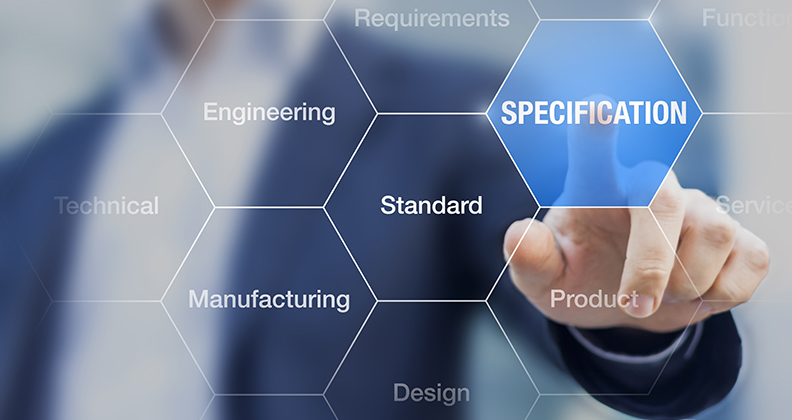
Orthopaedic products are designed to solve complex problems in the most efficient and cost-effective manner, improving the lives of physicians and the patients they serve. But with challenging issues and demanding regulations, it’s easy for OEMs and CMOs to see unanticipated increases in manufacturing costs.
While costs are frequently noticed in the initial manufacturing and production phases, the design is what sets the stage. It’s in the design phase where parts, features and tolerances that could cost more are determined. Unfortunately, those higher-cost choices often aren’t discovered until later in the process. And the farther along you are in the process, the more expensive it is to make a change.
When designing new products, here are 10 considerations to keep in mind. Depending on how you incorporate these elements, these design considerations could either increase your costs or, more ideally, reduce costs, lower lead times, and minimize difficult obstacles.
Consideration #1: Rigid vs. Flexible Design
A rigid design doesn’t allow room for changes as the project progresses. Rigid designs are more difficult to adjust and update throughout the process, and can unnecessarily increase costs. That can be a problem because many manufacturing partners can help lower costs with design for manufacturability support, but only if the design can be adjusted.
Suggestions from manufacturing partners often come from expert engineers with experience in designing and producing orthopaedic products. Their suggestions may include adjusting tolerances so machines can create the parts with standard tools. If the design can’t support the change, you’ll likely require custom tools that will increase your costs. Other suggestions may involve adjusting features to make them easier to inspect, a crucial element in orthopaedic design and production.
Consideration #2: Customization Needed for Overall Design and Individual Components
Custom components and products are in the nature of orthopaedics. You cannot solve a complex problem in a new way without a new design.
However, custom products, features, and parts are more expensive to produce. In most cases, this means that the more customization there is in a design, the greater the cost. Fortunately, new products and components don’t preclude the use of standard parts and features. For instance, designs that require multiple screws may be able to use the same screw in each location instead of three uniquely designed screws.
If there are places in your design where you can standardize or reuse parts, you’ll make it easier to source those parts and improve manufacturability. That will lower your overall costs.
Consideration #3: Feature Necessity
Some parts and products require large numbers of features, but every feature included in a design is a feature that needs to be created during the manufacturing phase. The more features, the greater the cost. If features need to be created on different machines with different tools, you’ll also increase the time it takes to create your piece. Simplifying a design will help reduce manufacturing costs, so design parts with only the features necessary to do the job.
Consideration #4: The Number of Parts within a Product
While not always avoidable, it’s worth noting that each part in a design needs to be created and assembled. The more parts you have, the more you increase your material, time and assembly needs. If you can decrease the number of parts required for your product, you will likely reduce costs as well as speed your time to market.
Consideration #5: Tolerances
Every zero you add to a tolerance magnifies your price. Tight tolerance features are more difficult to manufacture, often requiring specialty tools that are placed under greater strain and need to be replaced more often, driving up your costs.
Fortunately, it’s often possible to reduce tolerances while maintaining essential performance needs. Do a Tolerance Stack-Up Analysis to determine the cumulative effect of feature tolerances on assembly needs and adjust where possible.
Consideration #6: Inspection Requirements
Compliance is a major hurdle in orthopaedics, with regulations becoming more and more complex. Often times, it is the inspection phase that causes delays and sends designs back for revision. There are three common inspection-related issues that could increase your costs.
- Creating a feature that cannot be reached for inspection. Just because a feature can be created in design software, or even by a CNC machine, does not mean it can be properly inspected. If the feature cannot be inspected, you lose time and money sending the design back for updates.
- Designing without features or reference points that can be used to hold the part during inspection. Adding these features or creating a unique inspection process to overcome this limitation will increase costs.
- Requiring sophisticated inspection equipment to inspect features instead of simpler, cost-effective options like hand gauges. The more complex the equipment, the higher the costs.
Inspection technology is evolving rapidly, with advances that can significantly improve inspection processes. To ensure the most cost-effective inspection, talk with your manufacturing partner about the equipment at their disposal. Ask how the machines, manpower and time requirements to inspect your product will affect costs. In many cases, zero touch inspection technology can significantly reduce manufacturing time and increase consistency.
Consideration #7: Standard vs. Specialty Materials
Specialty materials are more expensive. Use standard materials where possible, and if you must use a specialty material, be as efficient as possible. Manufacturing process experts should be able to help you optimize designs and choose production methods that minimize scrap, so you get more from the material you purchase.
Consideration #8: Incorporating Specialty Processes
Similar to the challenges and costs associated with specialty material, designers should avoid specialty processes and monopolistic coatings if possible. These can prove costly and add significant lead time to your project. When specialty processes are necessary, make sure to carefully weigh the advantages and disadvantages to ensure the benefits outweigh the risks.
Consideration #9: The Machining Processes Needed to Create Each Feature
Some manufacturing processes cost more than others. For example, features that are created using EDM processes are typically much more time consuming and costly than features that can be created by machining processes like CNC milling. When possible, design with features that can be produced through less expensive machining processes.
Consideration #10: Consider Manufacturing Requirements During the Design Phase
Not designing for manufacturability early in the new product development cycle is one of the biggest design issues that results in higher costs. Whether that’s adding unnecessary customization or not accounting for inspection needs, design for manufacturability has a significant impact on your project’s manufacturing expenses.
To incorporate design for manufacturability principles, teams need an in-depth understanding of manufacturing processes. If that expertise isn’t available in-house, consider working with your manufacturing partner to improve your results. The best manufacturers have design and process engineers on staff. They can work as an extension of your team to review designs and suggest changes that will decrease costs and improve your time to market.
Brian Rosenkranz is an Engineering Manager at Paragon Medical.