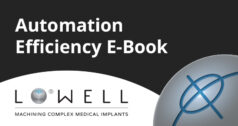
Lowell has authored white papers over the years on diverse subjects and we’ve been asked many times to combine the papers by subject matter. This summary is designed to help readers focus on emerging opportunities in streamlining the production and inspection of medical devices.
One of the biggest advantages of automation is the transformation that comes with allowing talented professionals to focus on higher-value, essential tasks. This produces greater employee performance and increasingly efficient production, which delivers cost-effective manufacturing of device components.
We began this journey of automation with the introduction of robots into our CMM room. Today, robots, co-bots and other automation tools are at work throughout our facility. We take immense pride in our automation leadership.
The topics outlined below are connected and can support your journey to embracing automation and increasing the efficiency of your device manufacturing. For the full-length eBook on this topic, visit the Lowell website to download.
Topic Focus:
- Automation of Inspection Equipment
- Statistical Methods for Precision Machining
- Automated Data Analysis: Making the Case
- Leveraging Automated Inspection to Counter Labor Shortages
Automation of Inspection Equipment
Like many domestic manufacturers, Lowell faces intense competition for business. We constantly seek ways to add value to the work environment of our associates. Lowell’s associates are highly trained and experienced machinists — the average employee has worked at the company for over 20 years. Lowell is faced with a dual challenge: reducing costs and retaining experienced employees. The company is achieving both goals through automation.
Our journey to optimize automation began with investing in a sophisticated sub-micron accuracy PMM from Leitz of Wetzlar, Germany to add inspection capacity to our existing Brown & Sharpe CMM. (This same equipment is used to calibrate gages at NIST.) To operate at peak accuracy, we built a 450-square-foot, climate-controlled space that maintains a temperature variation of <.9° +/- 1° F to house the high-end equipment.
We doubled our production capacity, but inspectors couldn’t keep up with the demand. These two highly sophisticated pieces of equipment sat idle while a Lowell associate loaded and unloaded parts into the machines by hand. This downtime meant that fewer parts were inspected while customers and machinists waited for their parts. Clearly, this was not the fault of the operators — a human can only work so fast before they tire or start to make mistakes. But what about a robot? This question led us on a journey to advance everything we could to enhance automation.
Statistical Methods for Precision Machining
Orthopedic device OEMs utilize data to prove their products’ efficacy to hospitals, doctors and regulatory agencies. Lowell is a leader in the use of measurement and data to improve and streamline the product development process.
It’s the start of your next project — the design of a precision-machined medical device component. Your customers were clear on their requirements and provided a list of product features to incorporate into the design. Your marketing and engineering teams successfully flowed down those features into technical requirements and now it is time for you, the design engineer, to generate a toleranced mechanical drawing.
If you are lucky, you can refer to an industry standard such as the Machinist Handbook and pull the nominal and tolerances. Most times, however, things are not that easy. It is at this stage where design engineers face divergent forces. On one hand, you must think in terms of the available design software to make the solid model. On the other hand, you must maintain the functional requirements of the device. How do you proceed?
Automated Data Analysis
Lowell’s manufacturing team needed to make a customer’s part on a new machine. The newer mill/turn machine was automated and would save machining time versus the original milling machine, but it required reprogramming the part.
To confirm that the new process wouldn’t impact product results, the team performed several process qualification activities. They ran three lots, then measured and analyzed the data of specific features. The results proved that the new process was at least as capable as the previous manufacturing method.
This type of process qualification is a critical step for contract manufacturers to build OEM confidence in the manufacturing process. It provides a detailed analysis of raw data to prove that a manufacturer can create the medical device or component consistently, even over multiple purchase orders and lots.
Often, the effort of process qualification is manual and tedious. Using automated data analysis for process qualification activities can streamline the effort for manufacturers and their customers.
Leveraging Automated Inspection to Counter Labor Shortages
At a time when the labor market is tight and competitive within the medical device manufacturing industry, retaining quality employees — and supporting them with additional skills, training and responsibilities — is more important than ever.
From an employer perspective, we can no longer assume that competitive pay alone will be enough to attract and retain the level of quality employees needed to move our businesses forward. We need to think about the day-to-day work and experience our team will endure throughout their career. This concern is important at all levels of the workforce, from less experienced inspectors to highly skilled programmers and engineers. We have made significant shifts in creating the best possible environment for our team by leveraging technology to enhance their experience while also identifying improved efficiency and savings in the production of quality components.
Connect with Lowell
A commitment to automation is just one aspect of our work that’s designed to support customers’ needs for quality, timely delivery and performance. Contact us to review your current projects and learn more about how we can help you achieve your goals. We can be reached by email or phone 763-425-3355.