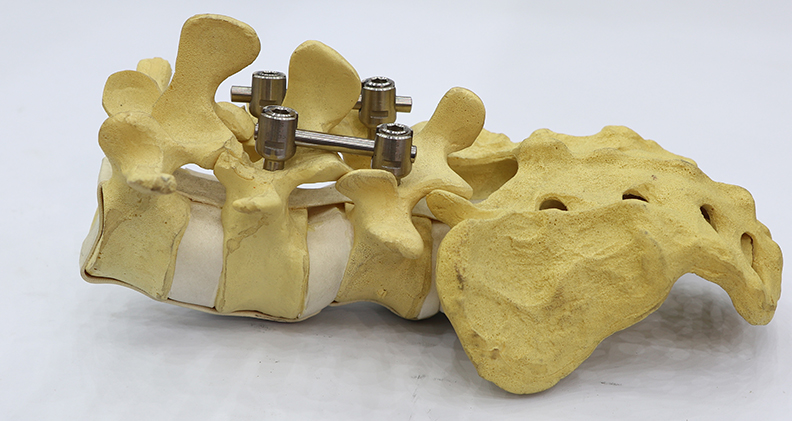
While titanium alloys have long been used in various orthopedic implants and instruments, a startup company believes that its proprietary nano-structured metals can enhance the material.
Boston-based Rosies Base is developing bio-compatible, durable and cost-effective nano-structured alloys to be used for orthopedic implants, spine implants, minimally invasive surgical tools and robotic surgery instrumentation. The company’s nanoTi is a titanium alloy created using a proprietary metallurgical rolling process that delivers ultra-fine-grained alloys, which are thinner and stronger than standard alloys. The material also possesses antimicrobial properties, according to the company.
Rosies Base’s process was established by its parent company Komatsuseiki Kosakusho (KSJ). A precision manufacturer, KSJ initially prioritized the fuel injector and watch markets. It has since expanded into medical devices, seeking industries that could benefit from the mass production of ultra-fine-grained metal alloys.
The proprietary process compresses the metal but does not change the basic composition of the material, be it titanium, stainless steel or cobalt chrome. Rosies Base’s nanoSUS, a stainless steel material, has been used in FDA-cleared medical devices. Now, the company is targeting titanium for use as an orthopedic material.
Rosie Base’s orthopedic entrance includes a research agreement with SpineCraft. The partnership calls for the companies to investigate the compatibility and effectiveness of nanoTi in spinal implant rods.
“SpineCraft is dedicated to developing next-generation spine surgery systems to improve and enhance the quality of life for patients with spine disorders,” said SpineCraft President & CEO Wagdy Asaad, M.D. “We are eager to explore the potential of the innovative nanoTi alloy developed by Rosies Base.”
Stiffness is a concern with many materials used in spinal implants, said Hassan Serhan, Ph.D., CTO at Rosies Base. Stiff implants can cause adjacent segment degeneration, leading to spinal implant rod failure.
“Not only is our [nanoTi] harder, but we are stronger, and we are softer, or less stiff, in a way that accommodates for a transition between the adjacent segment,” he said. “From the clinical advantage, you’re dealing with a material that is not as stiff. Aside from the implants’ failures, bacterial adhesion or deep wound infections, there is a clinical value proposition. We’re investigating all of these claims.”
The company’s nanoSUS has improved fatigue performance by about 40% over traditional stainless steel, said Dr. Serhan. They’re hoping to achieve similar results with nanoTi.
Further, the material is easier to process. The finishing time for nanoSUS was 50% faster, according to Rosies Base.
While Rosies Base is starting with spine implants, it sees nanoTi as a platform technology with numerous orthopedic applications. It will seek FDA 510(k) clearances of nanoTi implants while conducting studies in larger animals that further examine their antimicrobial property claims. Animal studies are expected to begin in 2023.
CL
Carolyn LaWell is ORTHOWORLD's Chief Content Officer. She joined ORTHOWORLD in 2012 to oversee its editorial and industry education. She previously served in editor roles at B2B magazines and newspapers.