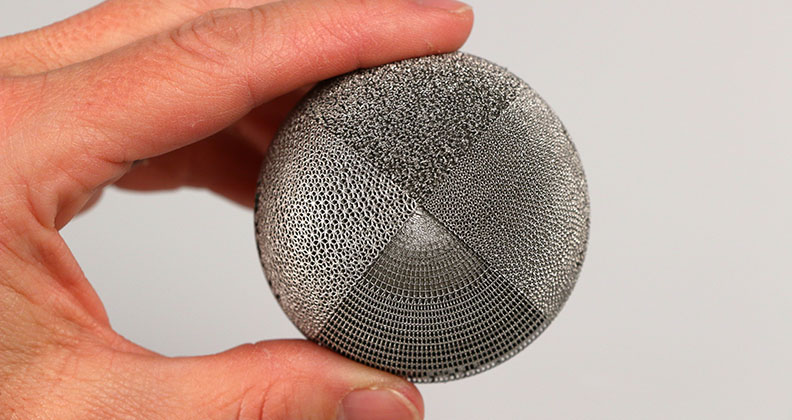
The typical timeframe for engineering teams to move their orthopaedic device innovations from market assessment and prototyping to documentation and submission is 12 months to two years. The industry-accepted average is 20 months. Yet each month of delay increases the risks of escalating costs and shifting requirements in today’s rapidly growing medical device industry.
Innovative orthopaedic solutions push boundaries, creating complex design and additive manufacturing challenges. Moving devices quickly to market seems like an arduous task, but a streamlined path to submission makes it much more realistic and less complex. The key to shortening ideation and validation timeframes significantly, and expediting time to revenue, is partnership.
A Faster Path to Market and ROI
Innovators can move more efficiently by leveraging the regulatory insights, design expertise, and vetted validation processes of experienced industry partners. As a bonus, external teams bring bandwidth to the table—a helpful benefit for tightly-stretched in-house development teams.
3D Systems is a company long sought out by innovators to partner on various phases of device design and additive manufacturing because of the company’s pioneering role in the 3D printing industry. Working with healthcare customers for over 30 years, 3D Systems noticed an interesting trend: when its team of expert consultants was involved from beginning to end—from concept development to qualification—the time to submission was significantly less than the industry average. Instead of 12 to 24 months, it was taking as little as three to six months.
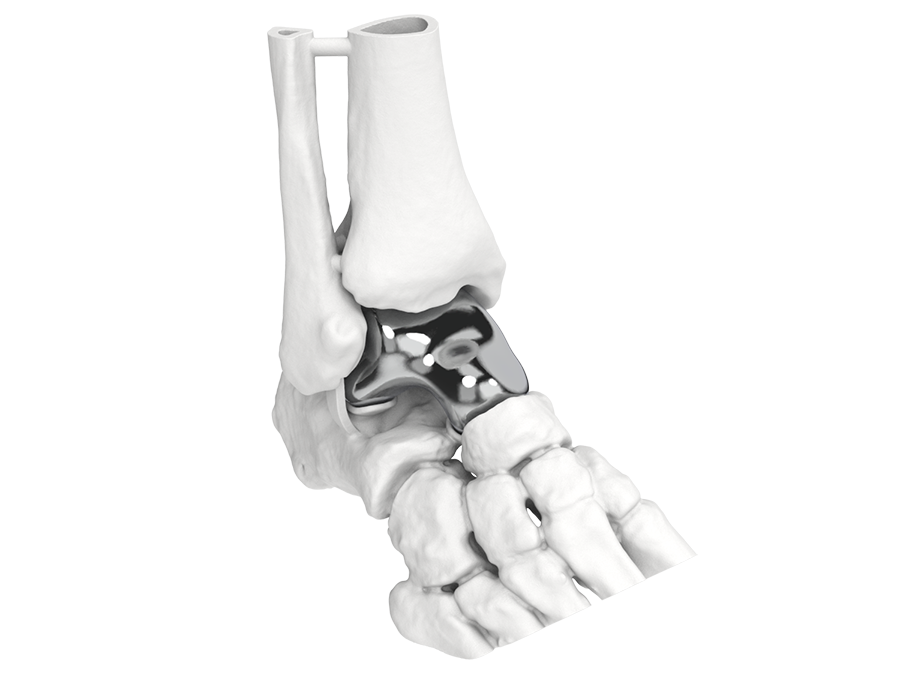
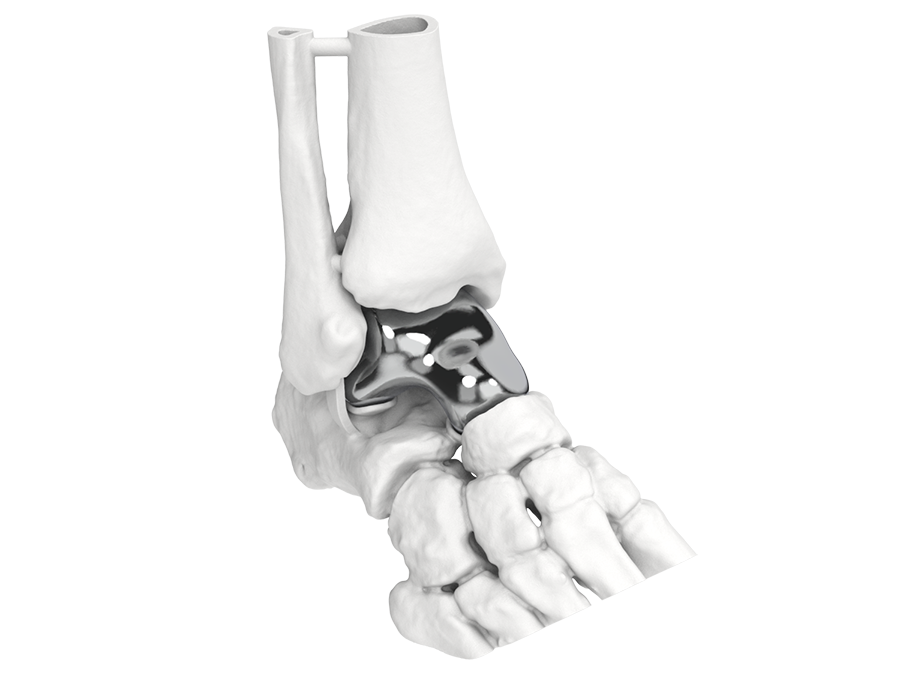
Innovative orthopaedic solutions push boundaries, creating complex design and additive manufacturing challenges. A streamlined path to submission makes it much more realistic and less complex to move devices to market quickly.
A Controlled Process and Advanced Technologies for Unrestrained Innovation
3D Systems’ team of consultants is called the Application Innovation Group (AIG). Among other things, the team is currently working with customers on patient-specific interbody fusion devices, shoulder replacement solutions, and talar implants in cobalt chrome.
With its vetted device validation process and regulatory expertise—including multiple master access files with FDA—complex problems in design and production become quickly solvable. Development and validation are streamlined, helping device manufacturers get innovations to market in record time. It’s what makes 3D Systems’ AIG such a powerful ally.
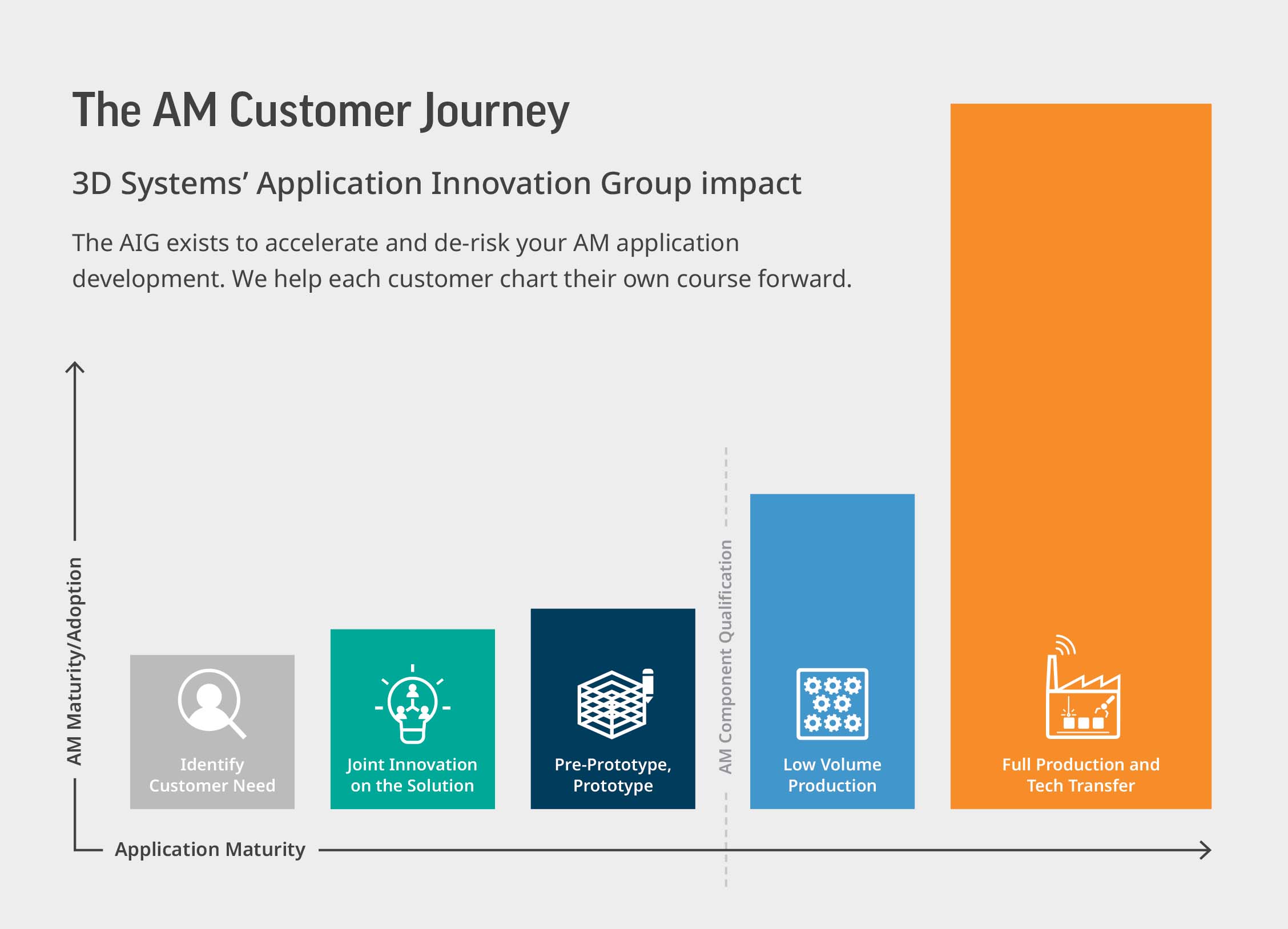
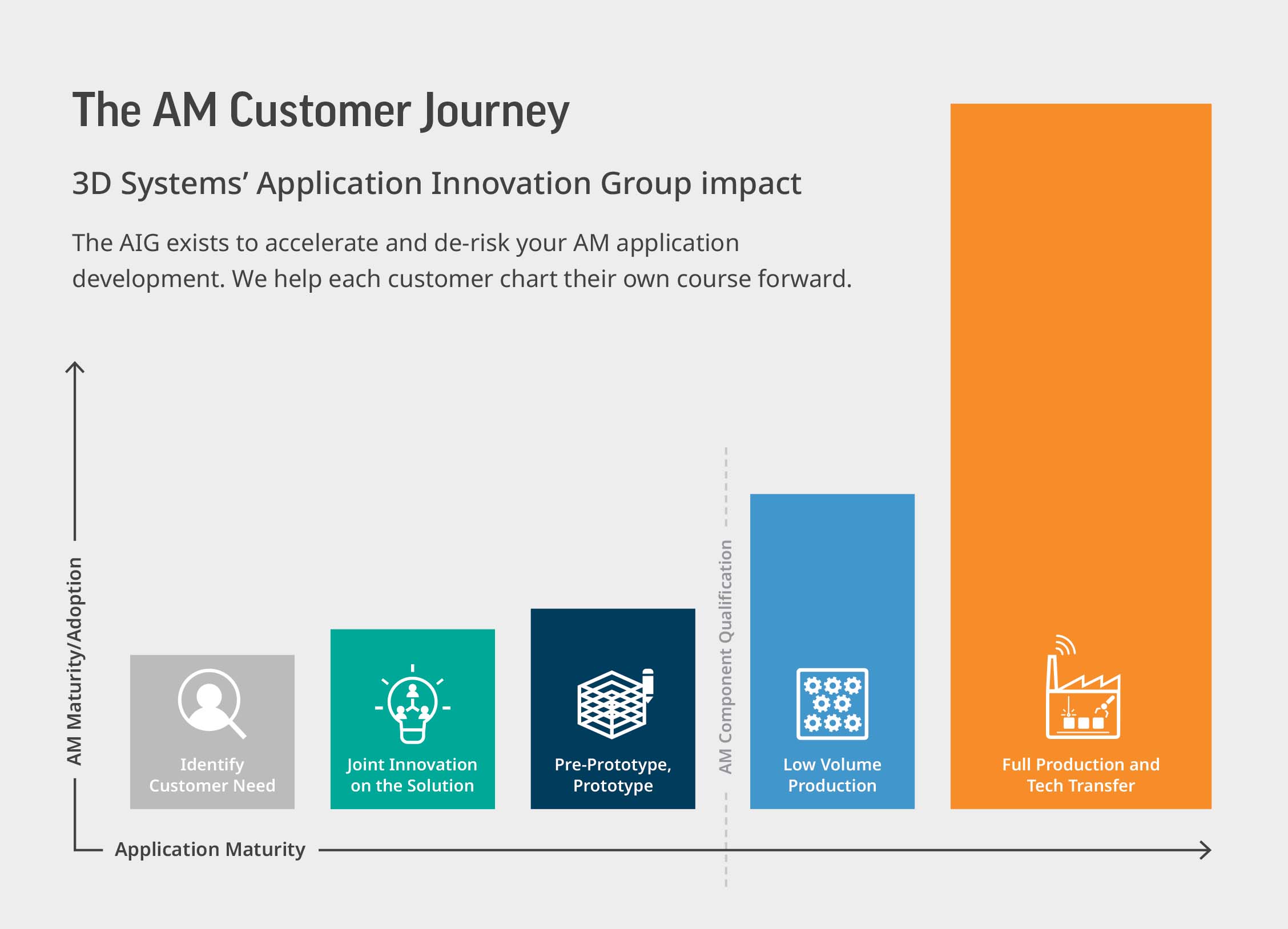
While 3D Systems has a well-defined model for its approach to healthcare innovation, each new project and customer brings unique challenges. The company’s team of experts—called the Application Innovation Group—collaborates with innovators to solve issues quickly, expediting the path to submission and beyond.
Today, additive manufacturing is becoming a preferred process for personalizing implants, partly because design engineers can create complex shapes and geometries that improve the performance of orthopaedic implants and, ultimately, help improve outcomes. With new multi-laser 3D printers, any orthopaedic device can be a candidate for additive manufacturing, including implants for knee and hip applications. Additionally, when combined with expertise and proven processes, additive manufacturing can decrease development time by supporting the ability to quickly iterate design and reduce device production costs.
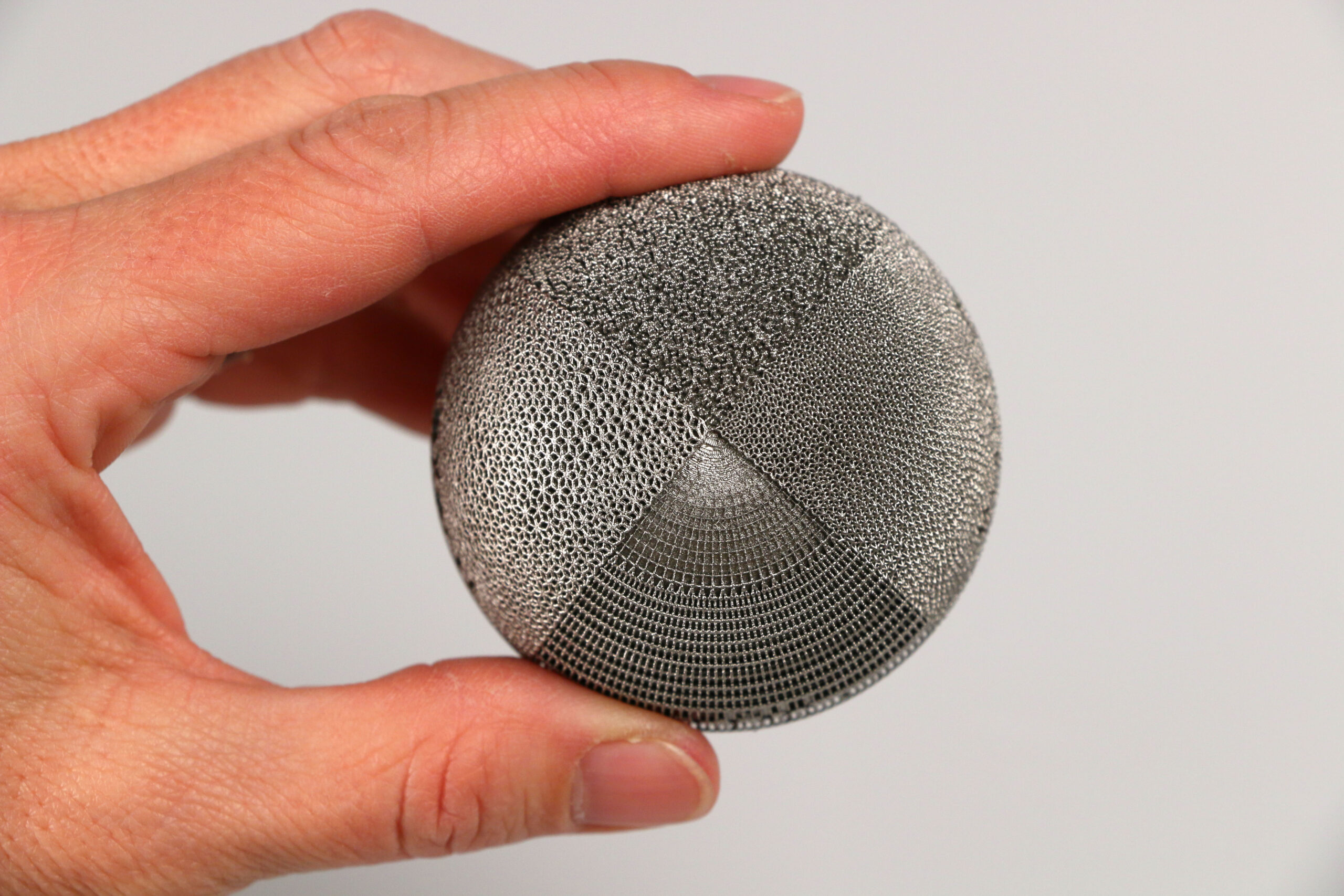
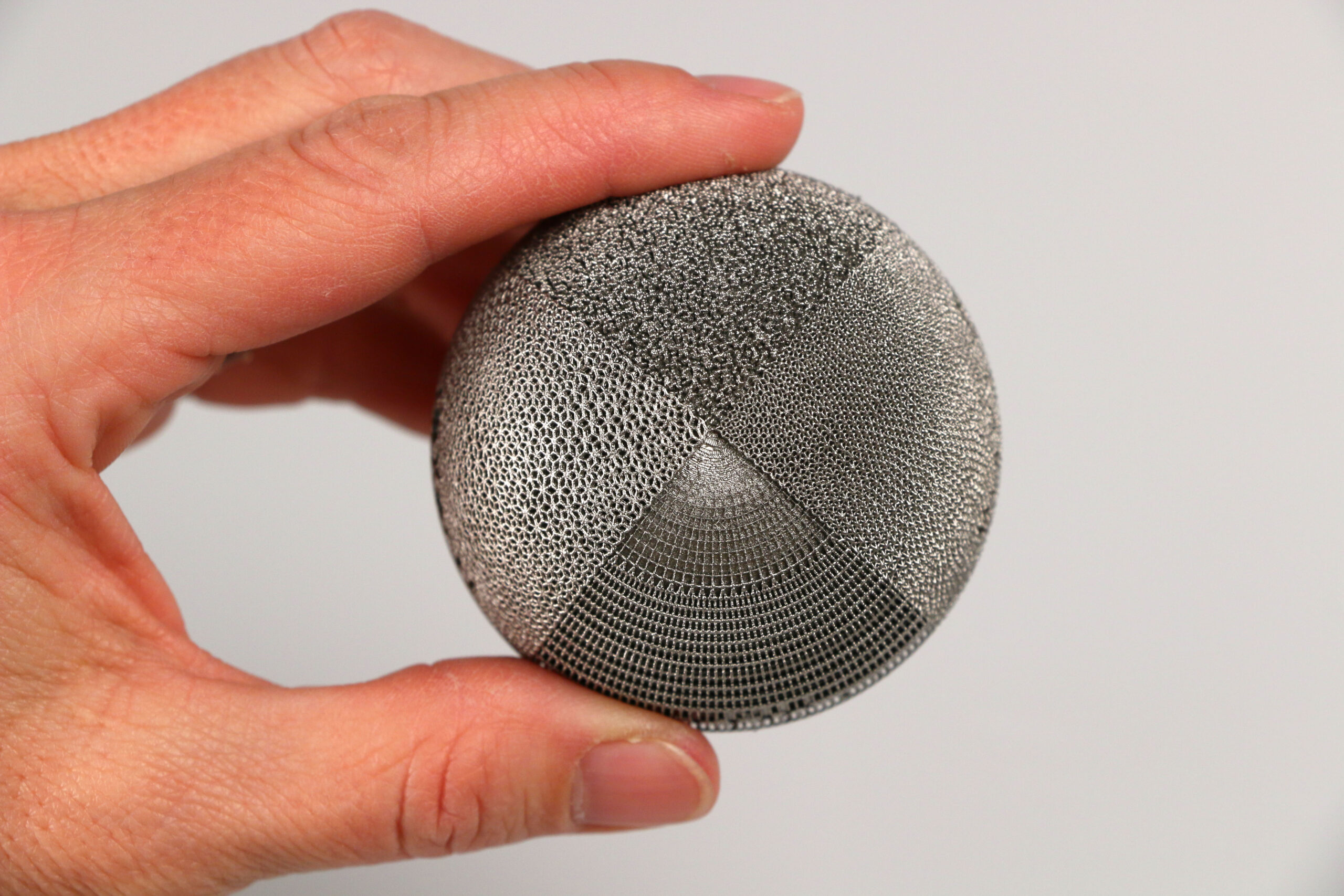
With new multi-laser 3D printers, any orthopaedic device can be a candidate for additive manufacturing, including implants for knee and hip applications.
Removing the Guesswork of Using AM in Orthopaedics
The path to market for orthopaedic device innovation is constrained by the complex and lengthy process of preparing it for FDA submission. 3D Systems is unique in the industry as both a contract manufacturer and user of its own material, software, hardware, and services. The company’s designers and engineers actively engage with in-house regulatory experts, who provide guidance on evidence needed to streamline reviews following submission.
Instead of calling in experts at different stages and from different organizations, innovators can leverage one team with experts who collaborate internally and stay on track with shared goals and objectives. That breadth of expertise is one more reason the AIG has had success moving innovations from ideation to validation so rapidly. From innovation and development to validation and production, the group’s vetted processes help innovators overcome technical challenges, optimize additive manufacturing design and workflows, employ state-of-the-art additive manufacturing-specific standards and quality practices, and bridge manufacturing so that applications can be ramped up at an appropriate pace.
For a more technical look into the ingenuity behind the materials and processes at 3D Systems, read the white paper, Titanium Process Capability Using Laser Powder Bed Fusion. It includes an extensive analysis of the validation and process characterization of titanium alloys for use in medical devices. When combined with the AIG’s approach to design, development and regulatory guidance for 3D printed devices, this workflow for metal implants helps further accelerate the path to market.
With over two million devices manufactured, more than 150,000 patent-specific cases delivered, and 100 plus FDA-cleared and CE-marked devices supported, 3D Systems has the experience and expertise that’s hard for any other company to match.
Ross Attardo is an Application Development Engineering Manager in the Application Innovation Group at 3D Systems. With nearly a decade as an engineer in 3D printing for healthcare, Attardo is now an expert consultant managing product realization with 3D Systems’ Application Innovation Group. Leveraging a wealth of knowledge through his previous roles at Johnson & Johnson, Attardo leads design, development, and production projects for diverse medical device applications, helping to ensure excellent quality and expeditious delivery. He is a Six Sigma Black Belt and holds a Bachelor of Science degree in Biomedical Engineering from Boston University.