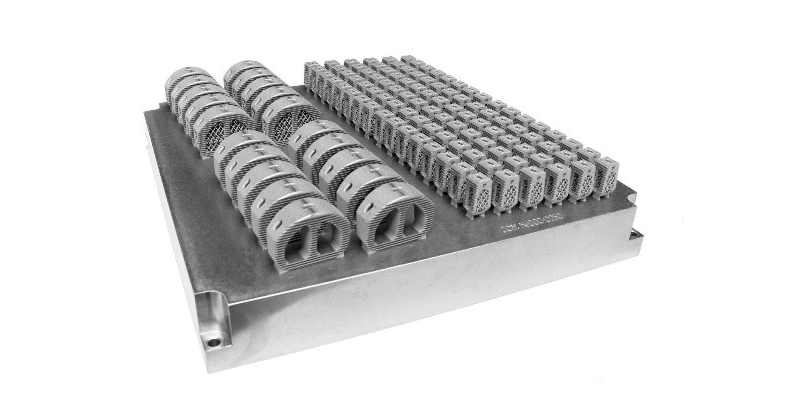
Amnovis has incorporated process improvements into its additive manufacturing (AM) contract manufacturing workflow for titanium implants. This has led to significantly increased productivity on behalf of titanium spinal cage and other medical device OEMs. Amnovis is now able to produce 3D-printed spinal cages at lower cost and shorter lead times.
Amnovis’ founders were among the first to employ laser powder bed fusion (LPBF) for printing titanium medical implants. Incorporating the process improvements into its manufacturing workflow allows Amnovis to expand its potential for standard and patient-specific medical device innovation.
Ruben Wauthle, Amnovis CEO and Co-Founder, said, “For us, innovation benefits from material and process enhancements as well as the ability to increase AM productivity. By scaling our manufacturing capabilities for quality-critical applications, such as medical devices, we ensure faster delivery at lower cost, while maintaining our quality standards.”
“We see great potential in innovating various AM applications across a broad spectrum of medical device types. Highly-efficient 3D printers enable us to better align design and development with material selection and manufacturing excellence. Our joint offering with selected partners comprises of the complete process for customers and prospects to aim high and move fast, while removing hurdles in medical device development, validation and manufacturing.”
Source: Amnovis
JAV
Julie A. Vetalice is ORTHOWORLD's Editorial Assistant. She has covered the orthopedic industry for over 20 years, having joined the company in 1999.