi, Yunnan / 云南
China
16 Tianshan Road, Xinbei District,
Changzhou, Jiangsu / 江苏 PRC 213022
China