
The manufacturing of orthopedic implants such as femur-knees or tibia tray components is still characterized by a high degree of manual interaction from machine operators due to setup work for a specific part family and size. The work typically results in higher machining costs per component due to decreased productivity and more process steps. Additionally, each step must be documented before moving parts along the production chain.
The objective to increase productivity and lower per part cost becomes an even greater challenge when attempting to accurately predict on-demand manufacturing, which continues to rise in complexity.
Schütte Schleiftechnik has set out to create a new approach in manufacturing orthopedic components that start with a casted part. The goal is to minimize human interaction with the machine tool and increase automation flexibility to the point of having little to no restrictions in terms of component handling and manufacturing. The approach includes further process steps that are, as of yet, unthought of in orthopedic manufacturing.
Automating Orthopedic Manufacturing Steps
Another typical characteristic of the current orthopedic manufacturing production chain is the process design materializing as solitary improvements or island solutions. These include a flowing combination of interdisciplinary steps such as grinding, milling and metrology with active feedback into the manufacturing process. Abrasive belting, polishing and documentation of each step into one or fewer steps is now within reach.
A new automated approach provides a total capacity of 12 logistic trays stored in a parts loader protected from unauthorized access. The capacity of each tray accommodates up to 16 castings, where parts can simply be placed onto the tray with a focus on ergonomics. The pertinent information of each batch, like part size and number of parts in the order, can be either fed into the system via barcode or RFID chip. The system then automatically moves the trays from the load port to a camera station for size verification and part orientation on the tray. These 12 logistic trays may carry up to 12 different part sizes for consecutive processing without the need for additional human interaction. Automation of these steps facilitates real, on-demand unattended production for hours.
Part clamping fixtures for the grinding and milling operations are secured in a shelf located in the loader unit and monitored by sensors. The system management is designed to load the defined clamping fixture as the workflow requires, and to avoid mismatch errors. This is accomplished with a separate RFID tag on the clamping fixture itself. Part programs, tools and all workpiece components are managed with high efficiency in the number of repetitions called for by the batch assigned.
An automated station for fastening parts directly onto the fixtures can securely clamp all variants of parts, for example, femoral knee castings. Whether the knee is with or without the option to clamp onto a pin, the station can secure the part to the fixture. Part specific sizes or requirements for different clamping pressures aren’t posing restrictions either, as each recipe is individualized, learned and stored in the system control.
Once the workpieces are loaded into the WU335Linear grinder, the machining begins by probing each component location individually. To increase the productivity of the machining process, the system can load and machine two workpieces clamped side by side to eliminate unnecessary tool changes representative of a single part fixture, reducing cycle time. The external wheel changer has the capacity to store not only the necessary grinding, milling and abrasive belting heads covering the diversity of the scheduled parts, but also replacement tools. An inbuilt counter in the SIGSpro software provides an active tool life manager to exchange worn out tools automatically.
The machining process is challenged by the aim to rapidly machine NURBS (Non-uniform rational B-Splines) defined surfaces in the lowest time and with the highest accuracy possible. The machine tool must operate with the highest dynamic performance during many repetitions without compromising the given part surface topology. To provide accuracy with high velocity profile grinding, Schütte recommends its linear drive technology. This technology has subsequently eliminated several common wear parts, such as ball screws from the machine tool.
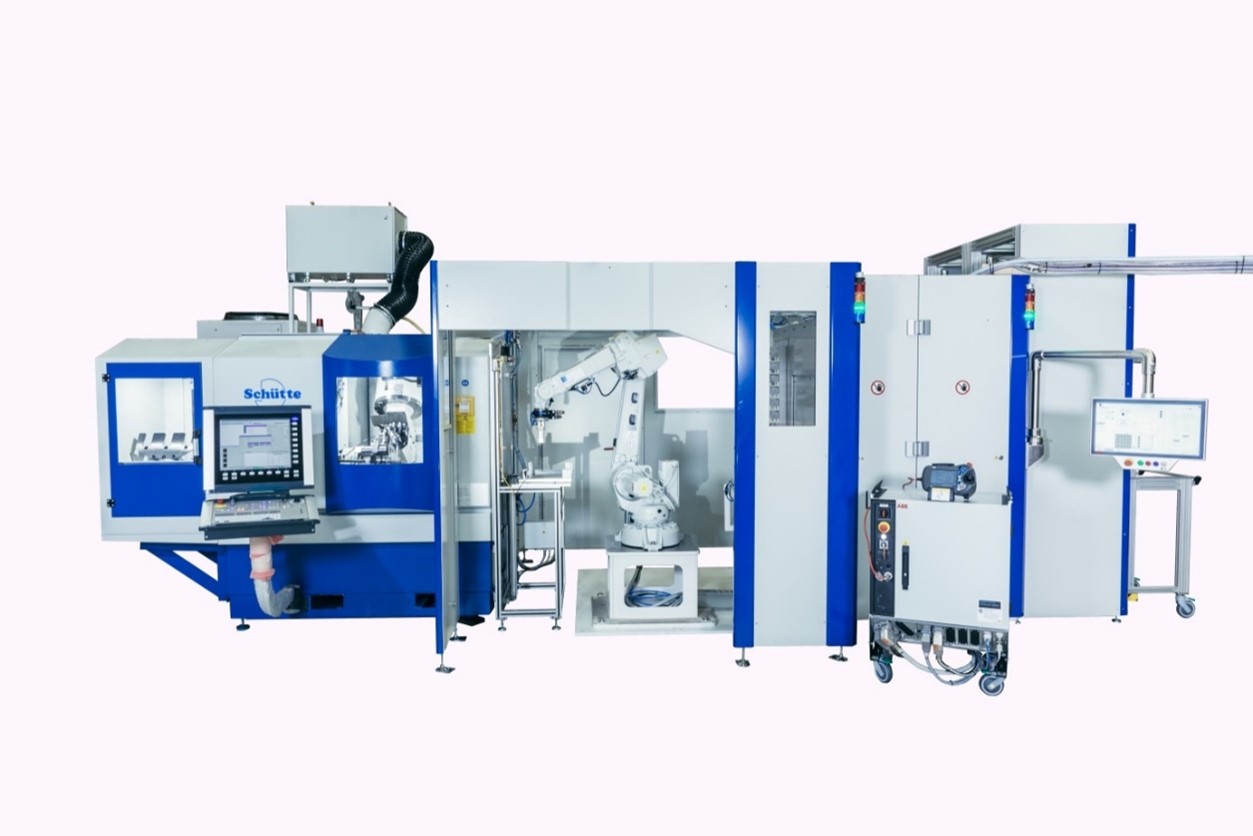
Schütte’s goal is to minimize human interaction with the machine tool and increase automation flexibility to the point of having little to no restrictions in terms of component handling and manufacturing.
Programming the Manufacturing Process
The source entry data required to compile and post-process a complex NC-program comes from a CAD/CAM system, translating the NURBS surfaces into many thousands of data blocks in the form of point and vector information. These trajectories are simply imported by a mouse click into the SIGSpro software and turned into an NC-program without the need to apply the skill of programming for the responsible technician. The machining cycle can be simulated and verified prior to production to ensure that the NC-program and part geometry match the design requirements.
The software integration provides a closed-loop work platform to conduct the engineering work, including simulation, offline and away from the machine environment. Additionally, the ability to store settings made in the program, such as feeds and speeds in an offline environment, helps avoid losing critical data in the program.
Going Beyond Manufacturing
After machining, manufactured parts and clamping fixtures undergo a cleaning cycle to avoid contamination from grinding and milling chips or oil compromising the firm process accuracy. The robot then places the machined parts back onto the logistic tray, and the process as scheduled continues. However, this may not be the end of the story.
The entire system, comprising machine tools, a robotic loader and a cleaning system, follows the concept of an open platform architecture. The system is made to grow in one leap or in single steps to provide stability for the process without sacrificing the flexibility to deliver what the order book demands.
Thomas Simmich is Sales and Technical Consultation for Schütte Schleiftechnik. For more information, you can contact Matt Morgan by email or phone, 517-812-4484.