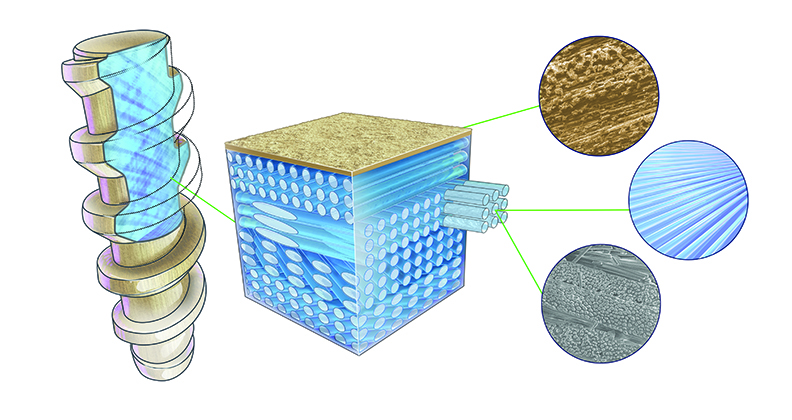
In recent decades, orthopedic companies have invested in research and commercialization of absorbable, resorbable and degradable biomaterials for trauma and sports medicine applications. The aim has been to replace the use of metal implants, often seen by these companies as a permanent solution to a temporary fixation problem. However, some novel materials lack weight-bearing strength or don’t fully absorb.
OSSIO, an orthopedic startup co-located in the U.S. and Israel, seeks to overcome challenges posed by metal and absorbable implants with its bio-integrative OSSIOfiber technology.
“We have created a new category in fixation materials,” said Brennan Marilla, Chief Commercial and Operating Officer for OSSIO. “What makes OSSIOfiber different is that the fibers are the secret sauce. …This is the first non-permanent, FDA-cleared implant that is stronger than cortical bone.”
Solving the Permanence Problem
OSSIO aims to provide non-permanent orthopedic fixation through natural bone healing. The goal is to eliminate the need for hardware removal, reduce implant complications and improve the healing process. OSSIOfiber is a platform technology used to create screws, pins and plates with what they call Intelligent Bone Regeneration Technology.
For applications in which patients need restored stability and mobility without a permanent medical intervention, such as fractures, it’s still most common to use materials that either remain in the body or need future surgical removal.
“One of the most common procedures in orthopedics is hardware removal,” Marilla said. “Elon Musk is going to put a human on Mars in the next 10 years, and we’re still implanting metal. There’s AI and robotics and regenerative medicine. And we’re putting metal screws and metal plates in people. Why?”
The benefit of metal implants lies within the strength and weight-bearing properties they have and the ease of insertion. But metal implants also result in permanent foreign material in the body or a second surgery to remove them. Polymer-based bioresorbable implants can often be too weak, according to Marilla. They can break on insertion or cannot bear the weight required in specific applications.
“We’re bringing to market a strong implant that surgeons can be confident will be inserted easily, just like metal, and it’s going to be weight-bearing, it’s going to hold the fracture, it’s going to hold the fusion, and then it’s going to go away very quietly and gently without them having to worry about it,” Marilla said.
A Platform Material
OSSIOfiber’s bio-integrative characteristics come from its novel makeup, 50% natural mineral fibers and 50% polymer.
“We take natural, continuous mineral fibers made out of minerals found in bone, including silica, calcium, magnesium, etc.,” Marilla said. “We layer them into a mold. We can layer them in different ways to dial in the mechanical properties that we might want, so we make a screw differently from a nail.”
The technology is a natural mineral fiber-based implant with a Poly (L-lactide-co-D,L-lactide) fiber-binder. OSSIOfiber provides the strength of metal with the biocompatibility and temporary existence of bioresorbable implants.
“We haven’t invented any new chemistry here,” he said. “The ingredients of OSSIOfiber have been around for 30 years in bone void filler. We just engineered them into a solid form that you can make fixation implants out of.”
During animal studies, human trials and their commercial experience of more than 6,000 implants, the OSSIO team has not seen evidence of their material leading to acidic reactions that create cysts, which can be a problem with polymers on the market. They’ve also witnessed exceptional weight-bearing performance.
Animal studies showed trabecular bone attachment to the OSSIOfiber implant within two weeks. Within six weeks, bone cells infiltrate the matrix-like fibers of the implant, the little polymer that is in the implant begins to degrade, and bone cells replace them. By one year, the polymer is completely gone.
“What happens is the underlying mineral fibers are just mineralizing and integrating into the bone,” Marilla said. “In our first in-human study, we have two years of data now; we have MRIs showing that the implant is gone, and there’s no fluid accumulation where the implant was.”
More recently, OSSIO completed animal studies on plates using their technology.
“We know what happens in bone, but we wanted to see what would happen on bone,” Marilla said. “When you put a plate on top of cortical bone, we wondered, is it going to leave a speed bump? What we saw over time was the plate just completely remodeled back down to the cortical surface, and there was no trace there was ever an implant.”
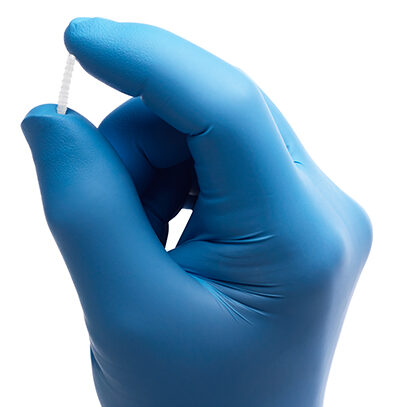
OSSIOfiber’s bio-integrative characteristics come from its novel makeup, 50% natural mineral fibers and 50% polymer.
Expanding Into New Areas
As a platform material, OSSIOfiber has potential in several applications. After starting with foot and ankle implants, the company is continuing to build out a portfolio of orthopedic implants that include upper and lower extremity products.
“We will enter the sports medicine business this year with a suture anchor that will be for both shoulder repair and Achilles repair,” Marilla said. “We recently received FDA clearance for the first non-permanent compression staple, which we will launch in late summer (2022).”
Marilla noted that the first FDA 510(k) clearance pathway wasn’t easy. But since then, the rest of the approvals have been relatively quick. OSSIO expects to launch a smaller compression screw this year and plans to get into more hand and wrist products, as well as specific labeling around pediatrics.
To scale their efforts, they are dramatically increasing manufacturing capacity at their Israel facility to stay ahead of growth.
OSSIO was granted a purchasing contract with Vizient in March 2022. The contract makes OSSIO products available at negotiated pricing for healthcare providers in Vizient’s group purchasing organization.
“It’s already helping us a lot,” Marilla said of the contract. “One of the biggest challenges in getting adoption, even with an innovative product like this, has been hospital access, especially during COVID. Value analysis committees didn’t meet, and they had other things they needed to focus on.
“It’s very hard for a company with a new product to get hospital approvals; we have 10 times the hospital approvals today than we had a year ago. Vizient is a big part of that.”
The biggest challenge now is maintaining focus with all of the opportunities in front of them.
“Sometimes strategy is what are you going to say no to versus say yes to,” Marilla said. “There are so many ideas coming at us, so many things we want to do. It’s tough to prioritize. We have to balance our spending between R&D and sales and marketing. We’re trying to bring a broader portfolio to market as fast as possible.”
HT
Heather Tunstall is a BONEZONE Contributor.