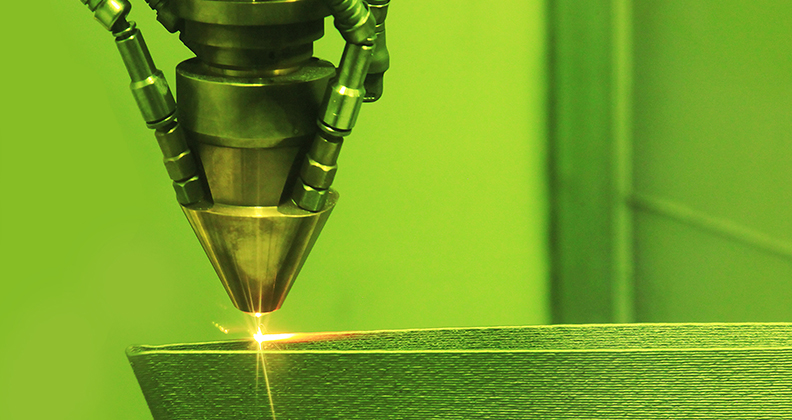
When orthopedic device companies venture into additive manufacturing, they often adopt one technology due to the immense capital, personnel and regulatory and quality investment. Companies essentially become brand agnostic and focus product development efforts so that their implant design and validation strategies meet the technology’s capabilities. Some in industry note that a greater focus on implant performance would push device companies to consider additional additive manufacturing types and, ultimately, lead to a proliferation of the technology in orthopedics.
4WEB Medical’s Lewis Harrison, Vice President of Research and Development, is skeptical of the idea of companies moving from one type of additive to the other, for many of the investment reasons noted above. “Medical device companies invest lots of time and resources into setting up manufacturing systems. This manufacturing setup requires validating equipment and processes to demonstrate control and the ability to reliably produce implants that are safe and effective. These implants then go through testing to ensure they are able to withstand necessary load requirements for the particular application, biocompatibility testing, sterilization testing, etc. The results of all of this testing is then submitted to FDA and other regulatory bodies to obtain clearance or approval to legally market the device in the specified country. If a company were to change additive technologies or brands, in most instances, they would be required to start the process all over again or at least perform significant testing/validations to demonstrate substantial equivalence. Therefore, I do not foresee medical device companies becoming more brand agnostic in this highly regulated industry.”
Randy Theken is the founder of the Theken Family of Companies, which includes NextStep Arthropedix; Theken recently sold its additive-focused contract manufacturer Slice Mfg to Avalign Technologies. Mr. Theken argued that companies that seek diversification in additive manufacturing processes have their hands tied because of limitations on materials that are used to create orthopedic implants. “You and I would both agree that with orthopedic companies, for the most part, 90%+ of what we put into the body is metal,” he said. “Metal is everything from titanium to cobalt-chrome. Any of these device companies today that are active in 3D printing are also active with regard to the metal side of 3D printing. That leaves you today with two options: Using a laser-based 3D printing technology or an electron beam 3D printing technology.”
Theken noted that there are important advantages and drawbacks for implant makers choosing between the two 3D-printed technologies, and that they’re generally limited to these options for the foreseeable future. But adopting a new additive manufacturing process comes with serious challenges, even if there are only two options to choose from. “Once a company goes down that road with a technology like this, it’s first very expensive. You put in a lot of resources, a lot of time, a lot of FDA validation. And once you take a path, because it’s medical and because it’s regulated by the government, it’s hard to go just jump on the next new horse that comes. But right now there are really only two horses.”
Some contract manufacturers are preparing for a broader approach to additive manufacturing in the future and believe it will be important for device companies and their partners to consider broadening their approaches to additive manufacturing.
Adam Clark, CEO of the contract manufacturer Tangible Solutions, said that the diversification of additive manufacturing processes is a matter of survival for device companies.
“What happened early is that companies were validating to a specific machine, a brand, and a serial number and really pigeonholing themselves to run everything on that machine. Instead of focusing on the output, they were messing around with the machines to achieve what was in their models,” he said.
Clark explained that diversifying his company’s machinery was essential for moving forward as a business and meeting customer needs. Diversification across multiple machines and platforms delivers flexibility and avoids backlogs, Clark argued. “As the parts come in, it doesn’t matter what platform they go on so long as all machines across the board are outputting the same results. So, when we do our validations of specific parts, we build the same, but they’ve got to look the same and have the same strength characteristics as other parts made differently. Being able to achieve that across different platforms gave us a lot of flexibility.”
Alan Dang, M.D., is the Chief Medical Officer of PrinterPrezz, a medical technology company that combines 3D printing with nano technologies to create spinal implants.
“We have invested in multiple technology platforms across every metric, including printers, software tools and materials,” he said. “We additionally invest in our workforce training and education and have ongoing benchmark development projects to expand the design envelope of medical device manufacturing.”
He argued that while it’s less burdensome initially for contract manufacturers to select single additive manufacturing methods, there are significant drawbacks to consider.
“It is certainly easier for a contract manufacturer to offer a single manufacturing technology because it’s cheaper, both in terms of capital equipment and real estate. It’s easier to train a workforce around a single machine or single set of software tools, in terms of time and money. However, that doesn’t provide the best performance when it comes to time and cost for the medical device design team. Medical device design teams should select manufacturing partners that share the same passion for patient care and continuing excellence and investment in education. Choosing an additive manufacturing process should be done at the device and application level. That is the only way to provide patients with the best available product.”
Judging from the perspectives of these experts, it’s clear that additive manufacturing is an incredibly complex issue for orthopedic device companies. Whether or not to invest time and money into multiple platforms, processes, and machines fully depends on the unique goals, resources and missions of each.
PM
Patrick McGuire is a BONEZONE Contributor.