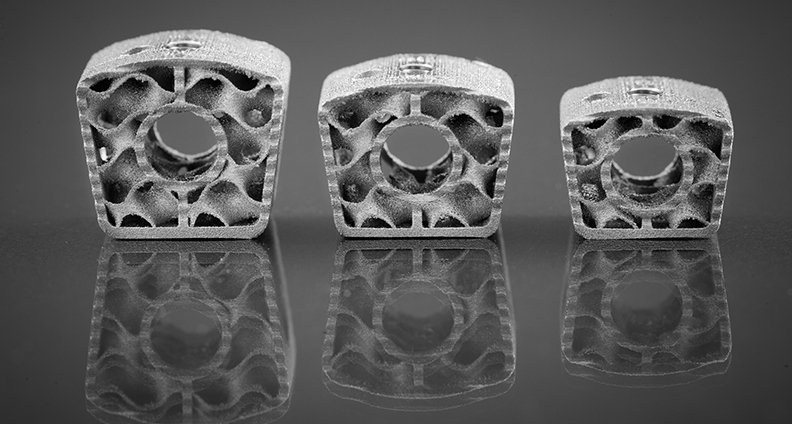
For years, and to this day, generic implants and surgical approaches for high-volume procedures have been the standard in orthopedics. But more and more, companies are looking toward patient-specific solutions that may provide better outcomes.
restor3d, a Durham, North Carolina-based medical device company and 3D printing manufacturer, is seeking to expand the delivery of 3D-printed personalized surgical solutions across multiple musculoskeletal specialties. They are also developing artificial intelligence (AI) and machine learning (ML) based software tools that will assist engineers with patient-specific implant design.
“The future of musculoskeletal surgery is personalized versus a one-size-fits-all approach, even in high volume procedures,” said Ken Gall, Ph.D., Co-founder of restor3d and a professor at Duke University. “Anatomy, physiology and kinematics, surgical approach, and patient factors are what restor3d is focused on in a quest to expand the reach of personalized musculoskeletal care.”
A Multi-Layered Path to Personalized Implants
restor3d has four foundational technology platforms: 3D printing, biomaterials, biomechanics and AI/ML software tools.
The spatially-varied porous nature of restor3d’s implants is known as TIDAL technology, a patented, optimized porous architecture that enables rapid digital design and manufacturing. TIDAL is optimized for osseointegration, with mesoscale pores that support graft retention and bony ingrowth, both key in the bridging of bone in a variety of orthopedic repairs.
“Our TIDAL Technology provides many advantages in 3D printing because of its high strength for a given porosity, combined with ease and speed of complex implant design and subsequent 3D printing,” Dr. Gall said. “This geometric pattern enables extreme flexibility in implant design and manufacturing orientation. Anatomically matched surfaces are easily approximated, and printing orientation dependency is minimized relative to other lattices by our competitors.”
The sheet-based architecture is additively manufactured using laser powder bed fusion of medical-grade titanium or cobalt chrome alloys.
In 2021, restor3d announced its merger with Kinos Medical, a total ankle replacement company. The KINOS total ankle arthroplasty product that has resulted replicates the kinematic profile of natural joints, with robust bone fixation features intended to improve stability.
restor3d uses AI to scale personalized medicine on both the manufacturing and design sides. By collecting data on completed surgeries, the company’s software tools aim to identify trends on what works best and can be replicated, or what may need adjustments. On the personalization side, the surgeon can use a CT scan to either design a patient specific implant or determine which implant from a list of predetermined FDA-cleared options are best suited for the parameters of the patient’s specific needs.
“Our materials, implants and products are based on extensive university research,” Dr. Gall said. “Our patented 3D-printed TIDAL materials and Kinos’ kinematic models are supported by a dozen published articles across benchtop and animal models. Our proprietary AI-based design tools are being developed in collaboration with leading university researchers in the fields of computer vision, computer graphics, medical imaging, image analysis and machine learning and we just published our first journal article in the space.”
restor3d offers personalized, patient-centered medicine in multiple specialties using expertise in biomaterials and biomechanics. Their onsite just-in-time manufacturing and post-processing of implants, instruments and anatomic models will allow them to quickly get product to market from a single source.
Upcoming Priorities
In early 2023, restor3d will move into a new facility in Research Triangle Park that will expand capabilities for patient-specific digital design and in-house manufacturing of implants and instruments, as well as surgeon training and education labs.
The company’s priorities will be new product introductions and enhanced 3D-printed personalized surgical solutions in the upper/lower extremity, spine, orthopedic oncology and trauma markets, as well as ongoing development of AI/ML-enabled software for surgical planning and implant design. They will also focus on fundamental research, preclinical and clinical studies, as well as expansion of the commercial team to support market traction across multiple market segments that benefit from personalized surgical solutions.
HT
Heather Tunstall is a BONEZONE Contributor.