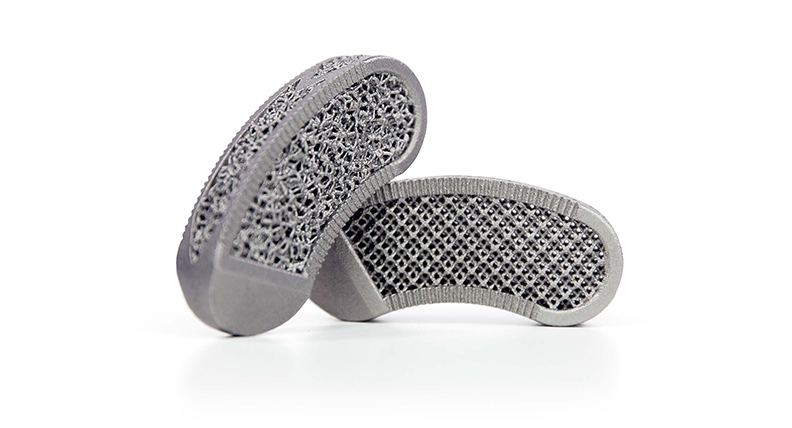
Innovation in healthcare is driven by new technologies that provide solutions to clinical care. One of these is additive manufacturing (AM), which is now being used across a range of applications as an unparalleled catalyst for innovation. Once a novel way for design engineers to prototype parts, AM has now become part of the manufacturing process used to fabricate millions of medical devices and healthcare products every year.
At its current rate of evolution, it is a safe bet that AM will be the manufacturing tool of choice for medical implants and instruments in the next five to ten years. To better understand how, it is important to know where AM stands today, why change is happening, and who is leading this transition.
Current State of AM Adoption and Development
Beyond increased awareness and applications for AM, use of the technology is growing as capabilities expand to enable higher volume production. Our industry-wide focus on productivity has led to the introduction of new printers specially engineered to deliver faster print speeds and throughput while maintaining the same high-quality output. And it is not just hardware that is advancing. Software platforms are also becoming more sophisticated and lowering hurdles to adoption by providing the digital infrastructure necessary to make traceability and compliance easier.
Innovation in patient-specific instruments and implants is another trend driving the adoption of AM. Personalized treatment options have a strong track record for use in complex surgical cases, and they are now being employed more broadly in the operating room where the use of a patient-specific device can save time and provide equally good or better outcomes. Because AM enables cost-effective, low volume production in a batch style of manufacturing, it is well-suited for effective personalized solutions.
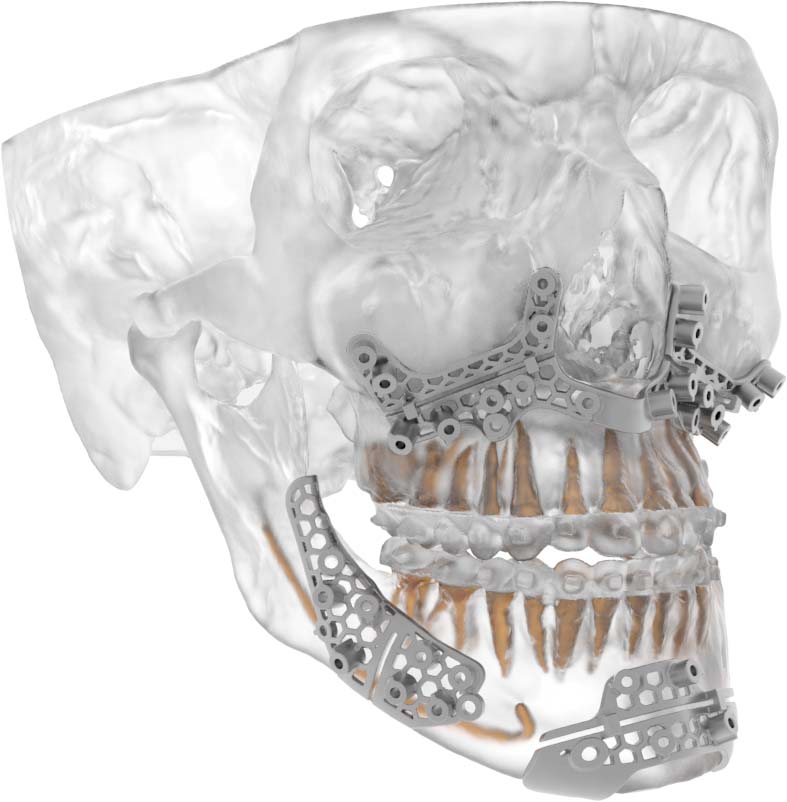
VSP Titanium Osteotomy Guides
The impact of these advancements is overwhelmingly positive, since more productive printers and processes means reduced costs overall. This, in turn, leads to more opportunities for additive manufacturing to drive innovation. Companies like 3D Systems are at the forefront of these changes, with more than three decades of experience providing industry-leading solutions. To date, 3D Systems alone has manufactured over two million medical devices, planned over 140,000 patient cases, and supported the development of over 100 products from concept through regulatory clearance and commercialization.
The Importance of Materials
A remaining variable in the equation is materials. When additive manufacturing was first introduced and primarily used for rapid prototyping, users accepted materials that demonstrated capabilities similar to traditionally used materials, in spite of differences in chemistry. In other words, a prototyping application could use a prototype material.
For production applications, however, the standards are far more stringent. Accordingly, as AM technology and applications have advanced, there has been a transformation in materials. 3D Systems has introduced AM materials that match the mechanical, chemical, biocompatibility and sterilization capabilities needed for final products. In metals, 3D Systems has seen tremendous success with the ability of its equipment to deliver products that meet or exceed ASTM requirements for commonly used titanium alloys, stainless steels and cobalt chrome. In plastics, the company’s nylon and acrylate materials are used to create patient-specific instruments for short-duration use. New developments and testing are continually underway to expand AM materials in both performance and variety.
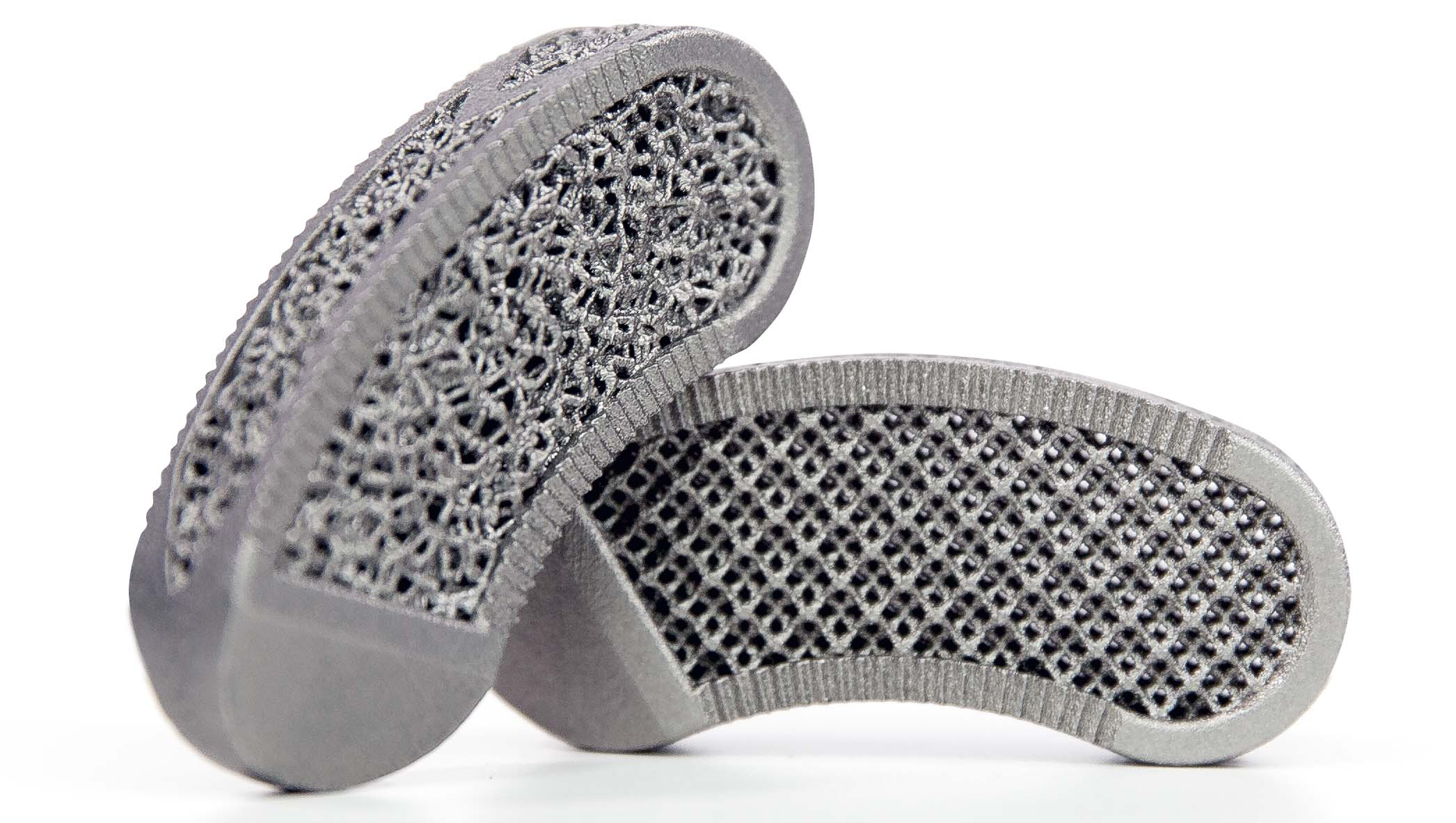
Interbody Fusion Device
Collaboration Drives Innovation
With device manufacturers constantly on the lookout for ways to foster innovation within their product lines, additive manufacturing is a welcome tool in the toolbox. Yet because no one understands the technology quite like the ones developing it, additive manufacturing solutions companies are invaluable for guidance. 3D Systems has organized its resources to help its customers meet these challenges through its Application Innovation Group (AIG), a team of engineers with deep expertise in 3D printing processes and experience developing industry-specific solutions. The AIG team partners with device manufacturers and plays an important role in the development and validation of new products. 3D Systems’ expertise includes engineering, quality systems and the regulatory know-how that the company has developed over the last several decades.
To give device manufacturers a flexible approach to capitalizing on AM, 3D Systems provides manufacturing services from ISO 13485 facilities to help bring new products to market without requiring costly manufacturing line set-ups. The company has also enabled several medical device contract manufacturers with its technology, creating a robust supply chain. If or when a device manufacturer is ready, 3D Systems supports its customers with technology transfer to bring product manufacturing in-house. Manufacturers can adopt AM in the way that makes the most sense for them while both accelerating and de-risking their investment.
Ultimately, elevating patient care requires collaboration among device manufacturers, surgeons and additive manufacturing solution providers. The innovations that arise will meet the medical challenges of tomorrow with greater precision than ever before.
Ask our experts how 3D Systems’ 360-degree approach to additive manufacturing in healthcare may help you accelerate innovation.