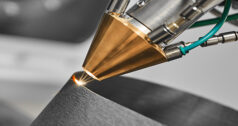
The 3D printing of materials continues to scale as acceptance and adoption of the technology increases, according to a global survey of metal additive manufacturing (AM) practices across various industries.
Nearly 80% of the responding organizations employ metal AM to produce parts, noted the survey, which was conducted by the market analysis firm Additive Manufacturing Research in partnership with 6K Additive.
A majority of the survey’s respondents were executive-level decision-makers, design and engineering professionals and academic researchers. Most worked in R&D, industrial roles and education. Close to half (40%) of the respondents were based in North America, 25% operated in Asia and 19% were in Europe.
Here are some of the survey’s key findings:
- 41% of the respondents print up to 50 parts per year, 21% print 100 to 500 parts and 15% print 50 to 100 parts.
- Steel (26%), titanium (20%), aluminum (17%) and nickel alloy (15%) were the most commonly printed materials.
- Times needed to qualify printed parts ranged from less than a month to six months to a year.
- Consistency and quality of metal AM materials were the most critical considerations when respondents assessed materials suppliers: 52% said it’s extremely important that materials meet industry standards and specifications and 56% highlighted the batch-to-batch consistency of material shipments.
- About two-thirds (66%) of respondents said the quality and consistency of AM metal powders are essential.
- When choosing a supplier of AM materials, 40% cited the rapid availability and lead time of materials and 39% tabbed the reputation and customer service of the supplier as extremely important.
- The cost of materials wasn’t an important factor when deciding on a supplier: 29% of respondents said it was somewhat worth considering, relatively unimportant or not considered.
- 39% of respondents said they are searching for a solution to manage failed prints, scrap and unused powder.
- 85% of respondents said currently available materials in metal AM meet their current requirements.
- A little more than one-third anticipate using refractory metals, 44% are undecided and 21% said they do not anticipate using refractory metals.
- New and unique alloys (32%), increased strength (27%) and reduced weight (21%) were identified as anticipated requirements of future metals.
“As metal 3D printing advances, users are increasingly seeking a broader array of materials to enhance performance beyond their current needs,” the findings noted. “Simultaneously, there is a growing emphasis on sustainability, prompting a quest for solutions to enhance materials handling and minimize scrap.”
That cost was low among the considerations of users who adopt AM, which suggests that the return on investment — by switching to 3D printing or improving the performance or price of printed parts — significantly outweighs reservations about the technology’s expenses, the findings noted. “Instead,” it said, “as the technology moves into the mainstream, the pressure to qualify parts, optimize the production process, secure the supply chain and manage sustainability are front-of-mind.”
AM continues to make inroads in orthopedics based on recent developments in the applications of 3D printing within the industry:
- Paragon Medical shared four benefits of AM design in orthopedics.
- OrthoVentions invested in MotioOV, an early-stage company created in partnership with the Hospital for Special Surgery, to develop a novel 3D-printed implant to address stiffness and pain associated with arthritis of the first metatarsophalangeal joint.
- restor3D is launching 3D-printed foot and ankle solutions.
- During an in-booth presentation at OMTEC 2024, Himed will discuss its new Bioceramics Center of Excellence (BCOE), which reduces the barriers for companies that want to explore the 3D printing of bioactive ceramics.
Greg Morris, a pioneer in the additive manufacturing industry, recently said that the orthopedic industry is focused on enhancements to 3D printing’s speed and accessibility to broaden its reach.
“This trend extends beyond metals to include polymers,” he said. “As a result, it’s anticipated that the adoption of AM will continue to increase in orthopedic segments.”
DC
Dan Cook is a Senior Editor at ORTHOWORLD. He develops content focused on important industry trends, top thought leaders and innovative technologies.