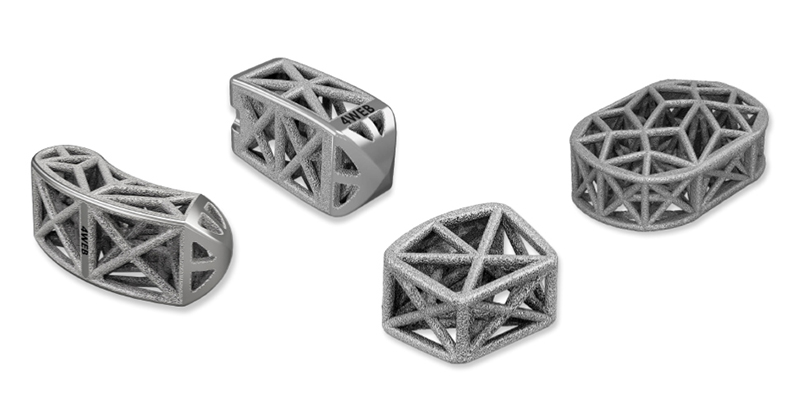
With additive manufacturing gaining greater adoption throughout the orthopedic device industry, many companies are asking which specific processes, machines and supplier networks best fit their unique needs. While most orthopedic device experts are familiar with the concept of additive manufacturing, there are multiple technologies to choose from, ranging from electron beam melting (EBM) to direct metal laser sintering (DMLS) to selective laser melting (SLM) and more.
The investment in additive is significant when you total the cost of machines, materials, software and, of course, personnel that possesses the expertise. Further, the investment requires regulatory and quality considerations that don’t afford a quick switch in technology. To learn more about how companies choose their additive manufacturing methods, we interviewed three industry members on how they made their decisions.
Design Freedom
Founded in 2008 in Dallas, Texas, 4WEB Medical drew on three decades of geometry research to bring lightweight, high-strength web structures to implant design. The company relies on additive manufacturing to produce its proprietary Truss Implant Technology.
“4WEB is using two types of additive manufacturing today for titanium orthopedic implants,” said Lewis Harrison, Vice President of Research and Development. “Our primary additive manufacturing technology is the GE Arcam EBM Q10plus. The Q10plus is used to produce our Spine Truss System, interbody fusion devices and Osteotomy Truss System implants. Additionally, we utilize the GE Concept Laser M2 for smaller scale parts such as our Hammertoe Truss System implants.”
For 4WEB, the decision to go with electron beam melting came down to functionality, superior throughput and the ability to produce hierarchical surface roughness.
“When 4WEB started producing implants via additive manufacturing in 2008, the Arcam EBM system was chosen over SLM systems at the time for several reasons,” Harrison said. “Primarily, the Arcam EBM system was able to produce the advanced structural design that is inherent to our Truss Implant Technology implants without requiring additional internal build supports. In contrast, the laser-based machines required a significant number of internal supports to be added to our truss design which could not be removed in post processing. Additionally, we were able to produce some proprietary build themes that took advantage of the hierarchical surface roughness produced with the EBM technology. We have several studies that show our surface features promote early fixation and stimulate an osteogenic cellular response. Finally, the EBM technology provides significantly higher throughput compared to the laser-based technologies, which is critical when doing short-run manufacturing of complete product lines comprised of 80 to 100 individual implants.”
All of 4WEB’s devices are additively manufactured; therefore, the decision of which technology to choose was significant to the company’s strategy. While cost, materials, throughput and manufacturer support were all important considerations when the company decided on an additive manufacturing process, design requirements were the driving factor behind their choice, Harrison said.
“There are distinct advantages between additive technologies that lend themselves to be more suited for particular design applications,” he said. “For example, most 3D-printed spinal interbody fusion devices on the market today are basic annular (ring) shaped designs with a micro lattice structure incorporated into the side walls of the implant. These generic lattice designs are well suited to SLM technologies because of the printing resolution of SLM and the minimal porosity between the struts in the lattice structures. 4WEB’s Truss Implant Technology and its advanced structural design are more suitable for EBM technology because the high temperature vacuum environment of the build chamber reduces residual stresses, decreases porosity within the material, and eliminates the need for complex internal build supports.”
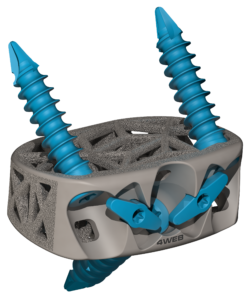
4WEB Medical STAND ALONE ANTERIOR SPINE TRUSS SYSTEM
Global Portfolio Adoption
As the largest orthopedic device company, it’s no surprise that DePuy Synthes and its parent company Johnson & Johnson are utilizing numerous types of additive manufacturing across various platforms.
“The key additive manufacturing technology platforms we are advancing are advanced metals and bio-ceramics, bio-absorbable and stimuli response (4D printing) polymers, 3D-printed electronics and sensors, 3D bioprinting and tissue regenerative solutions and personalized medicine applications for both clinical & OTC patients,” said Sam Onukuri, Head of 3D Printing Innovation & Customer Solutions at Johnson & Johnson. “These new capabilities are part of our ambition to fuel future growth and reimagine innovation globally.”
Onukuri said that through the embrace of 3D-printed technologies, his company now has the ability to create and manufacture products that were once thought to be unattainable, and is currently embedding their additive platforms within “point of care” settings where personalized implants and instruments can potentially be printed and delivered at or near hospitals and medical centers.
Among specific applications that DePuy Synthes is leveraging additive manufacturing is its TRUMATCH® Graft Cage – Long Bone, a 3D-printed personalized resorbable implant; the TomoFix surgical cutting guide, and the CONDUIT 3D, a porous spinal implant.
Gary Clerkin is Global Leader – Manufacturing Engineering, Science & Technology at DePuy Synthes. According to Clerkin, multiple factors should influence a company’s additive manufacturing strategy, including digital capabilities, materials, production costs, quality performance and the unique innovation pipeline of R&D teams. However, he pointed out that using a variety of 3D printing platforms was an asset for his company.
“The innovation curve for additive manufacturing is very exciting and we should not limit our thinking on the possibilities, especially when combined with other emerging technologies,” Clerkin said. “Agility and flexibility are important elements of a modern supply chain and therefore, the ability to have processes that are machine or technology agnostic will play a big part in the future. Advances in product, process and material characterization combined with innovations in end-to-end printing technology will enable much more flexibility than exists today.”
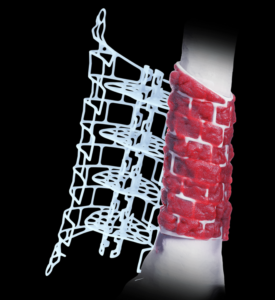
DePuy Synthes TRUMATCH
Strong Partners
Nick Slater, Chief Operating Officer at the startup Engage Surgical, said his company currently uses FDM (Fused Deposition Modeling) for printing early-stage plastic prototypes of implants and instruments and DMP (Direct Metal Printing) or DMLS to manufacture metal prototypes for evaluation and metal production implants.
“For metallic implant components, we spent time researching the various technologies and meeting with suppliers who had significant experience in additive methods,” Slater said in response to the question of how his company settled on its additive manufacturing strategy. “The final selection was made based on the production cost, lead time to manufacture, reliability of process, and existing clinical history.”
Since Engage Surgical’s inception in 2017, the company has relied on additive manufacturing methods to produce implants as well as instrument prototypes. “As a startup company, we don’t have the resources to invest in developing the in-house [additive manufacturing] capability. We outsource 100% of our additive manufacturing to vendors that specialize in this.”
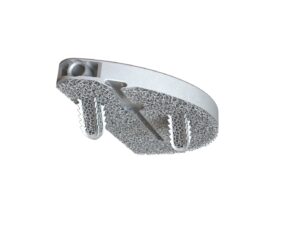
Engage Surgical partial knee system
Like Johnson & Johnson’s Onukuri, Slater said that on-demand additive manufacturing offered in point-of-care settings is a logical next step for the burgeoning technology. However, he believed it was “highly unlikely” that orthopedic and spine companies will become more brand agnostic in the future.
“The reason is that the switching costs are prohibitive,” he said. “Once a company goes through the effort of designing the part, developing and validating the additive process and getting regulatory approval, they have invested a significant amount of resources. There would have to be a very compelling reason to switch methods because any change of this type would introduce new and additional risk to the business, not to mention cost a significant amount of money.”
PM
Patrick McGuire is a BONEZONE Contributor.