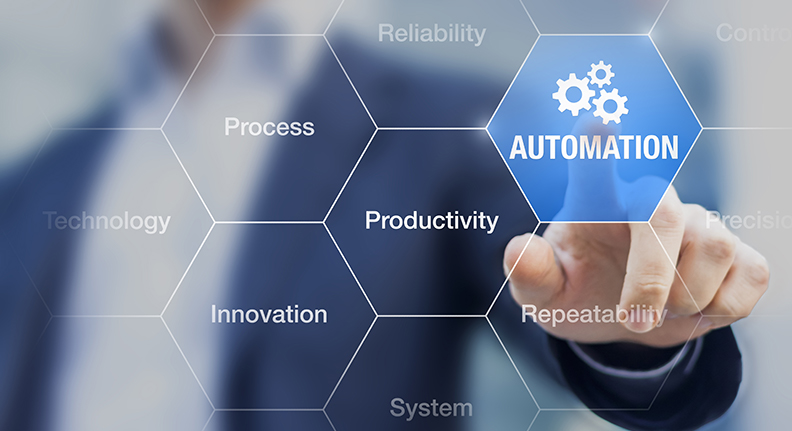
For decades, automation has been a key manufacturing initiative, resulting in significant efficiency, cost, and product consistency gains. However, it tends to be more widespread outside of the orthopaedic market, in industries like automotive and heavy trucking that work with high volumes and relatively low part mix.
Automation is less widespread in orthopaedics due to the inherent challenges of applying and scaling automation across projects. Unlike other industries, orthopaedics often creates low volume, high mix environments in which fewer parts need to be manufactured in a greater diversity of sizes and orientations. Low volumes can make automation less cost effective, while variations in part sizes and orientations often increase the complexity of the automated programs.
This is particularly true for orthopaedic implant and instrument manufacturing, which frequently incorporates full product families. Knee implants, for example, must be manufactured in two orientations, right and left, to support each leg. Both the right and left knee implants must then be manufactured in 20 sizes to ensure surgeons have implants that are suitable for a range of human bodies, from small children to large adults. Combined with volumes that are often between 50 and several hundred pieces, applying automation that results in real-world gains becomes challenging.
To determine whether automation could be beneficial, orthopaedic OEMs and contract manufacturers must evaluate the complexity of their environments, as well as where automation may fit in the process. To be effective, automation in low volume, high mix orthopaedic environments needs to encompass multiple part sizes and part numbers. Manufacturers with the expertise to implement such programs can see significant results.
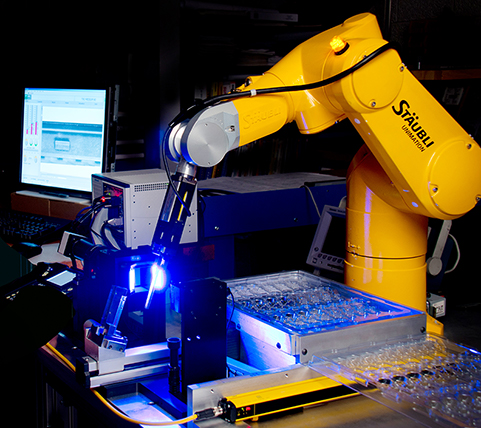
Robotic Automation
Types of Automation Used in Orthopaedics
The most common type of automation found within orthopaedic manufacturing is robotics. Robots are highly versatile and are used for loading and unloading bar stock, inspection, painting, welding, polishing, and more. Once finished with one project, robots are easy to repurpose, making them more cost-effective in low-volume environments.
Palletized systems can also be beneficial in orthopaedics. In many cases, palletized systems are performed with robotics, but they can be implemented through other automated programs.
Benefits of Automation in Orthopaedic Manufacturing
When implemented correctly, automation can result in multiple benefits for orthopaedic manufacturers, including improvements in efficiency, consistency, and cost. The real-world benefits will differ based on application, but can have far-reaching impacts for both the manufacturer and their customers.
Efficiency & Labor Gains
Automated processes increase efficiency by reducing manufacturing time and increasing output. Robots don’t need to take breaks or switch shifts, making lights-out production a possibility. In most cases, automation will increase efficiency by 10% to 15%.
As automation takes the place of human workers, manufacturers can also partly offset one of the industry’s biggest challenges – a shortage of skilled labor. Manufacturers in all industries have faced difficulties in recruiting that have only increased in recent years. And, despite the push to encourage more young professionals to pursue manufacturing careers, it’s unlikely that the labor pool will see significant growth in the near future.
As manufacturers look for ways to expand their capacity without hiring more people, automation is coming to the forefront. We regularly see a 30% reduction in labor needs with the right automated processes. For example, a manual process may require one technician per one to two machines. With automation, that same technician can handle between four and six machines, freeing up skilled labor to support critical projects and production requirements.
Consistency & Inspection Improvements
The potential for error increases any time a human is involved in a process. That error decreases as automated processes replace manual work, improving product consistency. This is especially true when it comes to inspections. Inspections that are 100% automated save time and ensure the consistency of every individual piece produced. They also create instantly digitized records, replacing the hard copies that are still used in many orthopaedic environments.
As technology improves, we continue to see advancements in automated inspections. Blue light scanning technology, for instance, now offers a touchless inspection method that places tolerances on parts and provides a heat map that evaluates each feature’s size and shape. The inspection sorts accepted and rejected products, significantly reducing inspection time.
Cost & Scrap Reduction
Depending on the process, automation may even translate to cost savings by reducing scrap. We see this benefit most often when automated inspections occur near the front end of a process. For example, an automated program can take a part from a CNC machine, then put it into an inspective device, such as an Equator, for measurement. If the Equator is interfaced directly with the CNC machine, then it can adjust the CNC offset based on the part’s measurements, ensuring it is within print tolerance. Coupled with the ability to automatically adjust the machine offset, this type of in-process inspection provides improved process capability and reduces the number of rejected parts, resulting in lower scrap volumes. For high-value materials such as the titanium and cobalt chrome used in implant manufacturing, this can translate to significant cost savings.
Automation requires an initial investment that can be taken on by manufacturers directly or shared between contract manufacturers and their customers. In today’s market, it’s common for automation to be left out of initial discussions between manufacturers and customers. However, with the increasing shift toward automation even in challenging low volume, high mix environments, orthopaedic companies can expect to see automation included in quotes more and more frequently.
An effective automation program will pay for itself within a year, then produce consistent cost savings through labor reduction and increased output. Robotics, in particular, can result in long-term cost savings due to their high uptime and versatility. An effective robot can function for up to 20 years with minimal maintenance, making it an easy and cost-effective tool to repurpose for different projects. Those robots can also help provide a 30% improvement in output.
Advancements in Automation Technology
The challenges of effectively implementing automation in low volume, high mix environments make it essential to carefully evaluate the manufacturing processes used, the products being manufactured, and the areas where automation may be a good fit. Manufacturers with a knowledgeable automation team, especially those with experience in implant and instrument manufacturing, are most likely to see the greatest benefits.
We expect to see automation continue to evolve and become more widespread in orthopaedic manufacturing. Advancements in laser technology are already assisting in measurements, such as welding measurements, and efficiency for many environments. Wireless communication between sensors is also evolving to provide more capabilities for machines with moving devices. There’s even a strong possibility that we’ll see the industry’s hottest trend, additive manufacturing, converge with automation because automation frequently supports secondary services for 3D-printed parts. In this area, it is the contract manufacturers with expertise in both additive manufacturing and automation that are best positioned to support customers as the industry evolves.
In the future, automation will likely become standard. It may also be included in design for manufacturability consulting from contract manufacturers and other related support services for projects. Orthopaedic manufacturing teams that build a foundation now will set themselves up as strong competitors in the marketplace.
Jason Wolfe is Senior Engineering Manager at Paragon Medical.