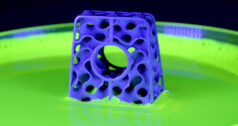
The continuing emergence of additive manufacturing coincides perfectly with the movement toward personalized orthopedic surgery.
3D-printed implants better match the anatomy of individual patients, leading to improved outcomes, reduced operating times and smoother workflows for orthopedic surgeons.
“Our company’s philosophy revolves around making the implant fit the patient rather than forcing bone to accommodate an off-the-shelf device,” said Nathan Evans, Ph.D., Vice President of Technology and Strategy at restor3d.
Evans said restor3d initially explored additive manufacturing applications in personalized orthopedic care to address complex, one-off cases. “Our current perspective extends beyond these exceptional surgeries,” he added. “We believe in applying personalized solutions to everyday procedures in the knee, hip, shoulder and ankle.”
Like personalized surgery, additive manufacturing is not a one-size-fits-all proposition for orthopedic companies. They must consider the purported benefits and potential drawbacks of the production methods, materials that are used and the regulatory and cost constraints before investing resources into the technology that promises to reshape how implants are produced.
Assessing the Differences
Electron beam melting (EBM) and selective laser melting (SLM) build parts by fusing stacked components from a bed of raw powder.
EBM generally boasts faster printing capabilities due to its energy deposition and ability to eliminate the need for downstream post-production treatments. Parts produced with EBM have rougher surfaces, which might promote bone growth but lack fine-tuned accuracy.
SLM offers advantages in finer feature control, tighter tolerances and smoother surface finishes.
Dr. Evans said mechanical properties are a critical consideration when assessing each option. “SLM exhibits significantly better fatigue strength than EBM,” he said. “This is particularly crucial when building porous orthopedic implants. Mechanical failure can have serious consequences.”
Porous structures carry an inherently higher risk of fracture due to reduced metal content, Dr. Evans noted. “Ensuring optimal fatigue resistance is crucial, particularly for orthopedic implants that are subjected to repetitive loading over thousands or millions of cycles,” he added.
He believes the significance of mechanical properties is often underestimated, making it essential to maximize the fatigue life of additively manufactured parts.
Dr. Evans also noted that advancements in laser technology, such as dual and quad lasers, have significantly increased printing speeds, closing the gap with EBM in terms of production capacity.
“Additionally, emerging laser technologies allow for comparable layer thicknesses to EBM, providing a balance between resolution and speed,” Dr. Evans said. “These advancements offer a blend of the benefits of EBM and laser technologies, representing a promising evolution in additive manufacturing.”
Dr. Evans noted that restor3d employs SLM to specialize in manufacturing small, intricate spine devices and large components for joints and huge defects. “Despite our broad range of products, we’ve opted to utilize a single printing technology,” he said.
That decision was based on the challenge of managing validations across multiple modalities. “It’s simpler to maintain consistency in regulatory pathways and printer qualifications,” Dr. Evans said. “Although faster printing with EBM might seem appealing, the logistical advantages of a unified technology outweigh the speed benefits.”
Materials Continue to Evolve
Titanium, stainless steel and, to a lesser extent, cobalt chrome are established materials in additive manufacturing. Dr. Evans said interest in alternatives such as nitinol and mixed materials is increasing.
“Printing cobalt chrome on the articulating side of a total knee implant and using titanium for the bone side to promote osseointegration presents intriguing possibilities,” he added.
The potential for new materials development, including biodegradable options like magnesium, represents ongoing evolution in the field.
Polymers such as PEEK present several challenges to consider in 3D printing applications, according to Greg Morris, a pioneer in the additive manufacturing industry.
One relates to understanding the mechanical strengths of various polymers. Another involves the difficulty in achieving production quality that matches injection molding.
“While metals can readily achieve machined or cast finishes, polymers often exhibit layering, which may not provide the sleek appearance associated with injection molding,” Morris said.
Ceramics are an intriguing and emerging option in additive manufacturing. Morris said ceramic parts are typically formed in a green state before undergoing a sintering process.
“Although there are limitations in the additive manufacturing of ceramics, especially regarding the size of parts due to machine constraints and the nature of the process, advancements are being made in the industry,” he said. “This development opens various possibilities for ceramic applications, although currently, the parts that are produced tend to be smaller. Nevertheless, it’s important to monitor this area as it evolves.”
Addressing the Barriers
Industry standards and regulatory guidance are continuously evolving due to the rapid advancement of additive manufacturing. FDA and organizations like ASTM and ISO are striving to keep pace with the changes.
“Don’t be solely focused on adopting the latest technology without considering the regulatory and validation implications,” Dr. Evans said. “Working closely with printer manufacturers, such as 3D Systems and EOS, is essential. These companies are well-versed in handling validations and qualifications.”
It’s important to optimize throughput in additive manufacturing. It’s also essential to mitigate regulatory risks.
“Our positive experiences on this front stem from collaborating closely with printer manufacturers to leverage their engineering and regulatory expertise,” Dr. Evans said. “I strongly advise collaborating closely with printer manufacturers to effectively navigate the complexities of additive manufacturing.”
Several software design systems offer enticing applications in additive manufacturing, such as the ability to create gradient lattice structures.
“However, a significant challenge arises when these designs cannot be seamlessly exported to the printing software,” Dr. Evans said. “While the design may appear impressive in a CAD file, the inability to transfer it to a printer poses a major limitation. This highlights a critical software constraint in additive manufacturing.”
Dr. Evans said some systems offer more flexibility with open-source or modular software approaches. He pointed to the importance of considering not only the physical hardware of a printing system but also its accompanying software workflow, weighing the respective advantages and disadvantages of each.
Morris said software companies are working to alleviate the burden of design engineers who must optimize products for additive manufacturing by letting them avoid becoming experts in 3D printing production methods.
“If engineers could achieve 90% completion of their designs with basic input and allow the software system to rapidly generate the desired outcomes, that would represent a significant breakthrough,” Morris said. “This approach has the potential to address a lack of in-depth understanding of designing for the additive manufacturing process.”
Artificial intelligence (AI) is expected to play a crucial role in the transformation of additively manufactured parts, Morris noted.
“AI can analyze multiple design iterations swiftly and determine the optimal solution,” he said. “Ultimately, the goal is for software companies to streamline the design process and enhance efficiency in additive manufacturing.”
Cost remains a significant barrier to the widespread adoption of additive manufacturing.
“Designing for the additive manufacturing process is crucial to mitigating cost barriers,” Morris said. “By incorporating lattice structures and consolidating multiple components into a single part, designers can optimize the printing process.”
Increased Adoption
Dr. Evans said the rapid evolution of additive manufacturing leads to new advancements that are constantly reshaping the landscape, with innovations emerging nearly every year to drive the industry forward. He envisions a continued evolution toward applying additive manufacturing to high-volume, everyday procedures.
“As lead times decrease and costs become more competitive, we’ll reach a tipping point where additively manufactured implants become not just feasible but potentially cost-effective,” he said. “This shift will be facilitated by the elimination of inventory concerns associated with traditional implant models.”
In the meantime, the orthopedic industry is focused on enhancing 3D printing’s speed and accessibility, thereby broadening additive manufacturing’s reach.
There’s a growing consensus regarding the effectiveness of additive manufacturing, prompting contract manufacturers and OEMs to embrace its utilization, Morris said.
“This trend extends beyond metals to include polymers,” he added. “As a result, it’s anticipated that the adoption of additive manufacturing will continue to increase in orthopedic segments.”
DC
Dan Cook is a Senior Editor at ORTHOWORLD. He develops content focused on important industry trends, top thought leaders and innovative technologies.