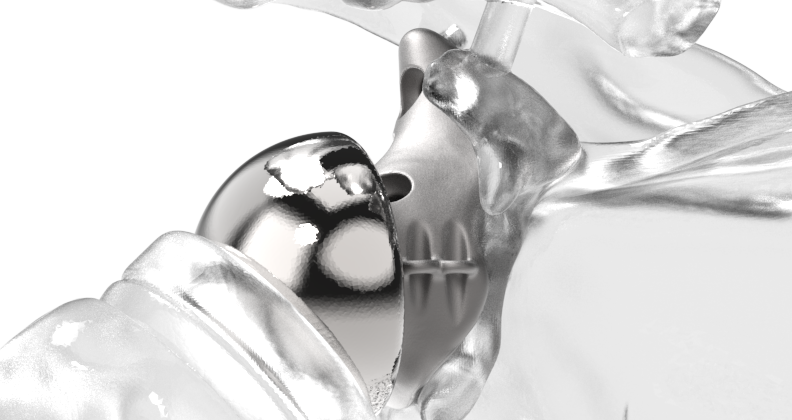
The orthopedic industry has widely adopted 3D-printed implants for spine surgeries, and now additive manufacturing has become a more cost-effective option for large joint applications. Developments in 3D printing technologies and design strategies enable manufacturers and surgeons to approach arthroplasty in a whole new way. Additively manufactured implants and personalized instruments can help increase efficiencies, reduce costs and improve outcomes. Let’s explore how.
Increased Efficiencies
3D printing increases efficiencies for the manufacturer, the surgeon, the hospital, and even patients in many different ways. Additive manufacturing (AM) enables faster production of medical devices compared to traditional manufacturing methods. Plus, implants with complex geometries and porous structures can be manufactured monolithically. Advancements such as multi-laser 3D printing platforms, the ability to print at a 90µm layer thickness without compromising quality, and build strategies that minimize post-processing steps further accelerate the production of medical devices.
Through customization, 3D printing enables the production of implants tailored to each patient, which reduces the need for intraoperative modifications or additional surgeries, and saves time and resources.
With streamlined throughput of standard-sized stock and personalized devices, manufacturers can speed the delivery of devices to surgeons, improve hospital processes, and address supply chain challenges.
Reduced Cost
AM has become more costeffective compared to traditional manufacturing, particularly for complex parts. With faster print platforms, new materials, and software to expedite workflows, manufacturers can now 3D-print applications such as glenospheres, personalized pelvic implants, acetabular cups, and femoral knee components more economically than ever. Additionally, 3D printing allows manufacturers to expand device portfolios without investing in and holding on to inventory.
Improved Outcomes
In recent years, 3D printing technologies helped create personalized implants that provide a custom fit to promote better joint alignment, improved implant stability, and reduced risk of loosening.1,2 The ability to build intricate lattice and porous structures supports better osteointegration, leading to faster patient recovery, increased mobility, and better long-term success rates.
Advances in AM technologies and design strategies have made it possible to expand patient-specific applications and enable wider adoption. 3D printing can also be used to create customized surgical instruments that improve surgical precision.
3D printing is revolutionizing the orthopedic device industry by increasing efficiencies, reducing costs, and improving patient outcomes. Arthroplasty is one area in which AM is showing great promise, and continued research and development in this area will lead to even more innovation in the future.
Are you considering AM for your next project? Talk to an expert in 3D Systems’ Application Innovation Group to explore how a complete concept-to-delivery workflow can help you expedite your path to market.
- Benignus, Christian, Buschner, Peter, et al. Patient Specific Instruments and Patient Individual Implants—A Narrative Review. J. Pers. Med. 2023, 13(3), 426.
- Lee, Jin-Ah, Koh, Yong-Gon, et al. Biomechanical and Clinical Effect of Patient-Specific or Customized Knee Implants: A Review. J. Clin. Med. 2020, 9(5), 1559.