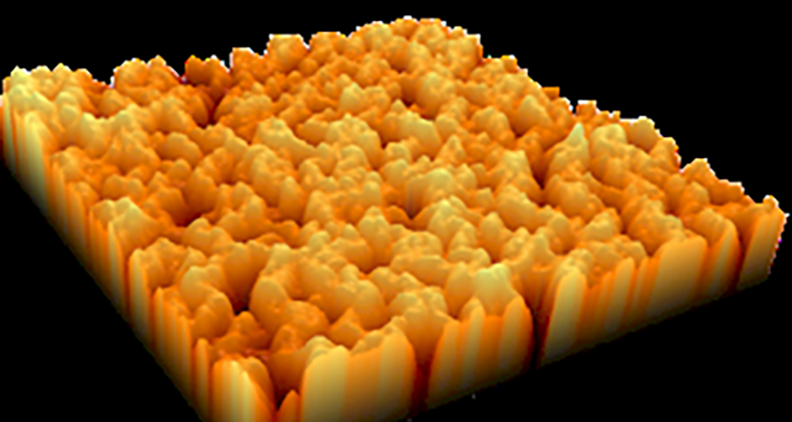
Total joint replacements are expected to continue growing long-term as the population expands and ages, and technology continues to improve. According to a study published in The Journal of Rheumatology, researchers predict that annual counts of total hip replacement in the U.S. alone may increase from about 498,000 replacements in 2020 to 1,429,000 replacements by 2040.
Total knee replacement is expected to reach 3,416,000 replacements in the U.S. by 2040. Worldwide, the joint replacement market was valued at $17.1 billion in 2020 and is expected to expand to more than $21.5 billion by 2023, according to ORTHOWORLD Inc.
Hip replacements have a revision rate of around 4.7% at final follow-up, while knee replacements have a 3.7% revision rate at final follow-up, according to the American Joint Replacement Registry 2021 Annual Report. The enormity of the market, coupled with the revision rate, shows that there is room for improvement in joint replacement.
Addressing Joint Replacement Failures with Nanotexturing
Two major risk factors and failure points in joint replacement are bacterial infection and wear. Vallum Corporation has developed Accelerated Neutral Atom Beam (ANAB) technology and processing protocols to address both.
The technology, NanoGlide, uses accelerated argon atoms to remove 20-50 nanometers from the surface of a manufactured polyethylene orthopedic insert. A nanotexture is created that does not affect the dimensions, design or chemistry of the device. The process is called subtractive nanotexturing, and it lies at the core of NanoGlide technology.
“We change the topography of the insert, which changes the physical characteristics that have some impact on attracting and absorbing proteins,” said Stephen M. Blinn, President and CEO of Vallum. “We also change the actual surface energy a bit, which is beneficial in attracting certain types of glycoproteins. We attract lubricin, mucin and casein.”
When the implant’s surface energy is changed using nanotexturing, the revised energy becomes nearly identical to the surface energies of the three proteins, which attract them to the implant surface. It’s the attraction of these glycoproteins that makes the difference in terms of joint replacement infection and wear.
Lubricin is a natural protein that the body absorbs into cartilage to give joints lubricity, making properly functioning joints almost frictionless. In traditional joint replacements, there is no cartilage and polyethylene implants do not attract lubricin, and may in fact get in the way of natural lubrication.
“Once we put NanoGlide on the surface of the polyethylene, all of a sudden, you now have nine times the amount of lubricin being absorbed into the surface. So now you have a natural lubricant, which dramatically reduces wear,” Blinn said. “We call it NanoGlide intentionally because of the natural lubrication. If you distill it down to its pure essence, this is going to be an implant, whether in the shoulder, the hip or the knee, that attracts lubricin.”
Lubricin is also a natural antimicrobial, so while it reduces wear, it also makes the implant’s surface more resistant to infection. The other two proteins that NanoGlide technology attracts, mucin and casein, are more beneficial in terms of antimicrobial roles.
Bacteria do not typically adhere to surfaces when casein is present. Mucin, on the other hand, is absorbed into the surface of the implant. If bacteria gets on the surface and attaches itself, the mucin interferes with the bacteria’s signaling complex. This action ultimately prevents the component from developing biofilm.
“We’ve got a triple punch for antimicrobial,” Blinn said. “Lubricin, mucin and casein all work as an antimicrobial. Lubricin, in particular, also works as a lubricant.”
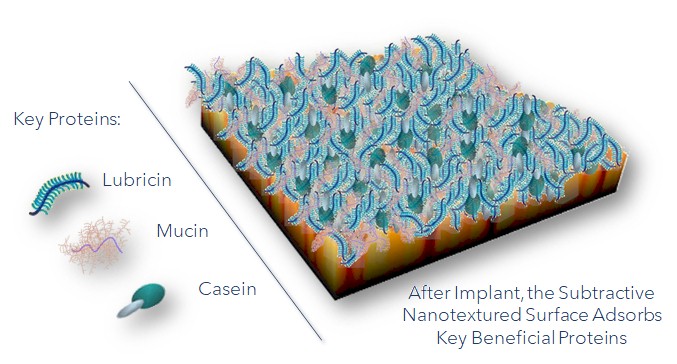
When the implant’s surface energy is changed using nanotexturing, the revised energy becomes nearly identical to the surface energies of three key proteins, which attract them to the implant surface.
A Manufacturing Solution for Nanotexturing
Vallum started using ANAB to subtractively nanotexture PEEK spinal applications back in 2019, seeing excellent results. As the spine market shifted away from PEEK and toward titanium, Vallum began applying the technology to polyethylene orthopedic inserts and likewise saw great results in vitro.
Tibial inserts for knee replacements, acetabular cup liners for hip replacements and glenoid and humeral inserts for shoulder replacements often use polyethylene. The nexus of wear and infection is frequently the polyethylene, because it has no inherent qualities that attract biological materials that are lubricants or antimicrobial. Vallum’s in vitro studies have shown that the NanoGlide subtractive nanotexturing reduces wear and bacterial attachment.
“We have statistical significance across all of the major bacterial species that would cause infections in these implants,” Blinn said. “Ssecondarily, when you look at wear, we’ve shown with highly cross-linked polyethylene that we have a statistical significance at two million cycles of accelerated wear, that we reduce wear almost to nothing.”
During ANAB, atoms are accelerated to tens of thousands of miles per hour. In a single square millimeter, about a quintillion atoms strike the surface, releasing thermal kinetic energy. Because polyethylene is an organic material, the heat generated by the kinetic energy ablates the material within the strike zone, turning it into gas.
The process is done within a vacuum chamber. The gas is removed by vacuum, and a virgin surface is left. The surface is exactly like the original surface, but is now dotted with concavities similar to dimples on a golf ball, but at a much, much smaller scale.
ANAB is repeatable, robust and has been around for quite a few years, indicating that it is well-developed and vetted in the marketplace. The technology was originally used for microdevices and even in the semiconductor industry, where requirements were orders of magnitude more specific than what’s used for medical devices. Vallum has licensed the technology and has exclusive rights to it for all medical applications.
The beauty in the approach is that the process is applied to a fully manufactured insert without changing its functionality. That’s a significant departure from traditional technologies that require a manufacturer to either come up with a new product or dramatically change their current product offerings, which may introduce technical and clinical risk.
The processor that applies the NanoGlide technology to devices is a seamless, plug-and-play addition to the manufacturing process. It can either be put at the end of a production line at the manufacturing facility, or it can be treated after the fact.
“You can take a low-level technician, and they can operate it because it is all computer controlled and has a complete history of all parts being processed,” Blinn said.
Rather than approaching joint replacement wear and infection by applying coatings, Vallum’s NanoGlide technology aims to be a seamless process to be used on products as a final step in production without introducing additional risk.
“In this case, the thickness of some of these components are eight to 11 millimeters (or 8 million to 11 million nanometers) thick,” Blinn said. “We are simply removing about 20-50 nanometers from the surface to make a nano texture, so it has zero effect on the dimensions and design. It just changes the topographical feature in a way that’s really beneficial.”
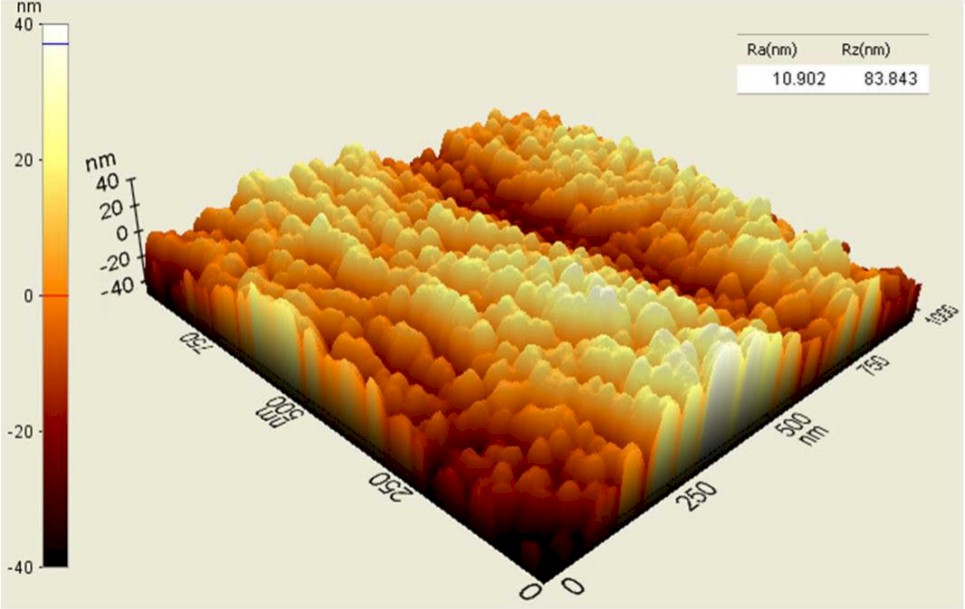
Unprocessed Polyethylene (top) vs. Processed Polyethylene (bottom)
Next Steps for NanoGlide
Vallum has established in vitro evidence and is now looking for a partner in orthopedics to move into animal studies to establish the anti-wear and antibacterial properties of a device in vivo. From there, they hope to file with the FDA for 510(k) clearance for the NanGlide subtractive nanotexturing process, starting first with the anti-wear claim, followed by the antibacterial claim following additional studies. Vallum plans for a limited rollout to collect human clinical data upon FDA clearance.
Securing an investment will allow Vallum to move into accelerated wear testing with a device and antimicrobial testing. Blinn estimates that from the time they enter into a partnership, they will have a product ready for commercialization within 15 months.
HT
Heather Tunstall is a BONEZONE Contributor.