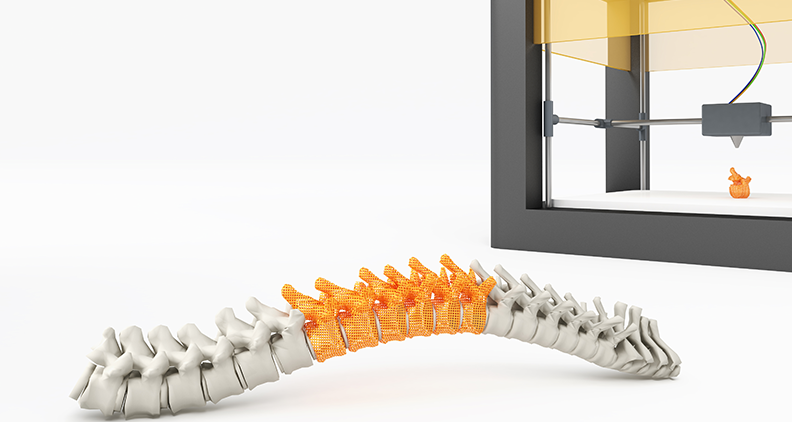
Implant Surfaces and CMDC Labs have agreed to expand a joint development effort to pursue immunological and tissue integration research relating to machined and 3D-printed titanium implantable medical devices. For the last decade, the companies have collaborated to optimize six unique titanium topologies that preferentially encourage targeted cell lines to attach to medical devices: for example, direct Osteoblast attachment to spinal implants while minimizing fibroblast interference.
Working together, the companies will now more broadly analyze the body’s immune response, microbial response, and relative surface biocompatibility of well-established post-treatments for titanium and titanium alloy devices, with particular attention to 3D-printed medical implants. Recent literature suggests some surface post-treatments may trigger negative bacterial and immunological response to a device.
“Our recently expanded research capabilities at CMDC Labs will allow thorough investigation of the bioactive coatings developed by Implant Surfaces by analyzing specifically how the immune response to a 3D-printed titanium surface’s post-treatment affects cell attachment and proliferation in a newly developed in vitro diagnostic model. In addition, we hope that delivering that specific biological and chemical feedback exactly when needed will speed development,” said Dan Storey, Ph.D. and CEO of CMDC Labs.
Implant Surfaces is known within the spinal market for creating a nano-engineered titanium coating applied to polyetheretherketone (PEEK) implants that significantly enhances bone cell (osteoblast) attachment while nearly eliminating fibroblast encapsulation. To date, over 50,000 implants with the company’s IntimateBondâ„¢ Osteoblast coating have been used in Spinal and Foot & Ankle procedures.
Both companies expect the methods used in this joint project will speed up surface development dramatically. Michael Paul, Director of Equipment and Processing Technology for Implant Surfaces said, “Closely matching surface development with the advanced immunological testing we need, exactly when and where we need it, will provide near real-time feedback on the entire series of nano modifications required to deliver the surface’s target electrical and chemical properties. Eliminating scheduling, availability and waiting time will also save a tremendous amount of time.”
“We’re hoping to prove out this approach with Implant Surfaces so we can make it available to other companies that need biological testing tightly coordinated with surface or product development,” said Christina Thomas, VP of Testing Operations for CMDC Labs.
Source: Implant Surfaces
JAV
Julie A. Vetalice is ORTHOWORLD's Editorial Assistant. She has covered the orthopedic industry for over 20 years, having joined the company in 1999.