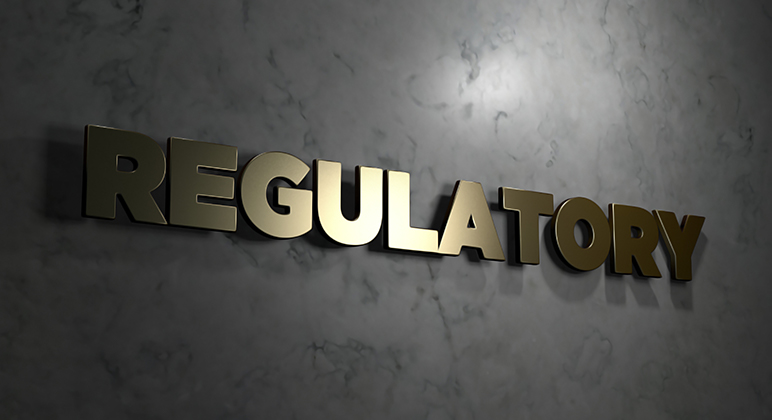
Ask the Experts is a series of reader questions answered by industry advisors. Send us your questions.
Question: How deep should we go with our process validation? What is the current industry thinking on this topic?
Answer from Carolyn Guthrie, Director of Regulatory Affairs and Quality Assurance, Kapstone Medical: Another way of asking this question using typical quality system language is to ask how to determine the scope of the validation.
While it really depends on the specific process that your company is validating, various processes like sterilization validation or packaging validations are well described in specific standards. However, if we are considering only manufacturing environments, such as a machine on the production floor and how it needs to be validated, there are some basic activities that make up a process validation. You need to ensure that your equipment is qualified, and then you need to demonstrate that your process can perform reproducibly and repeatably on the equipment. There are three steps to qualify your equipment: Installation Qualification (IQ), Operational Qualification (OQ) and Performance Qualification (PQ).
Usually in an IQ, you are simply setting up the equipment so there isn’t much of a scope differentiator. The equipment manufacturer can help you determine what you need and what to look for in an installation qualification for specific pieces of equipment.
In an OQ, however, you can develop more of a scope. You want to determine if the equipment you are using is capable of performing what it claims it can perform. If you are only using certain parts of the equipment, you can focus on these functions. In the OQ, you want to challenge your equipment and/or process. Also during the OQ, one can optimize process conditions.
In a PQ, you start to cross over into the process validation world. Most of the time, you will perform a PQ and a process validation at the same time. You are trying to demonstrate that the process you are testing is capable of meeting your specific intended use; in other words, in routine manufacturing conditions.
A way to help determine the scope of the validation is to make sure that you thoroughly understand how the process affects critical quality attributes (CQAs) of the device. You need to evaluate your product and ask yourself, what are the most important parts and functionalities of the product to ensure its successful performance, and continued safety? Here are ways to help determine the scope.
- Determine your critical quality attributes for your product (this may require input from the design and development team)
- Assess the process and determine critical process parameters (CPPs; directly affect CQAs) and less critical parameters
- Focus your efforts on controlling the CPPs of the process to be validated (scope narrowing opportunity)
- Use risk of the device and process to determine sampling requirements (scope narrowing opportunity)
I am a firm believer in risk management, whether it’s in the design of the device itself or the design of the process. By creating a strong flow chart of a process, identifying inputs into that process including risk, whether it be human, materials or any other part of the process, one should be able to explain how a company is balancing validation requirements and mitigation of risk to patients.
Ms. Guthrie is originally from South Africa, where she earned her Master’s Degree in Cellular Biology and earned a graduate certificate in business. She came to the United States in 2003 and has since worked primarily in the areas of regulatory and quality management in the medical device field, and earned her Master’s in Regulatory Affairs. She lives in Charlotte, North Carolina.