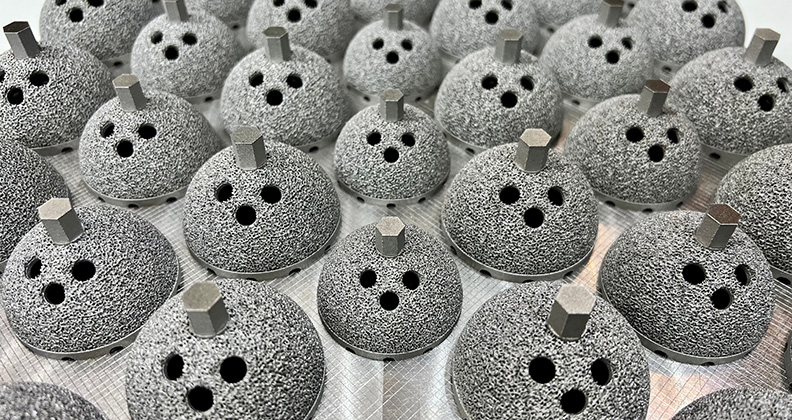
Securing FDA 510(k) clearance for orthopedic implants built from subtractive manufacturing can be a challenge. Adding additive manufacturing to the application process increases the level of difficulty and demands information that’s not needed for machined devices.
“The layer-by-layer building and melting of materials in 3D printing raise concerns about potential changes to material properties,” said Jeff Brittan, Vice President of Product Realization at SpiTrex Orthopedics.
Brittan has managed FDA 510(k) submissions for about two decades and over the last six years his role at SpiTrex Orthopedics has centered on the design, regulations and contracting manufacturing of 3D-printed devices. His exposure to various FDA review panels has given him insights into the agency’s expectations and allowed SpiTrex to streamline the clearance process.
“We’ve submitted several FDA master files detailing our additive manufacturing methods, which has helped us understand and respond to FDA requirements more effectively,” Brittan said.
The advantage of 3D printing lies in creating complex features, such as lattice patterns. Ensuring that they are reliably reproduced is crucial. Brittan said baseline references like ASTM standards (F3001 for titanium powder bed fusion, for example) and FDA guidance released in 2017, provide a good starting point for understanding FDA’s expectations.
However, he noted, FDA’s interpretations of these documents have evolved, and the agency hasn’t effectively communicated the changes to product developers.
“The ASTM document initially provided strength numbers for 3D prints,” Brittan said. “We used these numbers successfully until FDA, through further learning, decided that they should be product-specific rather than general baselines. This change wasn’t proactively shared with manufacturers, creating a challenge for sponsors to stay informed about new requirements.”
This lack of clear communication becomes apparent after sponsors submit 510(k) applications and start receiving questions about their products, making it difficult to anticipate what they need to address to gain clearance from FDA.
Brittan recently shared his experience with securing clearances for 3D-printed devices to eliminate much of the confusion about the process for orthopedic manufacturers and help them make it more efficient.
Key Considerations
Process control and validation are crucial factors in achieving additive manufacturing clearances. Brittan said FDA is concerned with how 3D printing impacts the geometry, dimensions, material characteristics and mechanical properties of a device and wants to know how input parameters and build location variability impact the final design.
FDA is interested in understanding variability within the printing system in single builds and across multiple builds, and how consistency is maintained among both.
“The agency examines fixed and variable parameters and how they’re managed,” Brittan said. “It’s essential to show how you compensate for variability or demonstrate that it’s not a significant issue in the printing process.”
These factors underscore the importance of establishing strong relationships with contract manufacturers and 3D printing providers, according to Brittan. “It’s a team effort that requires data collection from the design and manufacturing sides,” he said.
Material reuse is also a key issue in 3D printing that doesn’t arise as much in traditional machining.
“FDA frequently asks about the mechanical strength, chemistry and morphology of reused materials,” Brittan said. “Submission reviewers want to ensure that the powder maintains consistency in these characteristics, so implants produced in the future are equivalent to those produced today.”
To address this concern, FDA looks for defined reuse protocols and limits. “It’s up to the sponsor to determine these parameters,” Brittan said. “You could change the powder after every use, but that wouldn’t be practical. Instead, establish whether the reuse limit is after 10, 50 or 100 uses, and provide data to support that there will be no significant variability over time.”
Manufacturing residuals is another unique aspect of 3D printing. FDA specifically focuses on titanium powder that remains on printed parts, according to Brittan.
“FDA asks specific questions about the amount, appearance and morphology of the residual powder,” Brittan said. “The critical point here is justifying that these residuals do not pose a biocompatibility concern. This can be supported through literature, data or by comparing the device to a predicate product that has already received FDA clearance to demonstrate that the new device has equal or fewer residuals.”
FDA has been supportive of this aspect of the review process and wants device manufacturers to drive the process, according to Brittan.
“The agency is very open to the use of test coupons, which can relieve the burden of using implants for every build,” he said. “FDA suggests that coupons are an excellent way to characterize your printing process if they can be justified as representative of your device and process. This is particularly beneficial for destructive testing, such as mechanical testing that destroys a piece or chemistry testing that consumes it.”
Sponsors can explain why a particular coupon was chosen and its validity. Standard coupons are available in ASTM standards, but specialized designs can also be used. For example, SpiTrex has developed unique coupons that effectively differentiate various parts of the 3D printing process. FDA is open to the use of these coupons if there’s a clear justification for them, Brittan said.
Brittan noted that validation and process control are tied directly to performance testing, the aspect of the clearance process for which most questions arise.
In addition to standard design rationale, FDA expects a combination of design and process justifications for worst-case builds. The agency looks for data from performance test builds to support these justifications and ensure that the parts will perform reliably under worst-case conditions.
“This involves more than discussing the smallest diameter screw or smallest cross-sectional area in an interbody cage,” Brittan said. “It involves a thorough explanation of design and process considerations.”
He highlighted the importance of understanding the mechanical, chemical and morphological properties, particularly for titanium powder bed builds. These aspects involve using tensile coupons to verify the strength of the build, assessing oxygen composition as an indicator of static and dynamic strength and examining microstructures.
“FDA wants to see how well you understand these parameters and how you control them, especially under worst-case conditions,” Brittan said.
Providing Proof
Capturing this data accurately from builds used for V&V testing is essential to streamline the process. “This data feeds into your monitoring and acceptance activities,” Brittan said. “For instance, if your tensile coupons show a strength of 800 megapascals, your release criteria will be expected to align closely with that figure. Although FDA provides some flexibility, it expects consistency in your chemistry and morphology data per ASTM standards.”
It’s also vital to log and trend data during 3D printing cycles to ensure you consistently operate within your validated parameters. This also helps to identify deviations in the printing process before they become issues.
Brittan suggests engaging with contract manufacturers early in the product development process for 3D-printed 510(k) submissions. Understand and communicate what data is needed to support submissions, justify worst-case 3D printing conditions and ensure that the process data directly correlates with V&V builds. Use that information to establish your lot acceptance criteria and make sure it’s clearly documented in 510(k) submissions.
“These steps will help to reduce FDA questions and facilitate a smoother process,” Brittan said.
DC
Dan Cook is a Senior Editor at ORTHOWORLD. He develops content focused on important industry trends, top thought leaders and innovative technologies.