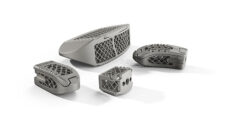
Perhaps no other segment of the orthopedic market has benefited from additive manufacturing (AM) applications more than spine. The technology has revolutionized devices by offering unprecedented freedom in design complexity and customization.
“The ability to create intricate lattice structures, personalized geometries and optimized porosity allows for better biomechanical integration and patient-specific solutions,” said Rick Simmons, Chief Marketing Officer at Spinal Elements. “It allows industry experts to think beyond historical concepts to solve unmet clinical needs.”
While traditional spine implants have standardized properties, AM enables device companies to alter the strength, flexibility and other mechanical characteristics based on patient anatomy and pathology. Simmons said recent advancements in AM — new materials and enhanced printing techniques and post-processing methods — have significantly improved the quality and functionality of spine implants in ways that contribute to better patient outcomes and fewer surgical complications.
“Reducing the stiffness of a material and creating a better surface topography contributes to an increased fusion rate,” Simmons said. “Affecting the porosity on a macro, micro and nano level, when combined with customized surface topology specific to spinal anatomy, assists directly with osseointegration.”
Spinal Elements’ Ventana product line is produced with an AM process that promotes fusion. The line’s C Anterior Cervical Interbody System, P/T Posterior Lumbar Interbody System and L Lateral Lumbar Interbody System were launched in November 2023 as part of the company’s suite of minimally invasive integrated instrument and implantable device solutions.
Unlike competing products, Ventana implants feature a unique “hinged door” design that allows a maximum amount of bone graft material to be packed into the cage, which acts as a delivery vessel to promote fusion.
Ventana’s minimalistic radiolucent lattice design maximizes the amount of bone graft captured in the device and improves visualization during and after spinal fusions. The implants also allow bone graft material to contact the endplates and provide a broad surface to help avoid implant subsidence.
Simmons believes the next big AM development in spine will likely involve the use of patient scans and artificial intelligence to quickly deliver patient-specific implants. “This will reduce the amount of inventory that’s sent to surgical facilities for each surgery and ensure patients get an implant specifically tailored to their needs,” he said.
Creating Cutting-edge Cages
AM allows for the production of porous titanium interbody cages that can increase osseointegration. Alessia Erlingher, Chief Commercial Officer at Spineart, said the company capitalizes on AM to safely reduce the amount of material that’s used to produce the devices. “Less structural density means fewer artifacts in post-op images, which leads to better patient care,” she said.
Spineart’s proprietary 3D printing Ti-LIFE Technology creates a modulus of elasticity that’s closer to that of bone than what’s possible with machined titanium and polyether-ether-ketone (PEEK), according to Erlingher. She noted that the technology’s geometry produces a porous structure that encourages bone ingrowth in implants.
The design of Spineart’s newest cervical cage SCARLET AC-Ti capitalizes on Ti-LIFE Technology to create enclosed parts with enhanced functionalities. For example, the company was able to integrate pre-assembled cam locks into the design for the first. This design advantage creates an implant with a zero profile and saves significant manufacturing time, Erlingher noted.
“While the AM process has allowed us to produce less dense implants, the mechanical properties are maintained compared to traditional machining,” Erlingher said. “There is a great interest in utilizing 3D printing technology in spine because it can maintain implant strength while reducing the density of the devices.”
Spineart published a study in The Spine Journal that demonstrated the advantages of 3D-printed titanium interbody cages with porous surfaces in sheep lumbar fusion models.
Erlingher said that Spineart has learned a lot about its AM process in the last decade. “We’ve looked at every feature of the SCARLET AC-Ti cage and asked ourselves how its design could be improved based on the available technologies,” she added. “Large data analysis gives greater insights on the device’s anatomical variability and allows us to refine design choices.”
It’s that refinement that led to the SCARLET ACT-Ti’s MIMETIX morphometric profile, which was developed with digital models of the vertebrae to optimize the contact surface between the implant and endplates. “We closely replicated the natural endplate morphology, instead of assuming a flat or geometrically domed surface,” Erlingher said.
Ergonomics is often associated with instrument design, but Spineart has applied the concept to implant manufacturing. SCARLET ACT-Ti’s cam lockers create a zero-profile implant and the tunnels for screw insertion are integrated into the device.
“This means we eliminated the need for bulky instruments to guide the screws, giving surgeons an unobstructed view of the surgical field and contributing to a safer procedure,” Erlingher said.
Truly Personalized Care
Jay Dinsmore, Executive Vice President of ADDMAN, suffered a serious spine injury while mountain biking 15 years ago and his company’s Digital Anatomy Printing (DAP) capabilities played a significant role in his recovery.
DAP creates 3D models that closely mimic human anatomy. The technology provides surgeons with detailed recreations of a patient’s spine that they can reference while planning procedures. Spine companies can also use these accurate models to enhance the development and testing of their products.
“We’ve been early adopters of DAP, and I’m a testament to its benefits,” Dinsmore said.
He’s printed numerous models of his spine to monitor anatomical changes that have occurred since his accident and subsequent treatments. He brings the models to appointments with neurosurgeons to discuss his condition and treatment options. The surgeon who performed a recent radiofrequency ablation on Dinsmore’s spine nerves relied on the model and found it to be a helpful planning tool.
“There’s nothing better for surgeons than having access to a physical model of the patient’s spine,” Dinsmore said. “Digital representations are good, but a model’s tactile feedback provides a much more comprehensive understanding of the anatomy that will be operated on. Some surgeons even bring the models into the operating room.”
The process of creating 3D models starts with segmentation from DICOM data, which ADDMAN converts into a mesh file using specialized software to produce a design file that’s ready for 3D printing. Axial3D INSIGHT, an FDA-cleared, cloud-based and AI-driven segmentation platform, converts 2D images into high-quality 3D digital files. Stratasys’ PolyJet 3D printers then produce the models.
PolyJet printing technology, which has been around for about 25 years, has significantly improved over the years. It can create full-color, flexible and rigid materials in a single print. This capability allows ADDMAN to create highly detailed models of complex human anatomy.
The printing and post-processing of the models also present several challenges. Dinsmore noted that front-end segmentation creates the biggest bottlenecks and takes considerable time and engineering resources to complete. He said Axial3D has made significant strides in addressing this issue by allowing ADDMAN to perform segmentation at scale with their platform. He called the advancement an exciting development for the company and its customers.
ADDMAN relies on multiple materials to print life-like anatomical models, including acrylonitrile butadiene styrene (ABS), polylactic acid (PLA), polyvinyl alcohol (PVA) and nylon. Materials are chosen based on the needed strength, durability, flexibility and resolution of the application.
ADDMAN’s comprehensive printing process allows the company to scale model production. Twenty years ago, processing digital data to create detailed spine models took more than 24 hours and the models would be printed in one to two weeks. Today, they’re printed overnight.
Dinsmore has interviewed numerous surgeons who tout the benefits of the DAP but acknowledged that achieving widespread adoption of the models remains challenging due to the lack of billing codes and reimbursement models.
ADDMAN utilizes the capabilities of AM in numerous ways, but Dinsmore believes DAP is the best and most gratifying application.
“It’s amazing to print these models and use them in real-life scenarios. These models have saved and extended lives, which is incredibly rewarding work,” Dinsmore said. “My personal experience is one reason I’ve always been drawn to the medical side of 3D printing. Being able to use this technology for my care is a blessing.”
DC
Dan Cook is a Senior Editor at ORTHOWORLD. He develops content focused on important industry trends, top thought leaders and innovative technologies.