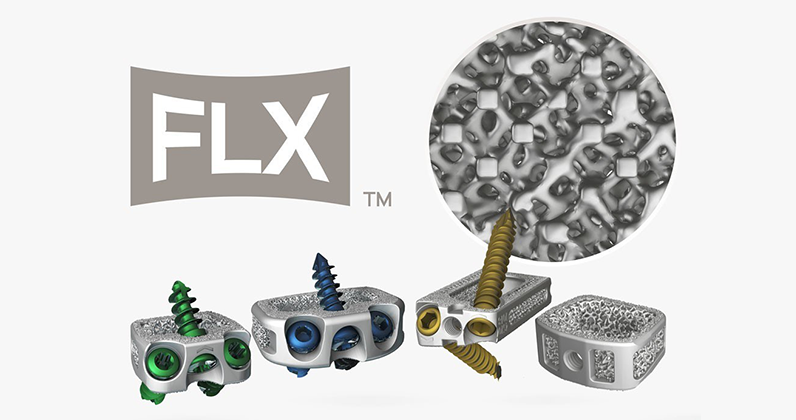
Optimizing designs and surfaces stands at the forefront of translational spinal research. Advancements in 3D printing technology allow for the precision manufacturing of implants with macro, micro and nano geometries, with complex structures that are not achievable utilizing traditional manufacturing methods. The ability to create interbody devices with such precise and unique geometries provides the potential to drastically enhance biomechanics and the fusion process.
As an industry-leading 3D printing manufacturer, Tangible Solutions has implemented Model-Based Definition (MBD) to create implants featuring complex structures and geometries. MBD is a strategic approach to creating 3D models that contain essential data needed to define a product, and produces a model that drives all engineering activities. The 3D model defines features that are desired (and not desired) in finished parts. Complex features such as lattice structures or roughened surfaces can easily be modeled in and finished products will have the modeled features exactly where intended.
Additive manufacturing (AM) can produce organic designs, stiffness control, surface roughness, textures and shapes and sustainable manufacturability. The lasting partnership between Centinel Spine®, LLC, and Tangible Solutions demonstrates the power of using Model-Based Definition, advanced printer technology and an experienced 3D printing contract manufacturer.
“At Centinel Spine, additive manufacturing technology enabled us to take interbody implants to a new level and provide highly porous 3D-printed options that overcome limitations with machined titanium implants. Our unique and highly porous, hydrophilic titanium structure is intended to promote rapid stability through cellular adhesion and osseointegration. We have taken advantage of advanced additive manufacturing to develop FLX™ 3D-printed porous titanium interbody devices,” said John Parry, Centinel Spine Fusion Product Development Leader.
FLX devices participate in the fusion process with a combination of macro, micro and nano structural characteristics that influence cellular events related to the production of new bone. Additionally, the texturized surface and proprietary FUSE-THRU™ osteoconductive trabecular scaffold built into these FLX devices are designed to improve cellular attachment and proliferation, to provide guided bone growth. The FUSE-THRU scaffold mimics the structure of trabecular bone, with a porosity and interconnected pores in size ranges that have been shown to be optimal for rapid and sustained bone growth.
“3D printing provides the opportunity to rethink the way implants can deliver better quality of life for patients in need of spinal fusion,” said Jamie Manos, Centinel Spine Fusion Product Director. “Creating a fully titanium implant with a complex lattice scaffold designed to enable bony on-growth, in-growth and thru-growth, with good imaging properties and a subsidence profile similar to PEEK is something that simply isn’t possible with traditional manufacturing methods, and is a game changer in the interbody space.”
3D printing also opens a pathway to easier implant customization in the future. This technology has enabled Centinel Spine to continue to be a pioneer in the anterior column space with the FLX portfolio of 3D-printed interbody devices, and offers customers an additional advanced material option to enable them to select the best option for each individual patient’s needs.
“With 3D printing, we have made the impossible, possible,” said Steve Sanderson, Centinel Spine VP of Marketing & Product Development. “Partnering with a 3D printing contract manufacturer with industry-leading expertise like Tangible Solutions is essential when a company wants to break manufacturing boundaries and produce their innovative designs, when they may not have the necessary production expertise, technology and machinery.”
Following the development of the unique and proprietary FLX implant designs, Centinel Spine and Tangible Solutions began to build a strong partnership. The FLX product development team was attracted to Tangible’s printing technology and commitment to quality manufacturing.
“Tangible Solutions employs Model-Based Definition as a strategic approach to creating 3D models that contain essential data needed to define a product, and these models drive all engineering activities. The advances in MBD and the use of highly advanced design software is becoming the standard of design in additive manufacturing,” said Adam Clark, Chief Executive Officer of Tangible
Solutions.
“The Product Development team at Centinel Spine did an outstanding job deploying advanced modeling techniques into the design of their FLX products,” said Chris Collins, Chief Operating Officer of Tangible Solutions. “They worked hand-in-hand with our team at Tangible to maximize manufacturability and efficiency while incorporating proprietary complex features such as digitally-defined rough surfaces and lattice structures. Designing for AM as well as necessary downstream processes is crucial to creating a truly unique, high-quality, consistent product. Centinel has done just that.”
Designs have never been limited by the innovative minds in the industry. Next-generation design and engineering software is expanding the medical device development and manufacturing horizon. The manufacturing partnership between Centinel Spine and Tangible Solutions is proof that today, the impossible is indeed possible.