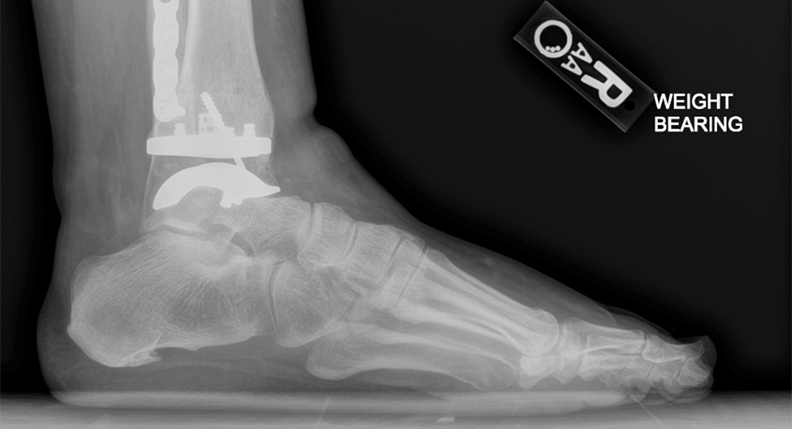
Total ankle arthroplasty is one of the fastest-growing arthroplasty segments, with a compound annual growth rate of 8.4% and $327 million in revenue anticipated by 2026.[1] There are currently 10 total ankle systems with FDA 510(k) clearances in the U.S., and three companies with patient-specific technology to accompany the implant.[2] The Exactech Vantage® Total Ankle System, one of the current total ankle designs, received its first FDA clearance in 2016.
Why an Ankle Solution Now?
In 2019, 3D Systems received FDA clearance for VSP Orthopaedics, a personalized solution for orthopedic applications. This surgical planning solution provides advanced visualization of anatomy and features nylon cutting guides produced via selective laser sintering (SLS) technology. 3D Systems elected to utilize SLS for orthopedic applications as it allows for the use of biocompatible nylon materials and provides a robust guide for larger bony anatomy. With the success of VSP Orthopaedics, 3D Systems chose to pursue other orthopedic products with the same technology and material.
3D Systems and Exactech have collaborated for more than a decade, since the development of the first FDA-cleared, 3D-printed orthopedic implant. The combination of 3D Systems’ VSP® surgical planning solution and Exactech’s Vantage Total Ankle System created the opportunity for innovative and collaborative development of patient-specific cutting guides. 3D Systems provided a proven digital workflow, additive manufacturing expertise and regulatory understanding, while Exactech provided implant system aptitude and an eager surgeon design team including Dr. Mark Easley, Dr. James DeOrio, Dr. James Nunley, Dr. Robert Santrock, Dr. Samuel Adams, Dr. Constantine Demetracopoulos and Dr. Jason Nowak. Together, this combination of knowledge and application development created Vantage® Ankle PSI.
Collaborating to Deliver Vantage Ankle PSI
3D Systems’ Application Innovation Group (AIG) accelerates the development of advanced applications and innovative additive manufacturing solutions. Taking a consultative approach, the AIG works to understand customer requirements from the start. Partnering with customers throughout the journey ensures the right solution is developed, enabling better outcomes for both the medical device company and the patient. The AIG’s regulatory experience in patient-specific applications of additive manufacturing facilitated the submission and clearance of the Vantage Ankle PSI.
How It Works
Vantage Ankle PSI was the second patient-specific total ankle system on the market in the U.S. and consists of cutting guides and anatomic models produced via SLS technology. The digital workflow begins with CT imaging data, segmented to create digital 3D models of the patient anatomy, then planned to employ each surgeon’s unique preferences, followed by device design. Once the design is complete, the patient-matched guides and model are 3D-printed on the SLS platform using the biocompatible nylon material. This combination of printer and material provides a repeatable and durable solution for the manufacture of anatomic models and guides. The cutting guides demonstrate consistent accuracy and ability to withstand surgical forces during benchtop and cadaveric studies.
Utilizing pre-operative planning and patient-specific tools, Vantage Ankle PSI aims to reduce time in the operating room and improve patient outcomes.[3, 4] 3D Systems’ team of engineers complete imaging segmentation, pre-surgical planning and design with interactive feedback from surgeons across the country as part of the VSP surgical planning workflow. The surgeon then receives anatomic models that allow them to confirm the fit of the patient-specific guides, which increases surgeon confidence during the procedure.[5] Vantage Ankle PSI cutting guides are uniquely designed to allow the surgeon to cut through the saw slots on each nylon guide, reducing the number of operative steps per case. Vantage Ankle PSI has been utilized by several surgeons to complete over 100 cases thus far in a limited pilot launch after FDA clearance.
Case Studies
Dr. Oliver Schipper and Dr. Constantine Demetracopoulos, two of the pilot launch surgeons that are utilizing the technology, have each completed multiple cases utilizing the Vantage Ankle PSI to date. The Vantage Ankle PSI solution allowed Dr. Schipper to address a challenging case with pre-existing hardware requiring deformity correction with good agreement between surgical plan and clinical outcome, as evidenced by the images below.
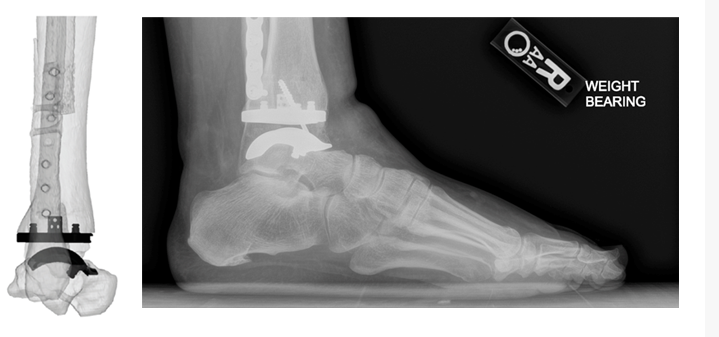
Dr. Schipper’s PSIs and final patient x-rays
“The Vantage Ankle PSI represents the next evolution of total ankle arthroplasty patient-specific instrumentation designed to allow surgeons to more accurately perform ankle replacement while saving time in the operating room,” said Dr. Schipper.
Additionally, Dr. Demetracopoulos said, “I have enjoyed adding the Vantage Ankle PSI to my practice. Using Vantage Ankle PSI increases my accuracy, makes the procedure more reproducible, and decreases my O.R. time. I have used Vantage Ankle PSI for both flat cut and curved talus implants and have been able to address deformity cases as well.”
Conclusion
Orthopedic surgery continues to offer many opportunities for innovation leveraging additive manufacturing and patient-specific workflows. Accelerating this innovation is the collaboration among experts in clinical care, patient-specific medical devices and additive manufacturing. Surgeons and their patients increasingly demand personalization of treatment that helps to improve surgical outcomes, and additive manufacturing combined with specialized software tools provide many solutions to these needs. Additive manufacturing technology is continually evolving with more efficient printers, innovative materials, software improvements and an increased capability at the point of care. While the technology has been utilized clinically for over a decade, it is clear that we are just at the cusp of what patient-specific products can do to improve patient care.
Ben Johnson is VP, Portfolio and Regulatory, Healthcare at 3D Systems and Zachary Wilczynski, M.S., serves as Senior Product Development Engineer, 3D Systems.
3D Systems provides comprehensive products and services, including 3D printers, print materials, software and on-demand manufacturing services for the healthcare industry.
1. https://www.medgadget.com/2019/09/total-ankle-replacement-market-2019-overview-industry-opportunities-and-outlook-to-2026.html
2. https://www.podiatrytoday.com/keys-maximizing-outcomes-fourth-generation-total-ankle-replacements
3. Patel A, Levine J, Brecht L, Saadeh P, Hirsch DL: Digital technologies in mandibular pathology and reconstruction. Atlas Oral Maxillofacial Surg Clin N Am 20:95-106, 2012
4. Roser SM, Ramachandra S, Blair H, Grist W, Carlson GW, Christensen AM, Weimer KA, Steed MB: The accuracy of virtual surgical planning in free fibula mandibular reconstruction: comparison of planned and final results. J Oral Maxillofac Surg 68:2824-2832, 2010
5. McCormick S, Drew S: Virtual model surgery for efficient planning and surgical performance. J Oral Maxillofac Surg 69:638-644, 2011