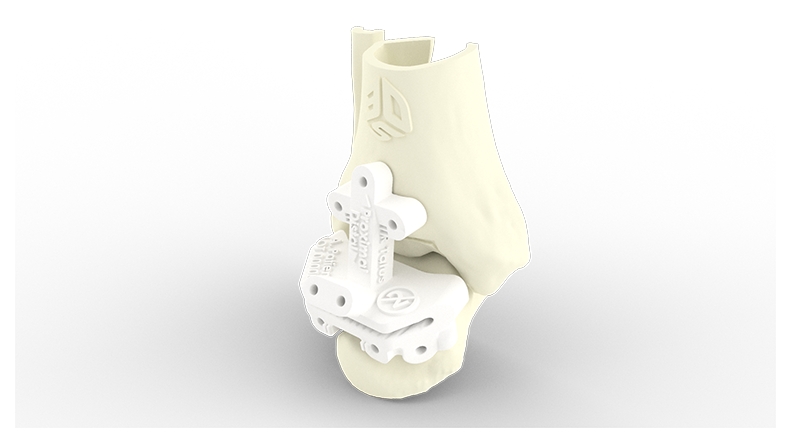
Importance of Testing Sterilization Methods on Materials used in Additive Manufacturing
Medical devices must be able to maintain all, or a high percentage, of their mechanical, dimensional and biocompatible properties after going through standard sterilization methods. However, this has not always been the case for traditional additive manufacturing (AM) materials, nor has information been available on the effects of common sterilization methods on AM materials.
We developed our healthcare materials to remain stable following sterilization, and then we put our polymers to the test to provide data on how well our materials maintain their properties. This due diligence is intended to provide guidance data to help manufacturers choose which material is best for prototypes, anatomic models, instrumentation and ultimately, for implants.
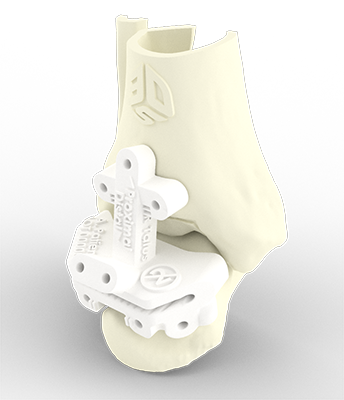
Vantage Ankle PSI uses DuraForm ProX® PA for anatomic models and instrumentation.
Material Properties Evaluated in Response to Sterilization
Several sterilization methods were applied to Figure 4®, VisiJet® and DuraForm® materials in our testing. We measured responses to autoclave, etO, gamma, e-beam sterilization, novel gas (vaporized peracetic acid) processes and recently reported the results in a white paper.
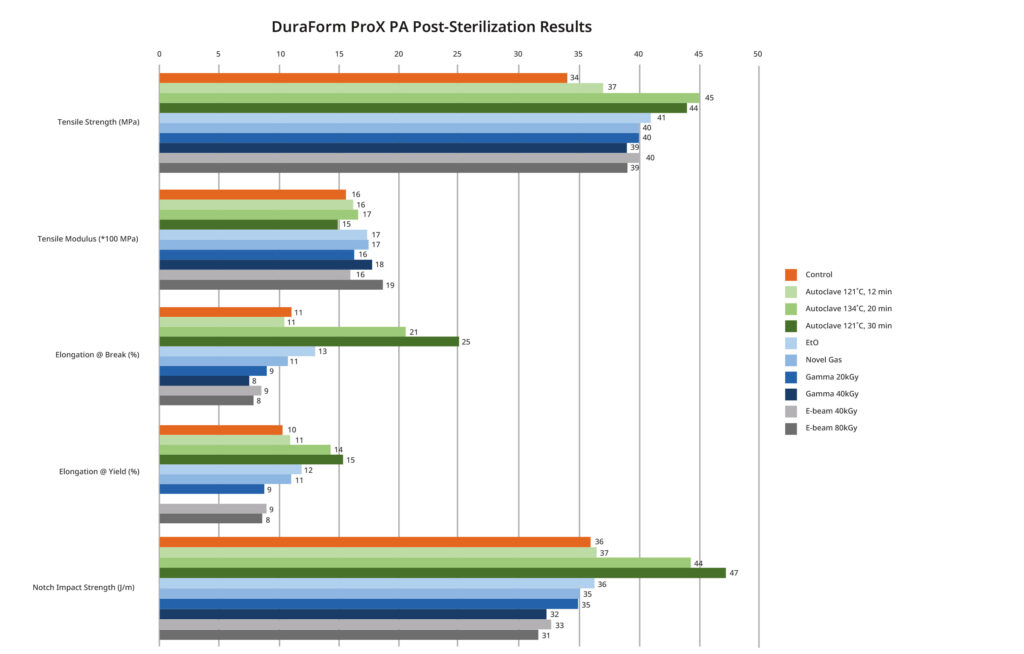
Sterilization results for DuraForm ProX® PA material used for ankle and CMF instrumentation. (Click to enlarge)
As part of our evaluation, we looked at several mechanical properties, as well as the aforementioned dimensional stability, color stability and cytotoxicity. It’s important to select a material for implants and instrumentation that will not degrade as a result of the sterilization process. That is why we measured and quantified the critical mechanical and dimensional values before and after each of these sterilization methods.
Next, we looked at color stability, to ensure that a white part does not appear stained, pinkish, tan or brown following these processes. Lastly, we tested cytotoxicity per the ISO 10993-5 standard to ensure that the materials maintain their biocompatibility and appropriateness for a broad range of medical applications.
Let’s dive a little deeper into dimensional stability. It is a critically important property to measure before and after sterilization. When putting a device through high temperatures and steam, for example, what does that process do to the device? In our tests, we looked at both the thin wall features and the more rigid, solid features to detect any distortion. Even for nominal variations, we recorded the percent change for each material following autoclave, gamma and other methods.
Materials responded to the tests differently for color stability. For instance, our Figure 4 Tough 60C White has excellent color stability, while our Figure 4 MED-AMB 10 material exhibited color changes. Others, such as the VisiJet M2R-WT, experienced color changes only after the high gamma sterilization method.
Finally, we conducted ASTM testing for the chemical compatibility for industrial cleaners. Sodium hypochlorite solutions often are used for cleaning and quick sanitizing in medical environments. We wanted to report how our materials handled that activity.
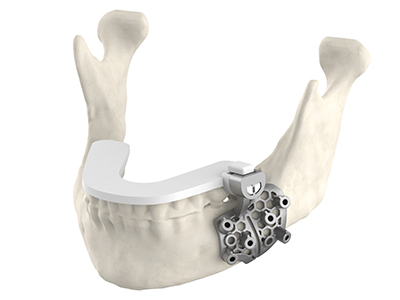
Maxillofacial hybrid guides incorporate DuraForm ProX® PA and LaserForm Ti Gr 23 (A) materials.
Additional Data Available to Help Choose the Right Material for a Particular Application
We understand the importance of having thorough data to effectively match a material to an application. The test data in our white paper “Common Sterilization Methods and 3D Systems’ Plastic 3D Printing Materials” is intended to help classify 3D Systems’ polymer materials as production-capable, clinical trial-capable or appropriate for functional prototyping based on the performance requirements of a medical device.
Martin Johnson is Director | Print Process, Technical Fellow at 3D Systems, Inc.