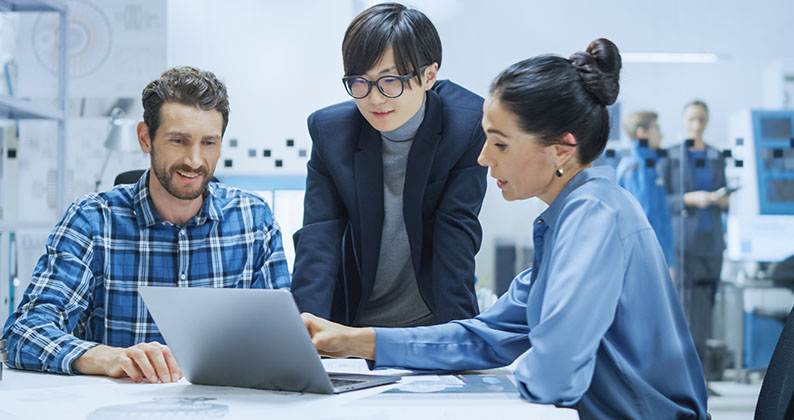
The increased interconnectivity and smart automation introduced by Industry 4.0 and the personalized surgical care afforded by the enabling technologies of Industry 5.0 have brought sweeping changes to the orthopedic industry.
Innovation holds the important promise of improved patient care, but device makers are having a tough time adapting to the changing dynamics within the manufacturing workforce.
“Digital ecosystems create a growing need for workers with advanced technical skills in software programming, data analysis and robotics,” said Jeff Richardson, Industry Solution Director at Critical Manufacturing, a provider of MES and IoT Data Platforms. “Orthopedic companies are looking for highly skilled workers with the background and abilities to develop, implement and manage these technologies.”
The growing pains that companies experience during the transition to digital surgery provide an opportunity to remake product development teams that will continue to improve patient care, keep pace with innovation and help shape the future of orthopedic surgery.
Stiff Competition for Talent
Integrated workforces that can adapt to the changing landscape of device development are critical as conventional manufacturing methods overlap with technological advancements. Orthopedic companies are responding to changing staffing dynamics by ramping up efforts to recruit young, tech-savvy workers, according to Jeph Ruppert, Vice President of Technical Business Development at 3D Systems.
“Today’s product development professionals must possess creative problem-solving skills,” he said. “They can develop those skills through higher education, but they must be able to apply them in a practical manner.”
With the demand for skilled labor so high, orthopedic companies are open to creative recruitment methods. Some strategies include attracting new talent by offering career guidance and partnering with recruiting firms.
Rob Kraal, Vice President and General Manager of Connected Health at Zimmer Biomet, said Industry 4.0 is reshaping the way his company hires and recruits new talent.
“We made a conscious decision to invest in robotics, mixed reality and a patient care management platform that ties these technologies together,” he said. “This requires us to not only recruit in traditional engineering fields, but also in software engineering disciplines that focus on web, mobile and API development. We must also hire UI/UX design teams that improve the usability of our software.”
Kraal said Zimmer Biomet’s customers constantly report that clinical data is vital to their R&D efforts, but the vast amounts of information can be overwhelming to manage and mine for practical insights. “We have recruited machine learning engineers, data scientists and clinical data scientists to address this need,” he added.
Kraal acknowledged that hiring new talent with specific technical experience is an intensely challenging endeavor. “In the past, we competed for new hires in a fairly small talent pool,” he said. “Now that our company is building sophisticated medical-grade software that clinicians use in practice, we’re competing for talent with big tech companies and the major players in the orthopedic industry.”
Most industries have undergone a digital transformation, which has further diluted the pool of tech workers. Still, orthopedics provides a potential advantage against which other fields can’t compete. Zimmer Biomet’s focus on creating technical solutions that significantly improve patient outcomes appeals to younger members of the workforce and gives the company a leg up on the competition in other fields, according to Kraal.
“We’re a mission-driven organization, and that’s what sets us apart when we recruit new talent,” he said. “We have a compelling case to make when we’re interviewing members of the younger generation who are getting started in their careers. They have the chance to make software that helps patients recover from joint replacement surgery. That’s an attractive opportunity.”
Future orthopedic workforces will include professionals with the variety of skills companies need to function and remain competitive as surgery becomes digitized and specialized.
“We’ll continue to require smart, motivated people to build the hardware that surgeons and patients need,” Kraal said. “We’ll also need talented technical workers who will design and build the digital tools of the future.”
Recruiting workers with diverse professional backgrounds from outside of healthcare who are unconstrained from “the way things have always been done” will help break down old paradigms.
“There is so much opportunity to improve how orthopedic care is delivered,” Kraal said. “It’s useful to get fresh perspectives on the problems that need to be solved.”
Focusing on the Similarities
Industry 4.0 is changing the work culture within the orthopedic industry and creating new opportunities for software designers and mechanical engineers who can leverage new technologies. “But fostering collaboration among mechanical engineers and software experts can be challenging due to their different backgrounds, skills and perspectives,” Richardson said.
He cited significant challenges to getting both groups on the same page, including communication barriers, different work processes, limited domain knowledge and resistance to change. Orthopedic manufacturers are developing strategies to break down these barriers and help existing workers adapt to the industry’s technical evolution and acquire the skills needed to succeed in a digitized workplace.
They are experimenting with a variety of tactics aimed at developing workforces that are experts in burgeoning technologies such as robotics, artificial intelligence (AI) and additive manufacturing. This often involves investing in training and education programs, offering career development opportunities and fostering a culture of continuous learning.
These initiatives often revolve around ways of generating collaboration among software and mechanical engineers. Ruppert, who has sat on both sides of the project management table, believes that efforts to bridge the gap between the two seemingly disparate groups should focus on finding the commonalities they share.
“Developing software, hardware and processes demands intentional and codified methodology,” he explained. “There are more similarities between hardware and software engineers than we might think.”
Coding an array of ones and zeroes isn’t the same as testing mechanical forces, but a significant interaction between the two tasks must take place during the product development process. “Orthopedic leaders must be intentional in their understanding of how both sides develop, validate and verify their work,” Ruppert said.
Kraal believes constructive collaboration is key for getting software and mechanical teams to work together effectively as the orthopedic industry deepens its reliance on modern technologies.
“Early on, mechanical engineers were curious about what the software side was up to, but recognized that the changing healthcare landscape required their contribution,” he said. “It’s always going to be about balancing the needs and impact of both groups.”
Mechanical engineers have a more linear/sequential approach to tackling projects, while software professionals use agile methodologies that involve frequent iterations. Those different ways of problem solving can work in concert if the two teams communicate early and often during product development projects.
“We typically report out on a monthly basis to ensure that the various groups involved in projects are aligned and launch plans are on track,” Kraal said.
Tech workers and mechanical engineers might also have different levels of comfort with new technologies and how to best deploy them. “Creating a culture of openness and collaboration that encourages everyone to embrace needed change and continuous learning is a must,” Richardson said. “Consensus should be reached on what technologies will deliver the highest value in the shortest amount of time.”
For example, greater throughput could be achieved by implementing an MES as opposed to purchasing a new piece of equipment. “Finding a way to integrate different work processes is important to developing a shared understanding of how to work together effectively,” Richardson added.
The Foundation for Success
Ruppert described Industry 4.0 as the nexus between the digital and physical worlds of orthopedic manufacturing, where automation offers the possibility of producing more with less manpower. Still, it’s impossible to eliminate the important contributions of skilled trade workers. “Metal still needs to be cut, and parts still need to be produced,”
Ruppert said. “That’s been challenging for many orthopedic manufacturers because of the lack of available skilled trade professionals. Finding a good machinist or craftsman is becoming much more difficult for orthopedic manufacturers. They need to find the right balance between technical labor and craftsmanship.”
Orthopedics is not immune to nationwide staffing shortages that are impacting the healthcare industry. The United States is experiencing a major shortage in skilled labor, according to a 2022 survey of members of the National Association for Business Economics. More than half (57%) of the survey’s respondents reported a shortage of skilled workers.
Ruppert acknowledged that workplace culture in America could be a contributing factor. “Pursuing a career in trade professions feels like an afterthought,” he said.
Orthopedics will attract new talent by understanding the needs of potential new workers and initiating outreach programs that expose young talent to the industry’s storied past and promising future.
“Innovation in orthopedic product development is possible because of its rich manufacturing past,” Ruppert said. “The transformation of our business will be built on the shoulders of the great work done by the professionals who initiated the innovation that produced the device improvements we see today.”
PM
Patrick McGuire is a BONEZONE Contributor.