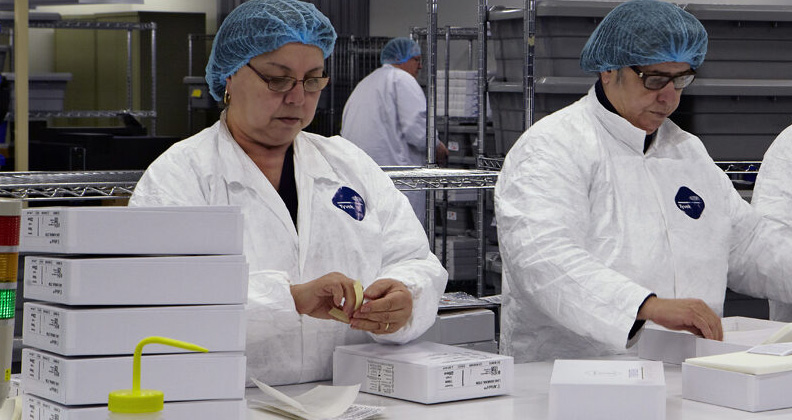
Today’s orthopedic devices are housed in more than simple trays and packs. Packaging systems must maintain a device’s functionality and sterility from shipping through to surgery as regulatory requirements increase sterilization challenges and interest in sustainable designs ramps up.
Advanced simulations, innovative design solutions and waste-reducing concepts are transforming packaging systems that play a key role in the delivery of orthopedic care. Let’s look at four ways that orthopedic manufacturers can work with proven experts to ensure devices are delivered efficiently, safely and reliably.
- Streamlined Workflows
One of the most significant inefficiencies in current packaging and sterilization workflows is managing the “edge case” sizes for implantable devices, according to Tom Williams, General Manager at Millstone Medical Outsourcing.
“While there is consistent demand for core sizes in knee, hip and spinal implants, the less commonly used sizes — those on the outer edges of the bell curve — can disrupt operational efficiency,” he said. “Processing these low-volume items a few times a year creates bottlenecks and slows overall production.”
Williams noted that inefficiencies also stem from supply chain fragmentation. “When packaging and sterilization partners operate without a centralized Tier 1 approach, products are shipped to multiple locations for inspections, testing and sterilization,” he said. “Each handoff introduces potential delays and logistical complexities.”
Millstone addresses these issues by offering centralized logistics and Tier 1 solutions, reducing redundant product movements, which limits inspection delays and excess transportation costs.
- Mining the Data
Williams said recent advancements in sterility testing methodologies have focused on improving predictability and real-time insights during the transport and storage phases. For instance, he said Millstone is exploring the use of environmental sensors and data loggers that track conditions like temperature, humidity and shock exposure.
“These sensors provide immediate feedback if conditions fall outside the acceptable range, allowing for proactive intervention,” Williams explained.
The collection of better process data also enables the parametric release of products after sterilization. “Parametric release relies on in-process data rather than traditional sterility tests, offering faster turnaround times,” Williams said. “This approach not only ensures product integrity but also accelerates time to market.”
Williams points to the importance of reducing unnecessary validations. “By relying on pre-validated materials and utilizing shared validation data, we help clients avoid redundant testing, minimizing waste and costs,” he said. “These initiatives align with OEMs’ broader goals to reduce waste while maintaining high product integrity and sterility.”
Data analytics plays an increasingly vital role in improving packaging and sterilization methods. Packaging and cleaning systems can now interface with external data collection systems to provide detailed process insights.
“This data is no longer just a historical record,” Williams said. “It serves as an early warning system to detect shifts in the process that may impact quality or safety.”
Millstone uses sterilization data to reduce downtime after a source reload and analyzes cycle data to identify trends that signal potential delays or inefficiencies.
“These insights enable proactive adjustments and minimize downtime,” Williams said. “As mentioned, advanced process data also supports parametric release protocols, allowing for faster product release without waiting for traditional sterility testing. Real-time process data ultimately allows us to maintain quality control and consistency.”
- Trusting the Experts
Effective collaboration among engineers, regulatory specialists and operations teams is essential for improving packaging and sterilization workflows. Willams said fostering cross-functional cooperation involves establishing shared long-term strategies, particularly around emerging sterilization modalities like X-ray amid the push to reduce ethylene oxide (EO) usage.
“When all teams are aligned on strategic goals, they make faster, more unified decisions about implementation,” Williams said.
Like most packaging design professionals, Sean Egan, Director of Global Marketing at Nelipak Healthcare Packaging, emphasized the importance of being involved in product development cycles during the initial phases. “When we have the time to collaborate, the results can be incredibly successful,” he said.
Egan shared one notable example involving a customer that was among the first companies to prioritize sustainable packaging designs and wanted to reduce the overall size and weight of their system. They were committed to using EO sterilization, but their new packaging design featured fewer empty spaces in order to reduce its size. The changes raised concerns about how the EO gas would flow into and out of the packaging during the sterilization process.
Nelipak’s team worked closely with the company to develop a solution. “We designed a surface on the device’s tray and lid that created enough space for the EO gas to flow efficiently,” Egan said. “This allowed the company to reduce the size of their packaging without compromising the sterilization process.”
That’s not all. Further testing identified an issue during the preconditioning phase of EO sterilization, during which heat and steam encouraged organism growth but caused some of the device’s components to lose their shape. To address the problem, Nelipak designed the tray to hold the components firmly in place during sterilization. This ensured the components retained their intended shape once the system cooled.
These innovations allowed the customer to significantly reduce their packaging footprint and earned Nelipak several awards for the design’s environmental impact.
Egan said his company is proactive in determining which sterilization modality is best suited for the devices that OEM clients present for packaging. It’s a way to become experts in the field and anticipate potential limitations before they arise.
“We often collaborate with sterilization providers to test how various materials behave under different processes,” Egan said. “Through this testing, we discovered that one sterilization method was incompatible with cellulose. This insight didn’t come from a customer request to use a specific sterilization method. It was something we uncovered during our evaluation.”
- Capitalizing on Simulation
Packaging waste reduction is a key priority for Millstone’s OEM clients, and the company meets those needs by conducting finite element analysis (FEA) to model packaging designs before production.
“By digitally simulating product stresses, we create stronger, more efficient packaging that uses fewer materials,” Williams said. “This approach allows for precise design adjustments before physical production and reduces waste and excess material costs.”
Another waste-reduction strategy involves developing universal packaging solutions that fit a variety of products. “We can validate one packaging configuration that works across multiple devices, eliminating the need for various validations,” Williams said. “It enables faster onboarding for new products and reduces material waste.”
Nelipak has advanced in silico computer simulations by achieving a high correlation between physical packaging test results and simulation data, enabling the company to engage in early-stage discussions with OEM customers about packaging design and potential down-gauging.
The simulations help to determine the amount of material that can be reduced while maintaining the packaging system’s performance, and the data allow Nelipak to determine how well packaging will perform in a drop test environment. Nelipak can also analyze the weight of virtual product models to predict whether design factors might cause issues like lid breaches, tray popping or other packaging failures.
“Using ASTM and ISTA standards, we can simulate drop tests and determine whether the package would pass,” Egan said. “Even better, we can visually demonstrate these simulations to our clients. We’re able to show that our testing technologies can help maintain package integrity and ensure that the sterile barrier remains intact throughout sterilization and handling.”
That’s no small accomplishment. One of Nelipak’s customers shared that a failed physical validation test could cost $80,000 to resolve, and result in five lost months of product development progress.
Nelipak is looking to explore ways to simulate accelerated aging at one, three and five years. “It’s an exciting direction for us,” Egan said. “This capability could significantly enhance what’s possible in testing the integrity of packaging and storage over time.”
DC
Dan Cook is a Senior Editor at ORTHOWORLD. He develops content focused on important industry trends, top thought leaders and innovative technologies.